Химическая физика, 2022, T. 41, № 3, стр. 57-67
Получение энергии и выделение редких металлов из зольного остатка при фильтрационном горении углей
Е. А. Салганский 1, В. М. Кислов 1, М. В. Цветков 1, *, А. Ю. Зайченко 1, Д. Н. Подлесный 1, М. В. Салганская 1, Х. М. Кадиев 2, М. Я. Висалиев 2, Л. А. Зекель 2
1 Институт проблем химической физики Российской академии наук
Черноголовка, Россия
2 Институт нефтехимического синтеза им. А.В. Топчиева Российской академии наук
Москва, Россия
* E-mail: tsvetkov@icp.ac.ru
Поступила в редакцию 29.06.2021
После доработки 14.07.2021
Принята к публикации 20.07.2021
- EDN: RUFNFR
- DOI: 10.31857/S0207401X22030104
Аннотация
Приведены результаты исследований выделения соединений ванадия, никеля и кобальта из зольного остатка, полученного в процессе фильтрационного горения древесного и бурого углей с последующим гидрометаллургическим извлечением металлов из зольных остатков. Для исследований использовали угли с предварительно нанесенными на них солями металлов. Изучены закономерности газификации исследуемых углей (температуры и скорости горения) и показано, что теплота сгорания газообразных продуктов для обоих видов углей составляет 4.3–4.5 МДж/м3. С помощью рентгенофазового анализа определены кристаллические структуры соединений металлов в зольных остатках. Проведено выщелачивание соединений металлов из зольного остатка водой, кислотами, перекисью водорода и их смесями. Установлено, что соединения ванадия практически полностью переходят в раствор при выщелачивании растворами кислот. Тогда как максимальные степени извлечения никеля и кобальта из зольных остатков газификации не превышали соответственно 59 и 61% для древесного угля и 40 и 28% для бурого угля. Это связано с тем, что в зольных остатках присутствуют соединения никеля и кобальта, стойкие к действию водных растворов кислот и других окислителей.
ВВЕДЕНИЕ
Благодаря специфическим физико-химическим свойствам редкоземельные элементы широко используются во многих высокотехнологичных приложениях (энергетика, электроника, космос и др.) [1]. Основной трудностью в получении редкоземельных элементов является отсутствие их концентрированных месторождений. К основным источникам получения редкоземельных элементов можно отнести минеральные руды [2], отработанную электронику [3] и т.д. В настоящее время все больше внимания обращают на угли и нефти, зола которых также содержит многие редкоземельные элементы, в особенности металлы [4]. Для селективного выделения редкоземельных элементов разрабатываются различные методы: экстракционные [5], сорбционные [6, 7], металлургические [8, 9], биологические [10, 11] и др.
Угли и нефтекоксы широко используются в энергетике. Газификация является эффективным методом получения энергии из твердых топлив. Газификация топлив может проводиться как в автотермическом [12–14], так и в аллотермическом режимах [15, 16]. Ранее исследование характеристик горения и массопереноса металлсодержащих продуктов в режиме фильтрационного горения было проведено в работах [17, 18]. При газификации твердых топлив в режиме фильтрационного горения наблюдается так называемый “сверхадиабатический эффект”, обусловленный теплообменом между реагентами и продуктами [19, 20]. Преимуществами сверхадиабатического метода газификации твердых топлив по сравнению с известными техническими решениями являются: высокий энергетический КПД процесса, позволяющий перерабатывать низкокалорийные смеси, низкое содержание токсичных веществ в газообразных продуктах сгорания [21–23].
Для извлечения V, Ni и Со из зольного остатка предложен ряд технологических процессов, которые можно разделить на пирометаллургические и гидрометаллургические. Пирометаллургические методы переработки золы включают хлорирование либо восстановительную плавку с получением сплавов соединений V и других металлов [24, 25]. Для осуществления хлорирования зольных продуктов, собранных после газификации углей или других видов твердых топлив, в их составе должен присутствовать углерод. В промышленных образцах зольных продуктов углеродные частицы всегда содержатся в виде недожога. Указывается [26], что первоначально проводится гранулирование золошлаковых отходов (ЗШО). Хлорирование гранул рекомендуется осуществлять при температурах 500–700 °С в расплаве солей KCl и NaCl. Например, хлорирование соединений V (600–700 °С) описывается уравнением
После охлаждения продуктов хлорирования можно провести либо дробную конденсацию отдельных хлорсодержащих соединений V, Ni и Со, различающихся температурами конденсации, либо получение их смесей, из которой посредством ректификации выделяются чистые соединения металлов. Процесс хлорирования различных видов сырья используется в промышленном масштабе во многих странах, в том числе в России.
Другим способом переработки зольных продуктов является выплавка сплавов рассматриваемых металлов с соединениями железа с получением ферросплавов, содержащих ванадий, ферроникель, кобальт [27, 28]. Наиболее перспективными представляются способы гидрометаллургической переработки, позволяющие использовать золу с низким содержанием соединений рассматриваемых металлов. Извлечение V, Ni и Со из золы угля гидрометаллургическими способами может быть проведено путем кислотного [29], щелочного или водного выщелачивания [30–33]. Гидрометаллургический метод извлечения был использован в России в промышленном масштабе на заводе “Тулачермет” для получения V2O5 из собранных ЗШО после сжигания мазутов. Наиболее полно гидрометаллургические способы изучены в работах В.И. Букина с сотр. [34].
В патенте [35] предлагается способ переработки, полученных после сжигания мазутов ЗШО, заключающийся в смешивании их с карбонатом натрия и водой. Далее полученную смесь выдерживают при постоянной температуре в интервале 100–150 °С (в печи) в течение 2 ч с получением спека. Из высушенного “саморассыпающегося” спека степень извлечения V посредством водного выщелачивания при температуре 95–100 °С составляет 73–74%.
Способ выщелачивания V и Ni из зольного остатка соляной кислотой был запатентован в США [36]. Согласно этому способу зольный остаток смешивали с соляной кислотой, суспензию фильтровали, фильтрат обрабатывали гидроксидом натрия, калия или кальция, повышая pH раствора до 5.5–6.5. При этом выпадал осадок, содержащий соединения V, который отфильтровывали и затем дополнительно выщелачивали при pH = 8.5–9.5, выделяя в осадок гидроксид никеля. Осадок, содержащий соединения ванадия, сушили, смешивали с гидроксидом натрия, калия или кальция, а затем смесь прокаливали на воздухе при 500–1000 °C. В результате получался твердый продукт, содержащий пятивалентный ванадий, который выщелачивали водой и фильтровали. Фильтрат подкисляли соляной кислотой и осаждали V2O5.
В работе [37] предложен электрохимический метод выщелачивания соединения ванадия из зольного остатка с использованием в качестве электролита водных растворов хлоридов и карбонатов щелочных металлов. Метод не представляется приемлемым, поскольку электролиты, содержащие хлорид-ионы, вызывают коррозию аппаратуры, а использование карбонатов связано с трудностью регенерации отработанного электролита.
Выбор реагента и условия проведения гидрометаллургической переработки зольных остатков с целью извлечения соединений металлов зависят от вещественного состава остатков, условий проведения газификации и элементного состава исходного угля. Термодинамическая оценка распределения между фазами соединений рассматриваемых металлов (кобальта, никеля, ванадия) показала, что данные металлы в условиях волны фильтрационного горения должны оставаться в твердой фазе в виде оксидных форм.
Цели работы – исследование возможности повышения степени полезного использования твердого топлива (угля) путем комплексной переработки ресурсов и получения тепла при газификации углей с последующим выделением редких металлов из зольного остатка.
ЭКСПЕРИМЕНТАЛЬНАЯ ЧАСТЬ
Аналитические методы исследования
Элементный анализ органической массы угля проводили методом сжигания в потоке кислорода на элементном CHNS/O-анализаторе “Vario MICRO cube” фирмы “Elementar Analysensystem GmbH” (Germany) с динамическим диапазоном регистрации элементов от 0.01 до 100%. Содержание влаги в углях определяли по ГОСТ Р 52911-2013 “Топливо твердое минеральное. Определение общей влаги”, содержание золы – по ГОСТ Р 55661-2013 “Топливо твердое минеральное. Определение зольности”. Анализ газообразных продуктов фильтрационного горения углей осуществляли с помощью газового хроматографа Хроматэк Кристалл-5000.2 производства ЗАО СКБ “Хроматэк” (Россия).
Определение содержаний соединений V, Ni и Co в модельных образцах углей, зольных остатках после выщелачивания золы и фильтратах проводили на рентгенофлуоресцентном спектрометре ARL PERFORM’X Sequential XRF компании TERMO FISHER SCIENTIFIC (USA) и эмиссионном спектрометре с индуктивно-связанной плазмой ICPE-9000 компании SHIMADZU (Japan). Исследование фазового состава зольных остатков проводили на рентгенофазовом дифрактометре Rotaflex RU-200 производства компании Rigaku (Japan), работающем при следующих параметрах источника: 50 кВ, 160 мА. Длина волны монохроматизированного излучения составляла 1.542 Å. Для монохроматизации использовался графитовый кристалл-монохроматор на отраженном от образца пучке. Источник оснащен горизонтальным гониометром Rigaku D/Max RC, θ–2θ-сканирование проводили по схеме Брэгга–Брентано в угловом диапазоне 2θ = 10°–70°. Измерение велось в режиме непрерывного сканирования со скоростью 2°/мин и шагом 0.04°. Обработку экспериментальных дифрактограмм проводили с помощью специализированной программы MDI Jade 6.5. Для идентификации фаз использовали международную электронную базу дифракционных данных ICDD PDF-2.
Методика приготовления образцов углей
В качестве модельных образцов угля были выбраны древесный уголь (ГОСТ 7657-84) и сернистый уголь Подмосковного бассейна Кимовского разреза (бурый уголь). Размер частиц древесного угля составлял 3–5 мм, бурого угля – 3–7 мм. Исходный уголь высушивали до абсолютно сухого состояния, после чего взвешивали на лабораторных электронных весах ВСТ-600/10.
Угли пропитывали следующими солями кобальта, никеля и ванадия:
1) кобальт(II) азотнокислый шестиводный (Co(NO3)2 ∙ 6H2O, ГОСТ 4528-78, чистота – не менее 99%).
2) никель(II) азотнокислый шестиводный (Ni(NO3)2 ∙ 6H2O, ГОСТ 4055-78, чистота – не менее 98%).
3) метаванадат аммония (NH4VO3, ГОСТ 9336-75, чистота – не менее 99%).
Количество добавки солей металлов рассчитывали таким образом, чтобы содержание металла в угле составляло 0.1 мас.%. Навески солей металлов взвешивали на аналитических весах с наименьшим пределом взвешивания, составлявшим 0.0001 г.
Соли металлов растворяли в дистиллированной воде, выбирая объем воды таким образом, чтобы уголь был полностью погружен в раствор. Легкорастворимые в воде соли кобальта и никеля растворяли в холодной воде, а метаванадат аммония – в горячей воде.
Сухой уголь засыпали в широкую кювету и заливали приготовленным раствором. После того как часть раствора поглощалась углем, остаток раствора сливали в стеклянный стакан, а влажный уголь ставили в сушильный шкаф. Высушенный уголь вновь пропитывали остатком раствора, перемешивали и снова сушили, повторяя данную процедуру до полного впитывания всего раствора. Завершающими стадиями были: смывание небольшим количеством воды осевшего при испарении раствора растворенного вещества на стенках кюветы, пропитка им угля и сушка угля до абсолютно сухого состояния в сушильном шкафу при температуре 105 °С. Перед сжиганием из общей массы пропитанного угля выбирали представительную пробу, которую растирали в ступке и анализировали на содержание металлов.
Методика выщелачивания зольного остатка
Перед проведением анализов, а также экспериментального изучения возможности извлечения соединений V, Ni и Co из золы углей в раствор зольные продукты подвергались механическому измельчению до аналитической крупности в фарфоровой ступке. Выщелачивание проводили в плоскодонной колбе объемом 300 мл, помещенной на магнитную мешалку с подогревом. Навеску золы массой 2 г загружали в колбу, далее добавляли выщелачивающий реагент при разном массовом соотношении золы (Т) и выщелачивающего раствора (Ж): от 1/10 до 1/30. Обработку проводили при температуре 60 °С в течение 2 ч. Далее полученную суспензию отфильтровывали на воронке Бюхнера. Фильтр с отфильтрованным материалом промывали водой, сушили, а затем взвешивали и определяли массу для составления баланса. Далее от твердого остатка в фильтре брали пробу и определяли содержание V, Ni и Со и по полученным данным их содержаний в исходной золе и остатке на фильтре определяли степень их извлечения.
В качестве реагентов для выщелачивания использовали следующие вещества:
– H2O дистиллированная;
– 25% NH4OH (ГОСТ 3760-79) + 5% (NH4)2CO3 и 25% NH4OH + 10% (NH4)2CO3;
– H2O2 с концентрацией 37% (ГОСТ 177-88);
– H2SO4 с концентрацией 95% (ГОСТ 4204-77) и 20%;
– HNO3 с концентрацией 65% (ГОСТ 4461-77);
– смесевой раствор, содержащий 650 г/л H2SO4 и 250 г/л HNO3;
– HCl с концентрацией 35–38% (ГОСТ 3118-77);
– раствор NaOH с концентрацией 20%.
МЕТОДИКА ЭКСПЕРИМЕНТА
Экспериментальные исследования по фильтрационному горению металлсодержащих углей проводили на лабораторной установке периодического действия, схема которой представлена на рис. 1. Основная часть экспериментальной установки – вертикально расположенный цилиндрический реактор 3, выполненный из кварцевого стекла, с внутренним диаметром 66 мм, толщиной стенки 3 мм и длинной 500 мм. Для снижения боковых радиационных теплопотерь внешняя стенка реактора экранировалась теплоотражающим экраном 4.
Рис. 1.
Схема экспериментальной установки: 1 – ПК, 2 – аналого-цифровой преобразователь, 3 – кварцевый реактор, 4 – теплоотражающий экран, 5 – электронный расходомер, ТП1–ТП6 – термопары.

Исследуемые образцы углей загружали в реактор через верхний торец. Воздух подавали через штуцер в нижнем торце реактора. Расход воздуха контролировали с помощью электронного расходомера “Mass-view” 5 (рис. 1) компании Bronkhorst High-Tech (Netherlands). Продукт-газ выводился через верхний торец реактора.
Перед началом эксперимента в реактор загружали слой инертного материала до уровня первой термопары (ТП1). В качестве инертного материала использовали керамические корундовые шарики диаметром 5–7 мм. Поверх слоя керамических шариков засыпали инициирующий состав, представляющий собой нагретую в муфельной печи до ~800 °С смесь древесного угля (10 г) с инертным материалом (30 г). После чего начинали подачу окислителя (воздуха) в реактор. При этом начиналось горение инициирующего состава. Расход воздуха во всех экспериментах поддерживали постоянным и равным 800 м3/м2 ∙ ч (0.76 л/с).
Далее проводили загрузку исследуемой смеси небольшими порциями (~50 г). Спустя 5–7 мин формировался стационарный фронт горения, который характеризовался постоянными скоростью и температурой горения. Распространение фронта волны фильтрационного горения по реактору регистрировали по показаниям шести хромель-алюмелевых термопар (ТП1–ТП6), расположенных по длине реактора на расстоянии 65 мм друг от друга. Спай термопар располагался по центру реактора. Показания термопар передавались через АЦП 2 на регистрирующий компьютер 1 (рис. 1) и отображались на экране монитора в режиме реального времени.
Массовую скорость горения определяли по регистрируемому с помощью термопар продвижению фронта горения и по убыли массы топлива в ходе эксперимента. Во всех экспериментах периодически проводили отбор проб газообразных продуктов в стеклянную ампулу-ловушку. После эксперимента из реактора выгружали твердые продукты сгорания, отделяли золу, растирали ее в ступке и анализировали согласно вышеописанной методике.
РЕЗУЛЬТАТЫ И ИХ ОБСУЖДЕНИЕ
Элементный состав исходных углей приведен в табл. 1. В отличие от древесного угля бурый уголь характеризуется высокой зольностью и низкой теплотворной способностью.
Таблица 1.
Характеристики используемых углей
Параметр | C, % | H, % | O, % | N, % | S, % | Зола, % | Q, МДж/кг |
---|---|---|---|---|---|---|---|
Древесный уголь | 91.20 | 3.65 | 3.64 | 0.01 | – | 1.5 | 34.1 |
Бурый уголь | 42.57 | 3.82 | 23.13 | 0.78 | 2.70 | 27.0 | 13.0 |
Анализ содержания металлов в подготовленных образцах углей и их золе представлен в табл. 2. Зольные остатки газификации бурого и древесного углей, пропитанные солями ванадия, никеля и кобальта, могут быть использованы для изучения процессов их извлечения. Содержание всех трех металлов по отдельности в золе древесного угля выше, чем их содержание в золе бурого угля из-за значительной разности в зольности углей. В ряде случаев наблюдали пониженное содержание металлов в золе углей вследствие их малой концентрации в исходных образцах и потерь при разгрузке из реактора зольного остатка.
Таблица 2.
Содержание металлов V, Ni, Co в углях и золе
Наименование пробы | Содержание, % | ||
---|---|---|---|
V | Ni | Co | |
Древесный уголь, пропитанный NH4VO3 | 0.10 | – | – |
Бурый уголь, пропитанный NH4VO3 | 0.10 | – | – |
Древесный уголь, пропитанный Ni(NO3)2 ∙ 6H2O | – | 0.09 | – |
Бурый уголь, пропитанный Ni(NO3)2 ∙ 6H2O | – | 0.11 | – |
Древесный уголь, пропитанный Co(NO3)2 ∙ 6H2O | – | – | 0.76 |
Бурый уголь, пропитанный Co(NO3)2 ∙ 6H2O | – | – | 0.96 |
Древесный уголь, пропитанный смесью солей V, Ni, Co | 0.17 | 0.10 | 0.09 |
Зола древесного угля, пропитанного NH4VO3 | 11.34 | – | – |
Зола бурого угля, пропитанного NH4VO3 | 1.19 | – | – |
Зола древесного угля, пропитанного Ni(NO3)2 ∙ 6H2O | – | 2.96 | – |
Зола бурого угля, пропитанного Ni(NO3)2 ∙ 6H2O | – | 1.06 | – |
Зола древесного угля, пропитанного Co(NO3)2 ∙ 6H2O | – | – | 7.05 |
Зола бурого угля, пропитанного Co(NO3)2 ∙ 6H2O | – | – | 1.35 |
Зола древесного угля, пропитанного смесью солей V, Ni и Co | 2.12 | 1.12 | 1.00 |
Зола бурого угля, пропитанного смесью солей V, Ni и Co | 1.19 | 1.40 | 1.09 |
Помимо внесенных нами металлов, в пропитанных углях также присутствуют некоторые химические элементы, которые содержались в исходных углях (табл. 3). Эти элементы согласно рентгенофазовому анализу не образуют кристаллических фаз с рассматриваемыми металлами.
Таблица 3.
Содержание в углях прочих химических элементов
Вид угля | Al, % | Si, % | Fe, % | Ca, % | Na, % | Mg, % |
---|---|---|---|---|---|---|
Древесный уголь | до 0.04 | 0.06–0.39 | 0.01–0.02 | 0.10–0.19 | до 0.20 | до 0.04 |
Бурый уголь | 2.40–3.37 | 1.66–2.40 | 0.53–0.81 | 0.16–0.20 | до 0.70 | до 0.04 |
При воздушной газификации древесного угля температура горения составляла ~1200 °С, массовая скорость горения – 0.14 г/с, а теплотворная способность газообразных продуктов – 4.5 МДж/м3 (табл. 4). В случае бурого угля температура и скорость горения были выше, чем у древесного угля. Это обусловлено более высоким содержанием золы, в результате чего реализовалась переходная структура волны горения, характеризующаяся более высокими значениями температур и скоростей горения. Однако теплота сгорания газообразных продуктов несколько ниже, чем у древесного угля и составляет ~4.3 МДж/м3. Однако в отличие от древесного угля продукты газификации бурого угля, кроме газообразных продуктов, содержат горючие органические продукты термического разложения (пиролиза) угля – смолы (элементный состав, мас.%: С – 74.8%, H – 7.6%, O – 13.0%, N – 1.1%, S – 3.5%). Выход продуктов пиролиза в значительной мере определяется температурным режимом проведения процесса [38, 39]. В наших экспериментах выход пиролизных смол составил ~8% от исходной массы бурого угля. Теплота сгорания последних составляет ~32 МДж/кг.
Таблица 4.
Характеристики газификации углей
Вид угля | Вид металла | Т, °С | Vгор, г/с | Q, МДж/м3 |
---|---|---|---|---|
Древесный | V | 1178 | 0.13 | 4.15 |
Co | 1155 | 0.14 | 4.68 | |
Ni | 1165 | 0.15 | – | |
V + Co + Ni | – | 0.15 | 4.49 | |
Бурый | V | 1319 | – | 4.27 |
Co | 1293 | 0.57 | 4.26 | |
Ni | 1257 | 0.53 | 4.24 | |
V + Co + Ni | – | 0.54 | – |
Согласно данным рентгенофазового анализа золы древесного (рис. 2) и бурого (рис. 3) углей, пропитанных солями V, Ni и Co, в образцах присутствуют как индивидуальные оксидные формы указанных металлов, так и их сложные соединения. В образце золы древесного угля, пропитанного солями V, Ni и Co, основными идентифицированными фазами являются VO2, NiO, NiTiO3, CoO, CaO, Ca2SiO4, CaSO4, SiO2, а в образце золы бурого угля, пропитанного такими же солями такими фазами являются VO2, NiO, NiS2, NiCo2O4, Co3O4, Co2C, CaCO3, TiO2, Al6Si2O13, Fe2O3.
Рис. 2.
Рентгенограмма золы, полученной после газификации древесного угля, пропитанного солями V, Ni и Co: 1 – CaO, 2 – CoO, 3 – NiO, 4 – Ca2SiO4, 5 – SiO2, 6 – NiTiO3, 7 – VO2, 8 – CaSO4.
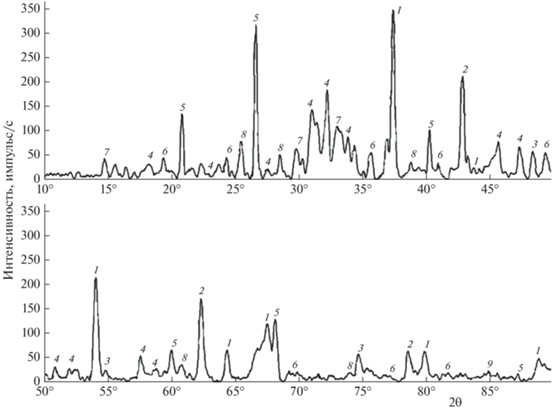
Рис. 3.
Рентгенограмма золы, полученной после газификации бурого угля, пропитанного солями V, Ni и Co: 1 – Fe2O3, 2 – Al6Si2O13, 3 – TiO2, 4 – CaCO3, 5 – Co3O4, 6 – NiO, 7 – NiS2, 8 – NiCo2O4, 9 – Co2C, 10 – VO2.
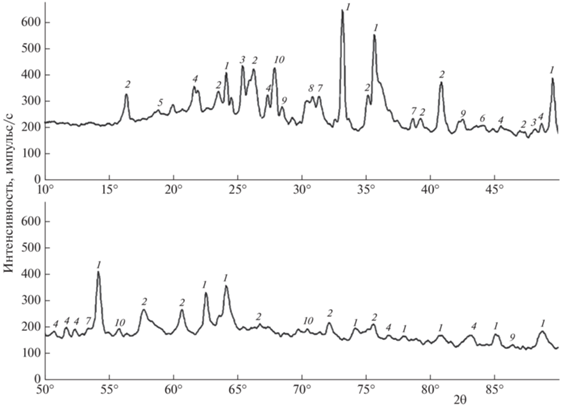
Зольные остатки, полученные после газификации углей, пропитанных соединениями V, Ni и Co, характеризуются высоким содержанием указанных металлов, а вещественный состав (рис. 2 и 3) показывает, что в образцах присутствуют трудноизвлекаемые соединения некоторых рассматриваемых металлов (NiTiO3, NiS2, NiCo2O4, Co2C). Полученные зольные остатки газификации древесного и бурого углей, пропитанные солями V, Ni и Co, представляли собой неоднородные продукты. Фотографии золы бурого угля до и после измельчения приведены на рис. 4 и 5 .
Выбранные реагенты имеют разное влияние на степень извлечения соединений ванадия, никеля и кобальта (табл. 5). Так, например, при действии 20%-ного раствора NaOH, дистиллированной воды, смеси NH4OH и (NH4)2CO3 на золу бурого угля степени извлечения V, Ni и Со не превышают 54, 34 и 22% соответственно. При действии сильных кислот (H2SO4, HNO3, HCl и их смеси) уже на первой стадии обработки повышается степень извлечения V до 73–76%, при этом снижается извлечение Ni до 29–30%, а степень извлечение соединений Со практически не изменяется. При проведении дополнительных стадий выщелачивания (двух-трех стадий) достигается практически полное извлечение в раствор соединений ванадия, а также повышается степень извлечения соединений никеля и кобальта. Наиболее высокое значение степени извлечения соединений никеля (35%) и кобальта (25.5%) достигается при двухстадийном выщелачивании при использовании в качестве реагента HCl и смеси HCl с H2SO4 и HNO3.
Таблица 5.
Степень извлечения в раствор соединений ванадия, никеля и кобальта из золы сжигания углей
Реагент | Т/Ж | Степень извлечения, % (по анализу остатка) |
|||
---|---|---|---|---|---|
V | Ni | Co | |||
Объект исследований: зола бурого угля | |||||
H2O | 1/20 | 40.2 | 33.4 | 20.8 | |
25% NH4OH + 10% (NH4)2CO3 | 1/10 | 53.4 | 33.0 | 21.9 | |
раствор NaOH (20%) | 1/10 | 38.2 | 33.5 | 19.1 | |
H2SO4 (концентрация – 95%) | 1/30 | 77.1 | 37.2 | 22.4 | |
H2SO4 (95%) + H2O2 (37%) | 1/10 | 72.5 | 30.2 | 25.1 | |
H2O2 (37%) | 1/10 | 44.4 | 36.7 | 21.9 | |
H2SO4 (95%) | 1-я стадия | 1/10 | 73.6 | 29.7 | 22.6 |
2-я стадия | 1/10 | 15.9 | 3.6 | 0 | |
3-я стадия | 1/10 | 1.8 | 0 | 0 | |
H2SO4 (20%) | 4-я стадия | 1/10 | 1.6 | 0 | 0 |
ИТОГО: | – | 92.9 | 33.3 | 22.6 | |
HNO3 (65%) | 1-я стадия | 1/10 | 75.9 | 8.0 | 16.9 |
2-я стадия | 1/10 | 13.2 | 3.5 | 9.7 | |
3-я стадия | 1/10 | 10.5 | 0 | 0 | |
H2SO4 (20%) | 4-я стадия | 1/10 | 0.3 | 0 | 0 |
ИТОГО: | – | 99.9 | 11.5 | 26.6 | |
650 г/л H2SO4/350 г/л HNO3 | 1/10 | 77.1 | 33.5 | 23.8 | |
HCl | 1-я стадия | 1/10 | 77.2 | 28.0 | 17.8 |
H2SO4 (93%) | 2-я стадия | 1/10 | 21.4 | 9.2 | 4.8 |
ИТОГО: | – | 98.6 | 37.2 | 22.6 | |
HCl | 1-я стадия | 1/10 | 77.2 | 28.0 | 17.8 |
HNO3 (65%) | 2-я стадия | 1/10 | 19.1 | 11.2 | 10.3 |
ИТОГО: | – | 96.3 | 39.2 | 28.1 | |
HCl | 1-я стадия | 1/10 | 77.2 | 28.0 | 17.8 |
NH4OH (25%) | 2-я стадия | 1/10 | 16.7 | 10.4 | 3.5 |
ИТОГО: | – | 93.9 | 38.4 | 21.3 | |
HNO3/HCl (1/3) | 1-я стадия | 1/10 | 79.2 | 29.7 | 17.7 |
H2SO4 (93%) | 2-я стадия | 1/10 | 17.0 | 5.2 | 5.3 |
ИТОГО: | – | 96.2 | 34.9 | 24.0 | |
HNO3/HCl (1/3) | 1-я стадия | 1/10 | 79.2 | 29.7 | 17.7 |
HNO3 (65%) | 2-я стадия | 1/10 | 12.7 | 3.8 | 0.7 |
ИТОГО: | 91.9 | 33.5 | 18.4 | ||
HNO3/HCl (1/3) | 1-я стадия | 1/10 | 79.2 | 29.7 | 17.7 |
NH4OH (25%) | 2-я стадия | 1/10 | 14.7 | 2.6 | 7.6 |
ИТОГО: | – | 93.9 | 32.3 | 25.3 | |
Объект исследований: зола древесного угля | |||||
H2O | 1/20 | 41.8 | 48.1 | 27.6 | |
раствор NaOH (20%) | 1/10 | 41.0 | 50.0 | 26.0 | |
H2SO4 (95%) | 1-я стадия | 1/10 | 92.5 | 57.4 | 60.0 |
2-я стадия | 1/10 | 2.3 | 1.4 | 0.7 | |
3-я стадия | 1/10 | 1.2 | 0 | 0 | |
ИТОГО: | – | 96.0 | 58.8 | 60.7 | |
HNO3 (65%) | 1-я стадия | 1/10 | 93.6 | 55.1 | 60.0 |
2-я стадия | 1/10 | 2.5 | 3.8 | 1.2 | |
3-я стадия | 1/10 | 0.9 | 0 | 0 | |
ИТОГО: | – | 97.0 | 58.9 | 61.2 | |
650 г/л H2SO4/250 г/л HNO3 | 1/10 | 93.5 | 55.5 | 59.8 |
Влияние состава растворов на степень извлечения металлов при выщелачивании золы древесного угля согласуется с результатами, полученными при выщелачивании золы бурого угля, однако во всех экспериментах степень извлечения соединений Ni и Со существенно выше, что связанно, по-видимому, с разницей вещественных составов полученных зольных остатков. В получаемый раствор после четырехстадийной обработки также переходят соединения некоторых элементов (Na, Са, K и др.), содержащихся в исходном сырье.
По-видимому, невысокая степень извлечения Ni и Co из исследованных образцов зольных остатков связана с образованием при газификации соединений (NiTiO3, NiS2, NiCo2O4, Co2C), без проведения дополнительной термохимической обработки которых (спекании, хлорировании и т.д.) практически невозможно увеличить степень извлечения соединений указанных металлов.
ВЫВОДЫ
Выполненные исследования показали, что скорость и температура фильтрационного горения бурого угля Подмосковного бассейна выше, чем древесного угля. В результате фильтрационного горения обоих типов углей получается газ с теплотой сгорания 4.3–4.5 МДж/м3. При фильтрационном горении бурого угля также образуется смола с теплотой сгорания, составляющей ≈32 МДж/кг, выход которой составляет примерно 8% от массы исходного угля.
Определены кристаллической структуры соединений металлов в зольных остатках углей. Выполнены эксперименты по выщелачиванию соединений металлов водой, кислотами, перекисью водорода и их смесями. Установлено, что соединения ванадия практически полностью (97–98%) переходят в раствор при двух-трехстадийном выщелачивании растворами кислот. В зольных остатках присутствуют соединения никеля и кобальта, стойкие к действию водных растворов кислот и окислителей. Вследствие этого максимальные степени извлечения никеля и кобальта из зольных остатков не превышали 59–61%.
Часть анализов проводилась на оборудовании АЦКП ИПХФ РАН и ИНХС РАН.
Исследование выполнено при финансовой поддержке Российским фондом фундаментальных исследований в рамках научного проекта № 18-29-24029-мк и госзадания № 0089-2019-0018 (регистрационный номер АААА-А19-119-022690098-3).
Список литературы
Chakhmouradian A.R., Wall F. // Elements. 2012. V. 8. P. 333; https://doi.org/10.2113/gselements.8.5.333
Demol J., Ho E., Soldenhoff K. et al. // Hydrometallurgy. 2019. V. 188. P. 123; https://doi.org/10.1016/j.hydromet.2019.05.015
Jowitt S.M., Werner T.T., Weng Z. et al. // Curr. Opin. Green Sustain. Chem. 2018. V. 13. P. 1; https://doi.org/10.1016/j.cogsc.2018.02.008
Салганский Е.А., Цветков М.В., Кадиев Х.М. и др. // ЖПХ. 2019. Т. 92. № 12. С. 1514; https://doi.org/10.1134/S0044461819120028
Исаева Ю.И., Елохов А.М., Денисова С.А. и др. // ЖПХ. 2020. Т. 94. № 7. С. 1006.
Громов В.Ф., Иким М.И., Герасимов Г.Н. и др. // Хим. физика. 2021. Т. 40. № 1. С. 55; https://doi.org/10.31857/S0207401X21010039
Touré M., Chamieh J., Arrachart G. et al. // Sep. Purif. Technol. 2020. V. 251. P. 117330; https://doi.org/10.1016/j.seppur.2020.117330
Tan Q., Li J., Zeng X. // Crit. Rev. Environ. Sci. Technol. 2015. V. 45. № 7. P. 749; https://doi.org/10.1080/10643389.2014.900240
Lu Y., Xu Z. // Resour. Conserv. Recycl. 2016. V. 113. P. 28; https://doi.org/10.1016/j.resconrec.2016.05.007
Hennebel T., Boon N., Maes S. et al. // New Biotechnol. 2015. V. 32. № 1. P. 121; https://doi.org/10.1016/j.nbt.2013.08.004
Lee J.C., Pandey B.D. // Waste Manag. 2012. V. 32. № 1. P. 3; https://doi.org/10.1016/j.wasman.2011.08.010
Ripoll N., Salgansky E., Toledo M. // Intern. J. Heat Mass Transfer. 2021. V. 177. 121472; https://doi.org/10.1016/j.ijheatmasstransfer.2021.121472
Сеплярский Б.С., Абзалов Н.И., Кочетков Р.А. и др. // Хим. физика. 2021. Т. 40. № 3. С. 23; https://doi.org/10.31857/S0207401X21030109
Fierro M., Requena P., Salgansky E. et al. // Chem. Eng. J. 2021. V. 425. P. 130178; https://doi.org/10.1016/j.cej.2021.130178
Antonov D.V., Valiullin T.R., Iegorov R.I. et al. // Energy. 2017. V. 119. P. 1152; https://doi.org/10.1016/j.energy.2016.11.074
Solomatin Ya., Shlegel N.E., Strizhak P.A. // Fuel. 2019. V. 255. P. 115751; https://doi.org/10.1016/j.fuel.2019.115751
Заславский Г.Е., Лемперт Д.Б., Манелис Г.Б. // Хим. физика. 2014. Т. 33. № 1. С. 14; https://doi.org/10.7868/S0207401X14010142
Lutsenko N.A., Salgansky E.A. // Intern. J. Multiphas. Flow. 2021. V. 140. P. 103670; https://doi.org/10.1016/j.ijmultiphaseflow.2021.103670
Evseev N., Ziatdinov M., Romandin V. et al. // Processes. 2020. V. 8. № 9. P. 1056; https://doi.org/10.3390/pr8091056
Salgansky E.A., Zaichenko A.Y., Podlesniy D.N. et al. // Intern. J. Hydrogen Energy. 2020. V. 45. № 35. P. 17270; https://doi.org/10.1016/j.ijhydene.2020.04.177
Костин С.В., Кришеник П.М., Рогачев С.А. // Хим. физика. 2021. Т. 40. № 1. С. 24; https://doi.org/10.31857/S0207401X21010076
Lutsenko N.A. // Combust. Theory Modell. 2018. V. 22. № 2. P. 359; https://doi.org/10.1080/13647830.2017.1406617
Podlesniy D., Zaichenko A., Tsvetkov M. et al. // Fuel. 2021. V. 298 P. 120862; https://doi.org/10.1016/j.fuel.2021.120862
Шпирт М.Я., Рашевский В.В. Микроэлементы горючих ископаемых. М.: Кучково поле, 2010.
Сирина Т.П., Красненко Т.И., Соловьев Г.В. и др. // Вестн. ЮУрГУ. Химия. 2013. Т. 5. № 1. С. 4.
Хаджиев С.Н., Шпирт М.Я. Микроэлементы в нефтях и продуктах их переработки. М.: Наука, 2012.
Шаповалов А.С., Полищук А.В., Черных Д.П. и др. Способ получения феррованадия: Пат. 2677197 РФ // Официальный Бюллетень Федеральной службы по интеллектуальной собственности “Изобретения. Полезные модели”. 2019. № 2.
Голубев А.А., Гудим Ю.А. Способ выплавки ферроникеля из окисленных никелевых руд и продуктов их обогащения и агрегат для его осуществления: Пат. 2336355 РФ // Б.И. 2008. № 29.
Кадиев Х.М., Висалиев М.Я., Зекель Л.А. и др. // ХТТ. 2018. № 6. С. 51; https://doi.org/10.1134/S0023117718060063
Висалиев М.Я. Комплексная переработка тяжелых нефтяных остатков с получением концентрата металлов Дис. … канд. хим. наук. М.: ИНХС РАН, 2014.
Chmielewski A.G., Urbanski T.S., Migdal W. // Hydrometallurgy. 1997. V. 45. № 3. P. 333; https://doi.org/10.1016/S0304-386X(96)00090-4
Висалиев М.Я., Шпирт М.Я., Кадиев Х.М. и др. // ХТТ. 2012. № 2. С. 32.
Tsuboi I., Kasai S., Kunugita E. et al. // J. Chem. Eng. Jpn. 1991. V. 24. P. 15; https://doi.org/10.1252/jcej.24.15
Цыганкова М.В., Букин В.И., Лысакова Е.И. и др. // Цв. металлы. 2011. № 1. С. 21.
Лукомская Г.А., Шакиров К.З., Петрова Л.И. и др. Способы извлечения ванадия из отходов сжигания сернистых мазутов: Пат. 2334800 РФ // Б.И. 2008. № 27.
Schemel R., Rodriguez D., Salazar R. Method for leaching and recovering vanadium from vanadium bearing by-product materials: Pat. US № 4539186. USA, 1985.
Михайлов Ю.Л. Физико-химические исследования процессов выщелачивания микрокомпонентов золы от сжигания углей Экибастузского бассейна Дис. … канд. хим. наук. Омск: ОмГУ, 2001.
Tereza A.M., Medvedev S.P., Smirnov V.N. // Acta Astronaut. 2020. V. 176. P. 653; https://doi.org/10.1016/j.actaastro.2020.03.045
Тереза А.М., Агафонов Г.Л., Бетев А.С. и др. // Хим. физика. 2020. Т. 39. № 12. С. 29; https://doi.org/10.31857/S0207401X20120158
Дополнительные материалы отсутствуют.
Инструменты
Химическая физика