Химическая физика, 2022, T. 41, № 11, стр. 79-87
Влияние герметизирующего слоя на физико-механические свойства оболочки сосуда высокого давления для хранения водорода
А. М. Куперман 1, А. Ю. Сергеев 1, *, Р. А. Турусов 1, В. И. Солодилов 1
1 Федеральный исследовательский центр химической физики им. Н.Н. Семёнова Российской академии наук
Москва, Россия
* E-mail: sergeevandrey89@gmail.com
Поступила в редакцию 16.05.2022
После доработки 14.06.2022
Принята к публикации 20.06.2022
- EDN: MXRTDQ
- DOI: 10.31857/S0207401X22110073
Аннотация
Исследован способ повышения герметичности емкостей для хранения водорода, изготовленных из полимерных композитных материалов, путем введения в структуру композита тонких металлических слоев. Показано, что наличие в стеклопластике промежуточного слоя отожженной алюминиевой фольги не изменяет модуль упругости и прочность материала при растяжении. Исследованы изгибные и сдвиговые характеристики, а также вязкость разрушения этого материала.
1. ВВЕДЕНИЕ
В настоящее время в рамках мероприятий по развитию водородной энергетики в Российской Федерации, направленных на увеличение производства и расширение сферы применения водорода в качестве экологически чистого топлива, актуализировались проблемы безопасного хранения и транспортировки водорода. Водород, в отличие от нефти и газа, относится к топливу, получаемому искусственно. При этом 1 кг водорода при комнатной температуре и атмосферном давлении занимает объем 11.2 м3, т.е. его объемная плотность при нормальных условиях равна ρ = = 0.089 кг/м3.
Особенно актуально применение водородного топлива в высокоэффективных энергетических установках, в которых используется принцип детонационного горения [1–4]. В настоящее время различают следующие способы его хранения: в сжатом газообразном виде, в сжиженном виде и с использованием твердых носителей [5–9]. Последний способ разделяют на физиосорбцию и хемосорбцию. Физиосорбция – процесс адсорбции водорода на поверхности материала. К материалам, для которых характерен процесс физиосорбции, относятся: металлоорганические каркасы (MOFs), цеолиты и углеродные материалы. Хемосорбция – процесс, в котором молекула диссоциирует между атомами водорода и диффундирует в структурную решетку материала. К твердым носителям, с помощью которых осуществляется хранение по способу хемосорбции, относятся металлические гидриды (MgH2) и комплексные гидриды (NaAlH4, LiAlH4, LiBH4, NaBH4 и т.д.). Комплексные гидриды, состоящие из легких элементов, таких как натрий (Na) и литий (Li), получили особое внимание в качестве твердотельного носителя для хранения водорода, поскольку обычный гидрид металла состоит в основном из тяжелых элементов.
К настоящему моменту наиболее эффективным промышленным способом хранения водорода является его хранение в баллонах в сжатом под давлением 70 МПа виде. Процесс сжатия позволяет достичь величины объемной плотности до 30 кг/м3. Данный способ широко используется в области наземного транспорта из-за технической простоты, эффективности и доступности.
На сегодняшний день выделяют пять основных типов конструкций емкостей для хранения газов, различающихся между собой себестоимостью изготовления и массой: цельнометаллические (тип I), металлокомпозитные (два подтипа: тип II и тип III), полимеркомпозитные (тип IV) и безлейнерные композитные баллоны (тип V).
В металлокомпозитных емкостях металлический лейнер (вкладыш) имеет меньшие предельные упругие деформации, чем композитная оболочка. Поэтому толщина усиливающей оболочки должна ограничивать уровень предельных деформаций металла лейнера. Кроме того, при использовании металлического лейнера внутри металлокомпозитного баллона, изготовленного методом намотки, возникает проблема наводораживания металла и, в частности, сварных швов. Таким образом, металлические баллоны и лейнеры для хранения водорода следует изготавливать из специальных, стойких к водороду сплавов. Это обусловлено тем, что водород, взаимодействуя с имеющимся в стали углеродом, превращает его в углеводороды, что приводит к резкому ухудшению свойств стали.
Полимеркомпозитные баллоны, содержащие лейнер из термопластичного материала, являются альтернативным техническим решением. Лейнеры такого типа изготавливаются методом раздувания заготовки в прессформе или ротационного формования с использованием специальных марок полиэтилена, полиамида и других термопластов. Полимеркомпозитные емкости, содержащие лейнер из термопласта, имеют довольно высокие предельные деформации и стойкость к циклическим нагружениям [10–13]. Однако массовая эффективность их меньше по сравнению с безлейнерными емкостями.
Безлейнерные емкости, состоящие полностью из композитных материалов, имеют наиболее высокую массовую эффективность [14]. Однако композитные материалы характеризуются меньшей герметичностью по сравнению, например, с однородными полимерами и металлами. К фундаментальной научной проблеме пониженной герметичности армированных полимеров относятся те определяющие качества и свойства рассматриваемых материалов, физико-химические процессы и явления, без которых невозможно само создание и существование класса армированных пластиков, а именно:
1) адгезионное взаимодействие полимерной матрицы и армирующих волокон, усадка материала матрицы при ее отверждении и различие в упругих свойствах и коэффициентах линейного расширения матрицы и армирующих волокон при охлаждении приводят с неизбежностью к формированию всесторонних растягивающих микронапряжений в ней. Эти микронапряжения создают сравнительно рыхлое состояние матрицы в армированном полимере, понижая тем самым герметичность последних;
2) анизотропия термоупругих параметров армированного полимера и двухсвязность формы намоточных изделий являются причинами возникновения радиальных растягивающих макронапряжений в композите. Макронапряжения вместе с микронапряжениями, приводящие в ряде случаев к образованиям макро- и микротрещин, являются фундаментальной причиной пониженной герметичности намоточных композитов. Иногда в процессе изготовления намоточного композита эти напряжения оказываются разрушающими.
Таким образом, повысить герметичность полимерных композитных материалов можно двумя способами: за счет создания благоприятного поля остаточных напряжений [15–17] либо внедрения герметизирующих слоев из металла или полимера [18–20]. В настоящей работе рассматривается вариант повышения герметичности оболочки баллона, основанный на том, чтобы поместить внутрь стенки из композита весьма тонкий (30 мкм) слой алюминия. Тонкий герметизирующий слой практически не воспринимает на себя нагрузку от внутреннего давления газа и будет работать совместно с силовой оболочкой.
2. МАТЕРИАЛЫ И МЕТОДЫ
2.1. Определение прочности алюминиевой фольги
Для создания герметизирующего слоя в армированных пластиках использована алюминиевая нагартованная холоднокатанная фольга марки АД1. Прочность, модуль упругости и предельное удлинение исходной и отожженной при 300 °С фольги определяли на образцах в виде полос шириной 20 мм, длиной рабочей зоны 100 мм и толщиной 30 мкм. Во время испытания фиксировали диаграмму нагружения напряжение (σ) – относительное удлинение (ε). Испытания проводили на машине Instron 3365 (Great Britain). Скорость перемещения зажимов составляла 10 мм/мин. Прочность определяли по максимальному напряжению, максимальное относительное удлинение соответствовало разрушению материала.
2.2. Определение герметичности образцов по гелию
Для определения проницаемости образцов использовали метод Дайнеса–Баррера, который основан на прямом количественном определении проникшего через полимерный листовой или намоточный материал газа за определенный период времени. Исследование проницаемости по газам проводили на установке, схема которой показана на рис. 1. Установка состоит из газового хроматографа 1, к которому подключена диффузионная ячейка 2, помещенная для повышения безопасности при проведении эксперимента при повышенном давлении в металлический защитный экран 3. Соединение диффузионной ячейки с хроматографом осуществлялось через четырехходовой кран 4. Кроме того, в состав установки входят баллон с гелием 6 и баллон с газом-носителем (азотом) 5.
Рис. 1.
Схема диффузионной установки: 1 – хроматограф, 2 – диффузионная ячейка, 3 – металлический защитный экран, 4 – четырехходовой кран, 5 – баллон с газом-носителем, 6 – баллон с гелием, 7 – осушительные патроны, 8 – образцовый манометр.
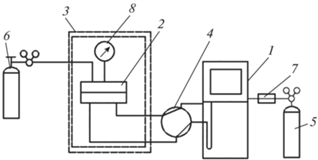
В качестве измерительного элемента использовался газовый хроматограф модели ЛХМ-72. Он позволяет оценить концентрацию газообразных примесей в газе-носителе, попадающих при проникновении через образец в диффузионную ячейку 2 (рис. 1), с помощью высокочувствительного детектора по теплопроводности – катарометра.
Осушительные патроны 7 (рис. 1) представляют собой цилиндрические емкости, последовательно заполненные несколькими слоями силикагеля, цеолита и активированного угля. Они служат для дополнительного осушения и очистки от возможных примесей газа-носителя.
Диффузионная ячейка (рис. 2) представляет собой конструкцию, состоящую из фланцев 1 и 2, образующих вместе с образцом дискообразной формы 4 две камеры: верхнюю, в которую подают через штуцер 7 гелий, давление которого контролируют манометром 8, и нижнюю – измерительную, соединяемую через штуцеры 6 с газовым хроматографом. Между камерами помещают образец исследуемого листового материала, деформация которого в результате создания избыточного давления гелия предотвращается индентором 3 с отверстиями. Уплотнение по периферии дискообразного образца выполнено в виде двойного шип-паза с шириной уплотняющей поверхности в 10 мм. Соединение камер осуществляется с помощью четырех радиально попарно расположенных болтов 9.
Рис. 2.
Схема диффузионной ячейки: 1 – верхний фланец ячейки, 2 – нижний фланец ячейки, 3 – диск с отверстиями, предохраняющий материал от механического разрушения при повышенном давлении (индентор), 4 – исследуемый образец, 5 – уплотнительный узел – двойной шип-паз, 6 – штуцеры для входа и выхода газа-носителя, 7 – штуцер для подключения баллона с гелием и создания избыточного давления, 8 – манометр, 9 – болты с гайками для герметизации ячейки.
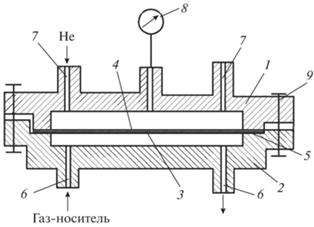
Диффузионную ячейку в сборе помещали в металлический защитный экран. Соединение диффузионной ячейки с хроматографом осуществляли через четырехходовой кран 4 (рис. 2). Кран имеет два положения. В первом положении измерительная камера диффузионной ячейки отключена от газового хроматографа, а во втором положении она подключена к газовой линии хроматографа и детектору. В последнем случае весь гелий, проникший через материал и находящийся в измерительной камере ячейки, потоком газа-носителя выдувается и транспортируется в детектор хроматографа. Уплотнение образцов в диффузионной ячейке осуществляли кольцевыми прокладками из фторопласта.
Образцы для испытаний имели форму дисков диаметром 80 мм, вырезанных из пластин стеклопластиков разной толщины. Для получения образцов пластин использовали однонаправленный препрег на основе стеклянного ровинга РВМПН-10-400-14 (НПО “Стеклопластик”, Россия). В качестве связующего применяли эпоксидиановую смолу ЭД-20 (Armplast, Россия), которую модифицировали 10 мас.% диглицидилового эфира диэтиленгликоля ДЭГ-1 (АО “ХИМЭКС Лимитед”, Россия) или 10 мас.% полисульфона ПСК-1 (АО “НИИПМ”, Россия). Отвердителем служил триэтаноламинотитанат ТЭАТ-1 (АО “ХИМЭКС Лимитед”, Россия). Пластины получали методом прямого прессования препрега. Для получения образцов с фольгой обезжиренный слой фольги укладывали на слой препрега, затем на слой фольги накладывался слой препрега и после сформированный образец отверждали в прессе при температуре 160 °С и давлении 16 МПа в течении 8 ч.
Всего получено три партии стеклопластиков разной толщины. Образцы первой партии стеклопластиковых материалов на основе эпоксидного связующего ЭД-20 + 10 мас.% ДЭГ-1 имели толщину от 0.6 до 4.1 мм; образцы второй партии на основе матрицы состава ЭД-20 + 10 мас.% ПСК-1 – от 0.8 до 5.0 мм; образцы третьей партии на основе эпоксидного связующего ЭД-20 + + 10 мас.% ДЭГ-1 с фольгой – от 0.8 до 3.0 мм.
Испытания по определению проницаемости материалов по гелию проводили при температуре (20 ± 3) °С в режиме изменения избыточного давления гелия в верхней камере диффузионной ячейки от 0.49 до 2.45 МПа. Определяли количество проникшего гелия и рассчитывали величину потока (I) проникшего газа в см3/см2 · с через материал при заданном давлении по формуле
где S, см2 – площадь рабочей поверхности образца материала; V, см3 – количество гелия, проникшего через материал за промежуток времени, равный Δt, с.Поток газа через пластину толщиной δ определяется с использованием уравнения Фика:
где Р = Dk – коэффициент проницаемости материала по газу, D – коэффициент диффузии материала, k – коэффициент растворимости газа в материале; p1 – p2 = Δp – перепад давлений на образце.Тогда из (2) имеем
2.3. Определение физико-механических свойств стеклопластиков с герметизирующим слоем алюминиевой фольги
Для того чтобы выявить преждевременное образование трещин, в частности, в пограничном слое между алюминиевой фольгой и стеклопластиком, была проведена серия испытаний образцов при различных видах нагружения. Так же, как и для плоских образцов, кольцевые образцы стеклопластиков получали на основе стеклянного ровинга РВМПН-10-400-14 и эпоксидной смолы ЭД-20, которую модифицировали 10 мас.% ДЭГ-1. Кольцевые образцы изготавливали методом намотки ровинга, пропитанного связующим, на цилиндрическую оправку диаметром 150 мм. Ширина образцов ограничивалась промежуточными кольцевыми вставками большего диаметра. Расстояние между промежуточными вставками составляло 10 мм (подробно технология намотки описана в работе [21]).
В процессе намотки в стеклопластик закладывали отожженную алюминиевую фольгу, которая служила герметизирующим слоем. При этом перед укладкой фольги в армирующую структуру ее предварительно обезжиривали в ацетоне.
Режим отверждения стеклопластиков аналогичен описанному выше. После отверждения и охлаждения в термошкафу оправки с кольцевыми образцами стеклопластиков разбирали. В результате получили кольца трех толщин: 1.3 мм (для испытаний на растяжение, изгиб и вязкость разрушения), 2.5 мм (для испытаний на изгиб), 4.5 мм (для испытаний на сдвиг).
Качество полученных образцов из стеклопластика оценивали по количеству армирующих волокон и пористости материала, которые определяли расчетным методом. Содержание армирующих волокон во всех образцах составило примерно 55 об.%, пористость – менее 3 об.%. Плотность образцов, измеренная гидростатическим взвешиванием, составляла около 2000 кг/м3.
Кольцевые образцы стеклопластиков толщиной 1.3 мм испытывали на растяжение с помощью 72-кулачкового приспособления и на полудисках [22, 23]. Это приспособление представляет собой устройство для равномерного нагружения кольцевого образца армированного пластика, которое достигается за счет синхронного перемещения кулачков, передающих нагрузку на внутреннюю поверхность образца при перемещении толкателя. Нагружение образцов осуществляли на испытательной машине типа Insron при скорости нагружения 10 мм/мин.
Прочность σр при растяжении кольцевых образцов, испытанных по обоим методам, определяли по формуле
(4)
${{\sigma }_{{\text{р}}}} = {{{{F}_{{\text{р}}}}} \mathord{\left/ {\vphantom {{{{F}_{{\text{р}}}}} {2А}}} \right. \kern-0em} {2А}},$Площадь образцов рассчитывали по формуле
где b – ширина образца, h – толщина образца.В случае испытаний армированных пластиков методом трехточечного изгиба изменение геометрических размеров образцов, т.е. изменение соотношения l/h, где l – длина образца приводит к изменению механизмов их разрушения. В зависимости от соотношения l/h образцы могут разрушаться от нормальных (изгиб) или от касательных (сдвиг) напряжений.
Кольцевые образцы стеклопластиков (с герметизирующем слоем из фольги и без него) толщиной 1.3 мм разрезали на сегменты, так чтобы соотношение l/h ≈ 30. Аналогично на сегменты разрезали кольцевые образцы толщиной 2.5 мм, в которых фольгу располагали в различных слоях: наружном, среднем и внутреннем. При этом фольга при испытании находилась соответственно в зоне сжатия, сдвига или растяжения. Соотношение l/h для таких образцов составляло около 20.
Перед разрезанием на сегменты часть кольцевых образцов подвергали предварительному многократному (до 10 раз) нагружению усилием, составляющим 50–70% от разрушающего в 72-кулачковом приспособлении. Это имитировало процесс заполнения–опустошения баллона газом.
Испытания проводили на машине Instron 3365. Скорость перемещения зажимов составляла 10 мм/мин.
Расчет прочности при изгибе проводили по формуле
где P – действующая сила, при которой происходит разрушение образца.Прочность при сдвиге определяли по методу короткой балки на сегментах, вырезанных из колец толщиной 4.5 мм. Соотношение l/h = 7. Так же как и для образцов стеклопластиков, испытываемых на трехточечный изгиб, часть кольцевых образцов подвергали предварительному многократному нагружению в 72-кулачковом приспособлении в тех же условиях. Скорость перемещения зажимов также составляла 10 мм/мин.
Расчет прочности при сдвиге проводили по формуле
Измерение удельной вязкости разрушения стеклопластиков, GIR, проводили путем раскалывания двухконсольной балки. Использовали сегменты колец толщиной 1.3 мм и длиной около 150 мм. Начальную трещину задавали с помощью лезвия в среднем слое образца без герметизирующего слоя и в слое, в котором находилась алюминиевая фольга. Так же, как и для остальных образцов, проведено 10 циклов нагружения и разгрузки.
Трещиностойкость армированных пластиков, GIR, определяли при помощи “метода углов” на образцах в виде духконсольной балки [24]. Схема нагружения образца и измеряемые параметры показаны на рис. 3. Скорость перемещения зажимов составляла 50 мм/мин. Число циклов нагружение–разгрузка при испытании каждого образца варьировали от 4 до 6. В ходе испытания регистрировали зависимости силы F от перемещения зажимов. По диаграммам нагружения для каждого цикла определяли силу F, необходимую для расчета энергии GIR. По фотографиям измеряли углы изгиба консолей образца.
Расчет удельной вязкости расслоения GIR проводили по формуле
(8)
${{G}_{{IR}}} = {{F\left( {\sin {{\alpha }_{1}} + \sin {{\alpha }_{2}}} \right)} \mathord{\left/ {\vphantom {{F\left( {\sin {{\alpha }_{1}} + \sin {{\alpha }_{2}}} \right)} b}} \right. \kern-0em} b},$Для каждого вида материалов испытывали по два образца.
3. РЕЗУЛЬТАТЫ И ИХ ОБСУЖДЕНИЕ
Как уже было отмечено, деформативность фольги – один из определяющих факторов для придания оболочке прочности и герметичности в условиях изменяющихся нагрузок. Интерес представляло сравнение предельных деформаций образцов из алюминиевой фольги в состоянии поставки и после термообработки.
На рис. 4 показаны диаграммы нагружения полосок исходной фольги (кривая 1) и фольги, прошедшей отжиг при 300 °С (кривая 2). Видно, что в результате такой термообработки существенно повышается уровень предельных деформаций: с 3 до 10%, при этом снижается прочность материала с 150 до 70 МПа. Дальнейшие исследования проводились только на отожженной фольге.
Результаты определения герметичности образцов стеклопластиков показаны в табл. 1. Испытание образца № 1 в первой партии (стеклопластик на основе эпоксидной смолы ЭД-20, модифицированной активным разбавителем ДЭГ-1) при избыточном давлении 0.49 МПа показало, что образец имел сквозные макродефекты (фазовый поток), и поэтому при других давлениях его далее не испытывали. Сквозные макродефекты регистрировали посредством погружения диффузионной ячейки в воду, отсоединения линии газа-носителя и наблюдения за истечением газа через штуцер 6 (рис. 2) в воду с образованием видимых пузырьков. Проницаемость стеклопластиков зависит от толщины образца. Так, для образца № 2 (толщина – 1.2 мм) усредненная проницаемости PHe составила 2.33 · 10–12 м2/с · Па, для образца № 3 (толщина – 2.1 мм) – 0.29 · 10–12 м2/с · Па, для образца № 4 (толщина – 4.1 мм) – 3.63 · 10–12 м2/с · Па. Изменение коэффициента проницаемости при разных давлениях и толщинах, вероятно, связано с влиянием напряженно-деформированного состояния на проницаемость стеклопластиков.
Таблица 1.
Проницаемость по гелию образцов прессованных стеклопластиков
№ партии | № образца | Средняя толщина δ, мм | Перепад давления гелия на образце Δр, МПа | Поток проникшего газа I · 107, см3/см2 ∙ с | Коэффициент проницаемости по гелию, PНе · 1012, м2/с · Па |
---|---|---|---|---|---|
1 | 1 | 0.6 | 0.49 | Фазовый поток | – |
2 | 1.2 | 0.49 | 10 | 2.40 | |
0.98 | 25 | 3.00 | |||
1.47 | 30 | 2.40 | |||
1.96 | 36 | 2.13 | |||
2.45 | 43 | 2.04 | |||
19.61* | 340 | 2.01 | |||
3 | 2.1 | 0.49 | 1.1 | 0.46 | |
0.98 | 1.3 | 0.27 | |||
1.47 | 1.8 | 0.25 | |||
1.96 | 2.6 | 0.27 | |||
2.45 | 2.9 | 0.24 | |||
19.61* | 24 | 0.25 | |||
4 | 4.1 | 0.49 | 4.3 | 3.47 | |
0.98 | 10 | 4.05 | |||
1.47 | 14 | 3.78 | |||
1.96 | 18 | 3.64 | |||
2.45 | 21 | 3.40 | |||
19.61* | 170 | 3.44 | |||
2 | 1 | 0.8 | 0.49 | 0.2 | 0.03 |
0.98 | 0.7 | 0.055 | |||
1.47 | 1.2 | 0.063 | |||
1.96 | 1.8 | 0.071 | |||
2.45 | 2.2 | 0.070 | |||
19.61* | 17 | 0.067 | |||
2 | 1.5 | 0.49 | 1.0 | 0.300 | |
0.98 | 1.8 | 0.270 | |||
1.47 | 2.5 | 0.250 | |||
1.96 | 3.5 | 0.260 | |||
2.45 | 4.5 | 0.266 | |||
19.61* | 36 | 0.266 | |||
3 | 3.0 | 0.49 | 0.05 | 0.030 | |
0.98 | 0.16 | 0.050 | |||
1.47 | 0.24 | 0.050 | |||
1.96 | 0.35 | 0.052 | |||
2.45 | 0.45 | 0.053 | |||
19.61* | 3.6 | 0.053 | |||
3 | 1 | 0.8 | 2.45 | – | – |
2 | 3 | 2.45 | – | – |
Еще более низкой проницаемостью обладают образцы второй партии (стеклопластик на основе эпоксидной смолы ЭД-20, модифицированной полисульфоном ПСК-1). Образцы № 1 и № 3 имели усредненный коэффициент проницаемости PHe = 0.059 · 10–12 и 0.048 · 10–12 м2/с · Па соответственно. Такую низкую проницаемость можно связать не только с напряженно-деформированным состоянием, но и с фазовой структурой эпокситермопластичных матриц [25, 26]. При концентрации ПСК-1 10 мас.% в ЭД-20 во время отверждения происходит фазовый распад изначально гомогенного связующего [25]. При этом образуются взаимопроникающие фазы, одна из которых обогащена ПСК-1. Таким образом, протяженная фаза полисульфона также будет способствовать снижению проницаемости материала.
При испытаниях образцов третьей партии (в армирующую структуру стеклопластиков введен слой фольги) не зарегистрирован поток газа, что свидетельствует о высокой степени герметичности исследуемых материалов.
На рис. 5 показаны типичные диаграммы растяжения однонаправленных кольцевых образцов стеклопластиков толщиной 1.3 мм, полученные при нагружении полудисками. Как видно из представленных графиков, зависимости для образцов с фольгой и без нее полностью идентичны. Стеклопластики деформируются упруго до момента разрушения.
Рис. 5.
Типичные диаграммы растяжения кольцевых образцов стеклопластиков с помощью полудисков: ◼ – контрольный образец, ⚫ – образец с фольгой.
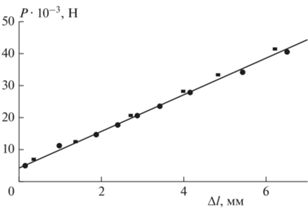
Как известно, в ряде случаев при определении прочности кольцевых образцов по формуле (4) получают заниженные значения по сравнению с альтернативными методами. Прочность образцов определяли путем умножения предельной деформации, измеренной с использованием тензоаппаратуры при нагружении полудисками, на модуль упругости. Кроме того, существует зависимость прочности и модуля упругости от толщины и диаметра образцов [27, 28]. Причина снижения измеренной прочности заключается в особенности напряженно-деформированного состояния образца, исследуемого по данному методу, в котором наряду с радиальными и окружными напряжениями возникают и касательные напряжения [29]. Величина касательных напряжений зависит от толщины и радиуса оболочки, а также анизотропии свойств композита. При этом в оболочке, равномерно нагруженной внутреннем давлением газа или жидкости, касательные напряжения отсутствуют. Таким образом, партию кольцевых образцов испытывали независимо акустическим методом [30] для определения окружного модуля упругости. Модуль упругости колец составил 52 ГПа. Прочность образцов, как с фольгой, так и контрольных, составила 1.8 ГПа.
Аналогичные результаты по определению прочности кольцевых образцов были получены также при испытании кольцевых образцов на растяжение с помощью 72-кулачкового приспособления, обеспечивающего, в отличие от метода испытаний полудисками, равномерное поле распределения напряжений. Разрушающие нагрузки оказались одинаковыми для контрольных образцов и образцов со слоем фольги и показали прочность, составившую 1.8 ГПа.
Значения прочности при изгибе стеклопластиков, полученные для образцов толщиной 1.3 мм (l/h ≈ 30), представлены в табл. 2. Видно, что прочность при изгибе контрольных образцов на 20% выше прочности стеклопластиков с фольгой в среднем слое независимо от того, исходные ли это образцы или подвергавшиеся 10-кратному нагружению.
Таблица 2.
Значения прочности при изгибе σизг сегментов колец стеклопластиков толщиной 1.3 мм (l/h ≈ 30)
Наименование образцов | σизг, ГПа | |
---|---|---|
исходные | после 10-кратного нагружения | |
Образцы с фольгой | 1.20 | 1.24 |
Контрольные | 1.50 | 1.60 |
Аналогичным испытаниям при изгибе (табл. 3) были подвергнуты кольцевые образцы толщиной 2.5 мм (l/h ≈ 20), в которых фольгу располагали в разных слоях: наружном, среднем и внутреннем. При этом фольга при испытании находилась соответственно в зоне сжатия, сдвига или растяжения. Следует отметить, что прочность контрольных образцов в этом случае оказалась примерно на 30% ниже по сравнению с предыдущим. Это можно объяснить уменьшением соотношения l/h (с 30 до 20) и соответствующим увеличением влияния напряжений сдвига. Наличие фольги в различных слоях образца также приводит к снижению прочности примерно на 10%. Особенно это проявляется для образцов с фольгой в среднем слое, в котором предполагаются максимальные напряжения сдвига. Однако 10-кратное предварительное нагружение образцов до нагрузки в 60% от разрушающей привело к увеличению прочности на сдвиг по сравнению с исходной более чем на 20%.
Таблица 3.
Значения прочности при изгибе σизг сегментов колец стеклопластиков толщиной 2.5 мм (l/h ≈ 20)
Тип образца | σизг, ГПа | |
---|---|---|
исходные | после 10-кратного нагружения | |
Фольга во внутреннем слое (растяжение) | 1.09 | 1.09 |
Фольга в среднем слое (сдвиг) | 0.88 | 1.05 |
Фольга в наружном слое (сжатие) | 1.10 | 1.14 |
Контрольные (без фольги) | 1.18 | 1.16 |
В табл. 4 приведены значения прочности при сдвиге, которые определялись методом короткобалочного сдвига на сегментах, вырезанных из колец толщиной 4.5 мм (l/h = 7). Прочность контрольных образцов (не содержащих слоя фольги) примерно на 20% выше, чем для стеклопластика с герметизирующим слоем. Такая разница в прочности при сдвиге может быть связана как с разной адгезионной прочностью для склеек эпоксидная матрица – алюминиевая фольга и эпоксидная матрица – стеклянные волокна, так и с полем напряжений, возникшим в герметизирующем слое. Предварительное циклическое нагружение образцов стеклопластиков не повлияло на их прочность.
Таблица 4.
Значения прочности при сдвиге τсдв сегментов колец стеклопластиков толщиной 4.5 мм
Тип образца | τсдв, МПа | |
---|---|---|
исходные | после 10-кратного нагружения | |
Образцы с фольгой | 51 | 51 |
Контрольные | 62 | 62 |
Значения вязкости разрушения стеклопластиков представлены в табл. 5. Результаты измерений оказались неожиданными. С одной стороны, введение фольги в средний слой образца приводит к снижению GIR на 20–40%, с другой – после 10-кратного предварительного нагружения этот показатель возвращается к первоначальному значению.
Как отмечено выше, практически при любом виде нагружения наблюдается рост прочности и трещиностойкости стеклопластиков, содержащих в качестве герметизирующего слоя алюминиевую фольгу, после циклического нагружения. Известно, что при многократной деформации металлов происходит накопление дислокаций (микродефектов в кристаллической решетке) на их поверхности. Возможно, что растущие микротрещины, образующиеся вблизи герметизирующего слоя, могут взаимодействовать с дислокациями на поверхности фольги и изменять свой путь. В результате увеличения длины пути трещины необходимо больше энергии для ее распространения. Учитывая высокую адгезионную прочность в системе алюминиевая подложка – эпоксидный полимер, можно предположить, что возникновение и движение дислокаций оказывают непосредственное влияние на распространение микротрещин в районе герметизирующего слоя. Этот вопрос требует дополнительного исследования.
4. ЗАКЛЮЧЕНИЕ
Основываясь на результатах проведенных исследований, можно отметить, что наличие в стеклопластике промежуточного слоя отожженной фольги не влияет на прочность материала при растяжении. Прочность при изгибе и прочность при сдвиге, а также вязкость разрушения снижаются на 10–20% при введении в армирующую структуру материала герметизирующего слоя. Возможно, это удастся преодолеть с помощью специальной обработки поверхности фольги. Предварительное нагружение стеклопластиков, имитирующее нагрузку–разгрузку баллонов, не ухудшает свойства композитов, как контрольных образцов, так и со слоем фольги.
Работа выполнена по госзаданию ФИЦ ХФ РАН (регистрационный номер 122040400099-5).
Список литературы
Атанов Г.А, Ежов В.М., Куликов С.В., Папанов О.А., Червонная Н.А. // Хим. физика. 2021. Т. 40. № 3. С. 31.
Ежов В.М., Куликов С.В., Мягков Ю.П. и др. // Хим. физика. 2021. Т. 40. № 6. С. 66.
Смыгалина А.Е., Киверин А.Д. // Хим. физика. 2021. Т. 40. № 8. С. 49.
Бетев А.С., Киверин А.Д., Медведев С.П., Яковенко И.С. // Хим. физика. 2020. Т. 39. № 12. С. 17.
Фатеев В.Н., Алексеева О.К., Коробцев С.В. и др. // Chem. Problems. 2018. Т. 16. № 4. С. 453.
Алексеева О.К., Козлов С.И., Самсонов Р.О., Фатеев В.Н. // Альтернативное топливо. 2009. Т. 4. № 10. С. 10.
Abe J.O., Popoola A.P.I., Ajenifuja E., Popoola O.M. // Intern. J. Hydrogen Energy. 2019. № 44. P. 15072.
Ouyang L., Chen K., Jiang J., Yang X., Zhu M. // J. Alloys Comp. 2020. № 829. P.154597.
Gangu K.K., Maddila S., Mukkamala S.B., Jonnalagadda S.B. // J. Energy Chem. 2018. P. 1.
Demichev V.I., Sergeev A.Y., Motova T.A. et al. // Mech Compos Mater. 2022. № 57. P. 785; https://doi.org/10.1007/s11029-022-09999-w
Zhang Q., Hu Hui, Jia X. et al. // Compos. Struct. 2020. № 236. P. 111915.
Liao B.B., Wang D.L., Hamdi M., Zheng J.Y. // Intern. J. Hydrogen Energy. 2019. № 44. P. 22494.
Dao D.Q., Luche J., Bustanante-Valencia L. // Fire Technol. 2014. V. 52. № 2. P. 397; https://doi.org/10.1007/s10694-014-0423-4
Type V pressure vessels liner-less all composite tanks. Composite Technology Development, Inc.; https:// www.ctd-materials.com/engineered-materials/kiboko/
Елаков А.Б., Турусов Р.А., Богачев Е.А., Сергеев А.Ю. // Науч.-техн. ведомости СПбПУ. Естественные и инженерные науки. 2018. Т. 24. № 2. С. 149;
Sergeev A., Turusov R., Gorenberg A., Kuperman A. // MATEC Web Conf. 2018. V. 251. P. 04053;https://doi.org/10.1051/matecconf/201825104053IPICSE-2018
Sergeyev A.Y., Turusov R.A., Baurova N.I. et al. // Mech. Compos. Mater. 2015. № 51. P. 321; https://doi.org/10.1007/s11029-015-9503-x
Wei R., Wang X., Chen C., Zhang X. et al. // Mater. design. 2017. № 116. P. 188.
Ogasawara T., Arai N., Fukumoto R., Ogawa T. et al. // Adv. Compos. Mater. 2014. V. 23. № 2. P. 129; https://doi.org/10.1080/09243046.2013.844756
Ляхно В.Ю., Гарбуз А.С., Гнездилова Л.В. и др. // ПТЭ. 2009. № 5. С. 150.
Solodilov V.I., Gorbatkina Yu.A. // Mech. Compos. Mater. 2006. V. 42. № 6. P. 513; https://doi.org/10.1007/s11029-006-0062-z
D2290 – 16 Standard Test Method for Apparent Hoop Tensile Strength of Plastic or Reinforced Plastic Pipe.
ГОСТ 25.603-82 Метод испытания на растяжение кольцевых образцов при нормальной, повышенной и пониженной температурах. М.: Стандартиформ, 2005.
Solodilov V.I., Bashenov S.L., Gorbatkina Yu.A., Kuperman A.M. // Mech. Compos. Mater. 2003. V. 39. № 5. P. 401; https://doi.org/10.1023/B:MOCM.0000003291.33589.df
Shapagin A.V., Budylin N.Yu., Chalykh A.E. et al. // Polymers. 2021. V. 13. № 1. P. 1; https://doi.org/10.3390/polym13010035
Tretyakov I.V., Vyatkina M.A., Cherevinskiy A.P. et al. // Bull. Russ. Acad. Sci. Phys. 2021. № 85. P. 876; https://doi.org/10.3103/S1062873821080293
Turusov R.A., Kuperman A.M., Andreev V.I. // Adv. Mater. Res. 2018. V. 1102. P. 155; https://doi.org/10.4028/www.scientific.net/AMR.1102.155
Турусов Р.А., Куперман А.М. // Механика композиц. матер. и конструкций. 1998. Т. 4. № 3. С. 62.
Partsevskii V.V. // Polym. Mech. 1970. № 6. P. 973; https://doi.org/10.1007/BF00856917
Sergeev A.Y., Baurova N.I. // Polym. Sci. Ser. D. 2017. № 10. P. 62; https://doi.org/10.1134/S1995421217010191
Дополнительные материалы отсутствуют.
Инструменты
Химическая физика