Химическая физика, 2020, T. 39, № 8, стр. 51-57
Влияние оксида натрия на плавкость золы твердых коммунальных отходов
М. В. Цветков 1, *, Д. Н. Подлесный 1, В. М. Фрейман 1, 2, Е. А. Салганский 1, Ю. Ю. Цветкова 1, И. В. Зюкин 1, 2, А. Ю. Зайченко 1, М. В. Салганская 1, 2
1 Институт проблем химической физики Российской академии наук
Черноголовка, Россия
2 Московский государственный университет им. М.В. Ломоносова
Москва, Россия
* E-mail: tsvetkov@icp.ac.ru
Поступила в редакцию 09.01.2020
После доработки 09.01.2020
Принята к публикации 20.02.2020
Аннотация
Охарактеризован модельный состав твердых коммунальных отходов и химический состав его золы. Минеральные соединения и температуры плавления исследованы с использованием различных аналитических методов, включая методы XRD, FTIR и AFT. Рассчитаны основные показатели шлакообразования: основно-кислотное соотношение, индекс вязкости шлака, коэффициент обрастания. Зола твердых коммунальных отходов содержит значительные количества CaO, SiO2 и Al2O3. С использованием программы Terra проведены термодинамические расчеты химических равновесий систем CaO–SiO2–Al2O3–Na2O, содержащих от 5 до 25% оксида натрия. Экспериментально показано, что увеличение содержания Na2O на каждые 5% снижает характерные температуры плавления, золы твердых коммунальных отходов на 30–50 °С.
ВВЕДЕНИЕ
В России ежегодно образуется более 60 млн т твердых коммунальных отходов (ТКО), из которых только 7–8% поступает на переработку [1]. Большая часть отходов отправляется на свалки, которые занимают огромные территории земли, и при самовоспламенении ТКО окружающая среда загрязняется отходящими газами. Кроме того, мусорные свалки являются источником загрязнения как поверхностных, так и подземных вод вследствие дренажа свалок атмосферными осадками.
В настоящее время одним из перспективных методов термической переработки ТКО является газификация в режиме фильтрационного горения [2–6]. Такая технология в противоточных системах имеет ряд преимуществ: высокая чистота отходящих газов, высокая эффективность процесса, возможность использования низкокалорийных и мелкодисперсных отходов [7–10]. При газификации ТКО образуется продукт-газ (смесь CO, H2, CO2 и др.), который после очистки можно использовать для получения тепловой или электрической энергии [11–15].
Технология газификации в режиме фильтрационного горения предполагает твердое золоудаление, поэтому плавление золы налагает ограничения на максимальную рабочую температуру. Этапы плавления золы ТКО, согласно ГОСТу 54238, можно описать с помощью четырех характерных температур – метод AFT (рис. 1).
Рис. 1.
Этапы плавления золы: 1 – исходный образец; 2–5 – вид образца при температуре деформации (2), температуре сферы (3), температуре полусферы (4) и температуре растекания (5).
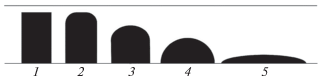
При росте температуры в реакторе выше температуры деформации (DT) золы наблюдается спекание шихты, что препятствует разгрузке зольного остатка. Для предотвращения шлакования золы важно до начала сжигания ТКО знать химический состав и характерные температуры плавления золы, чтобы не превышать DT, и/или применять другие методы предотвращения шлакования золы [16].
Характеристики плавления золы тесно связаны с ее составом, который в основном состоит из восьми оксидов: SiO2, Al2O3, Fe2O3, CaO, MgO, Na2O, K2О и TiO2. Как правило, эти оксиды разделены на две группы: кислотные оксиды, которые повышают температуру плавления, и щелочные оксиды, которые ее понижают. Влияние оксидов SiO2, Al2O3, Fe2O3, CaO на температуру плавления и минеральный состав золы угля уже достаточно хорошо изучено [17–20]. Однако влияние щелочных оксидов, особенно оксида натрия, изучено меньше, хотя изменение их концентраций оказывают значительное влияние на плавкость золы [21–23].
Изучая поведение натриевых полевых шпатов при их нагревании до 1600 °С, австралийские ученые обнаружили, что выше 1050 °С начинается плавление зольного остатка [24]. Это хорошо согласуется с бинарной фазовой диаграммой системы альбит–кремнезем, которая указывает на температуру эвтектики, равную 1062 °C. В работе [25] исследовали температуры плавления золы различных бытовых отходов (шин, древесины, смеси полимеров с бумагой и др.), однако практически не рассматривали влияние оксида натрия на плавкость золы. Температуру плавления золы можно изменять путем смешивания различных топлив, например угля с илом сточных вод [26]. В обзоре [27] рассматриваются проблемы шлакуемости золы при сжигании биомассы и некоторые способы ее предотвращения. Обсуждены мультикомпонентные фазовые диаграммы систем K2O(+Na2O)–CaO(+MgO)–SiO2 для предсказания характеристик плавления золы биомассы [28].
Приведенные выше исследования проводились в основном для углей и биомассы и были направлены на изучение роли добавок различных оксидов. В зависимости от морфологического состава твердых коммунальных отходов содержание соединений натрия в них может быть различным.
Цель настоящей работы – изучение влияния оксида натрия на температуры плавления золы ТКО и преобразование минеральных соединений в условиях термической переработки.
ЭКСПЕРИМЕНТАЛЬНАЯ ЧАСТЬ
Характеристика используемого ТКО. Модельный состав ТКО: бумага и картон – 40 мас.%, пищевые отходы – 22 мас.%, пластмасса – 10 мас.%, стекло – 7 мас.%, алюминиевые банки – 5 мас.%, железная проволока – 3 мас.%, древесина – 7 мас.%, текстиль – 3 мас.%, кожа и резина – 3 мас.%. Для повышения доли натрия в исследуемой золе к модельному составу золы ТКО добавляли карбонат натрия. Выбор Na2CO3 в качестве добавки обусловлен его инертностью при комнатной температуре (температура плавления карбоната натрия равна 852 °С).
Приготовление и анализ золы
Образцы золы ТКО готовили в соответствии с ГОСТом Р 55661-2013. Образцы помещали в муфельную печь, нагревали их до 500 °С в течение 30 мин, выдерживали 30 мин, затем поднимали температуру до 815 °С в течение 30 мин и выдерживали еще 2 ч. Далее золу охлаждали до комнатной температуры и хранили в герметичной таре для последующего анализа. Полученную золу анализировали на сканирующем автоэмиссионном электронном микроскопе Zeiss LEO SUPRA 25, а также на атомно-абсорбционном спектрофотометре AAS-3 (на натрий и калий) с целью определения ее химического состава.
Химический состав золы ТКО в пересчете на оксиды следующий: SiO2 – 24.21 мас.%, Al2O3 – 12.09 мас.%, Fe2O3 – 3.01 мас.%, CaO – 42.41 мас.%, MgO – 2.32 мас.%, Na2O – 3.25 мас.%, K2O – 1.5 мас.%, P2O5 – 2.53 мас.%, CO2 – 4.59 мас.%, остальное (TiO2, SO3, Cl– и др.) – 4.09 мас.%. Золу ТКО и ее смеси с 15% и 25% карбоната натрия (в пересчете на Na2O) нагревали до заданных температур (1000 °С, 1100 °С, 1200 °С) и охлаждали до комнатной температуры. После измельчения золы до фракции с размером частиц 60–100 мкм определяли кристаллические фазы на рентгеновском порошковом дифрактометре ДРОН-УМ2, укомплектованном рентгеновской трубкой с Cu(Kα)-излучением с размером шага 0.05° в диапазоне 2θ = 10–80°. Для идентификации фаз использовали электронную базу данных PDF-4 + ICDD.
Для определения пространственных групп атомов золу анализировали на ИК-фурье-спектрометре Bruker VERTEX 70. Исследовали спектральную область от 50 до 2000 см–1. В спектрах представлены пики поглощения, которые соответствуют частотам колебаний связей.
Методика определения температур плавления золы ТКО
Определение температур плавления золы ТКО и ее смеси с карбонатом натрия в количестве 10%, 15%, 20% и 25% (в пересчете на Na2O) проводили по ГОСТу Р 54238-2010. Использовали высокотемпературную муфельную печь SNOL с возможностью нагрева до 1650 °С, в которую помещали цилиндрические образцы золы ТКО высотой 10 мм и диаметром 6 мм. Скорость нагрева образцов до температуры 900 °С составляла 20 °С/мин. Затем скорость нагрева уменьшали до 5 °С/мин, поднимая температуру до заданного значения. Время выдержки образцов при заданной температуре в окислительной атмосфере составляло 30 мин. После их охлаждения до комнатной температуры проводили визуальный осмотр на предмет изменения формы образцов.
Термодинамические расчеты
Термодинамический пакет программы Terra основан на минимизации общей энергии Гиббса исследуемой системы. Он может использоваться для прогнозирования многофазных равновесий, соотношений жидкой и твердой фаз, а также фазовых переходов при различных температурах для гетерогенных систем [29].
Рассчитывали систему, состоящую из оксидов, входящих в состав зольного остатка модельного ТКО (см. выше). Дополнительно рассчитаны системы с содержанием оксида натрия в смеси 15 и 25 мас.%. Концентрации остальных оксидов уменьшали пропорционально их содержанию в золе ТКО. Расчеты проводили в диапазоне температур 600–1500 °С с интервалом 20 °С в окислительной атмосфере при давлении 0.1 МПа.
РЕЗУЛЬТАТЫ И ИХ ОБСУЖДЕНИЕ
Исследование температур плавления, фактора шлакования, индекса вязкости золы и коэффициента обрастания золы ТКО
Экспериментально измеренное значение DT золы составило 1170 °С, значение температуры образования сферы – 1220 °С, значение температуры образования полусферы (HT) – 1250 °С. При температуре 1280 °С наблюдали полное плавление образца и растекание его на фарфоровой подложке.
Температуру образования полусферы для исследуемого образца золы ТКО можно рассчитать по эмпирической формуле [30], в которую подставляются содержания оксидов (мас.%): HT = = 426.77P2–736.76P + 1592.3, где P = ([CaO] + + [MgO] + [Na2O] + [K2O])/([SiO2] + [Al2O3] + + [Fe2O3]), с коэффициентом корреляции, равным 0.91. Для рассматриваемого модельного состава ТКО рассчитанное значение температуры полусферы равно 1341 °С, что выше полученных нашими экспериментальных данных. Рассчитана температура деформации по эмпирической формуле [31]: DT = 92.55[SiO2] + 97.83[Al2O3] + 84.52[Fe2O3] + + 83.67[CaO] + 81.04[MgO] + 91.92a – 7891, где a = = 100 – ([SiO2] + [Al2O3] + [Fe2O3]+ [CaO] + [MgO]). Для рассматриваемого модельного состава ТКО DT = 990 °С, что ниже экспериментальных данных. Такое расхождение показывает, что приведенные формулы не подходят для определения температуры плавления золы ТКО и говорит о сложности правильного предсказания значений температур плавления золы.
Отношение суммарного содержания основных компонентов (CaO, MgO, Na2O, K2O, Fe2O3) к сумме содержаний кислотных компонентов (SiO2, Al2O3) золы определяет величину основно-кислотного соотношения (RS) [32]. Это соотношение широко применяется при моделировании шлакования золы и рассчитывается по эмпирической формуле, в которую подставляются значения мас.% содержаний оксидов (в мас.%):
Основно-кислотное соотношение оксидов для золы ТКО, рассчитанное по вышеприведенной формуле, равно 1.32, что позволяет отнести золу ТКО к материалам со средней степенью шлакуемости (RS = 0.6–2.0).
Другой важной характеристикой золы является индекс вязкости шлака, SR, который зависит от содержания SiO2 и Fe2O3 и рассчитывается по следующей формуле [32]: SR = 100[SiO2]/([SiO2] + [Fe2O3] + + [CaO] + [MgO]). Для золы ТКО SR = 33.65, что соответствует высокому уровню шлакования (SR < < 65). Эвтектика с низкой температурой плавления (SiO2 + Fe2O3) может оказывать сильное влияние на агломерацию частиц золы. В процессе спекания железо реагирует с кварцем и алюмосиликатами с образованием силикатов железа и силикатов железа и алюминия, которые могут плавиться при более низких температурах.
Коэффициент обрастания определяется по формуле Fu = RS(Na2O + K2O) [32]. Для золы ТКО это значение равно 6.27, что позволяет отнести ее к материалам с высокой степенью обрастания (Fu = = 0.6–40).
Влияние оксида натрия на температуры плавления золы
На рис. 2 показаны зависимости температуры плавления золы модельного состава ТКО от содержания оксида натрия. Характерные температуры плавления золы ТКО снижаются в среднем на 40 °С при увеличении содержания Na2O на каждые 5 мас.%.
Термодинамические расчеты с использованием программы TERRA
Согласно расчетам, для модельной золы ТКО основным соединением, образующимся во всем рассматриваемом температурном диапазоне является пиросиликат кальция (Ca3Si2O7), содержание которого составляет ~59%. Остальных соединений в золе образуется значительно меньше: содержание каждого из них составляет <11%. При увеличении температуры выше 640 °С снижается количество Na2CO3 и Al2O3, а алюминат натрия (NaAlO2) становится более устойчивым. При температуре ~850 °С происходит сплавление оставшегося карбоната натрия с оксидом железа с образованием феррита натрия. При температуре выше 900 °C карбонат кальция разлагается до оксида кальция и углекислого газа. Выше ~1250 °C часть натрия из алюмината натрия постепенно переходит в феррит натрия.
Рис. 3.
Расчетные зависимости массовой доли ω основных стабильных конденсированных фаз от температуры в золе ТКО: 1 – Ca3Si2O7, 2 – MgAl2O4, 3 –CaCO3, 4 – Ca3(PO4)2, 5 – NaAlO2, 6 – Fe2O3, 7 – CaO, 8 – NaFeO2, 9 – Na2CO3, 10 – Al2O3.
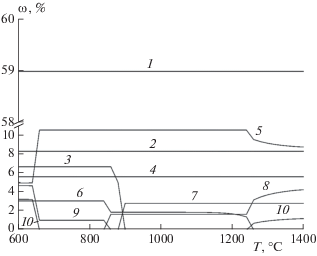
При повышении концентрации оксида натрия в системе до 15% основным соединением, образующимся во всем рассматриваемом температурном интервале, остается Ca3Si2O7. При температуре от 600 до 1300 °C никаких изменений (химических реакций) не происходит, концентрации всех соединений остаются постоянными и составляют: Ca3Si2O7 – ~45%, NaAlO2 – ~17%, Na2CO3 – ~8%, а остальных (Na2SiO3, CaO, Ca3(PO4)2, NaFeO2, MgO) – менее 7%.
При температурах выше 1300 °C карбонат натрия сплавляется с пиросиликатом кальция с образованием силиката натрия и оксида кальция, выделяя CO2. В результате концентрации Na2SiO3 и CaO возрастают до ~16% и ~14%, соответственно, концентрация Ca3Si2O7 падает до ~32%, а карбонат натрия исчезает полностью.
Когда содержание оксида натрия достигает 25%, основным соединением в системе становится Na2SiO3. Происходит дальнейшее вытеснение оксидом натрия оксида кальция из силиката кальция. В целом, тенденции аналогичны случаю с 15%-ным содержанием Na2O, только с различием в концентрациях участвующих веществ. В реальных системах концентрации образующихся веществ могут отличаться от концентраций, рассчитанных в условиях термодинамического равновесия, из-за неоднородности состава отдельных частиц золы и относительно медленно протекающих химических реакций.
Результаты термодинамических расчетов с помощью программы Terra могут быть использованы для моделирования минеральных превращений золы ТКО при высоких температурах.
Рентгенофазовый анализ золы ТКО с различным содержанием оксида натрия
На рис. 4–6 представлены рентгенограммы золы ТКО с различным содержанием оксида натрия при различных температурах. Основными кристаллическими фазами в модельном составе золы ТКО при 1000 °С и 1100 °С являются алюмосиликат кальция состава Ca2Al2SiO7 (геленит), кварц, оксиды железа и алюминия. Ниже приведена реакция образования геленита при высоких температурах:
Рис. 4.
Рентгенограмма модельной золы ТКО при температурах 1000, 1100 и 1200 °С: 1 – Ca2Al2SiO7 (геленит), 2 – Fe3O4, 3 – Fe2O3 (гематит), 4 – Al2O3 (корунд), 5 – SiO2 (кварц).
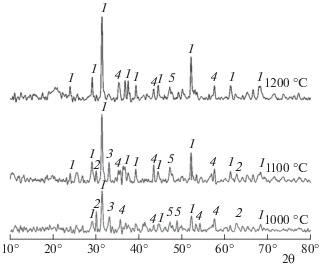
Рис. 5.
Рентгенограмма золы ТКО с Na2CO3 (15% Na2O) при температурах 1000, 1100 и 1200 °С: 1 – NaAlSi2O6 (жадеит), 2 – Ca2Al2SiO7 (геленит).
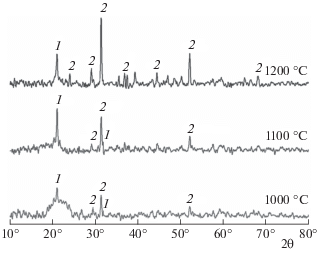
Рис. 6.
Рентгенограмма золы ТКО с Na2CO3 (25% Na2O) при температурах 1000, 1100 и 1200 °С: 1 – (NaFeO2)1 –x · (SiO2)x.
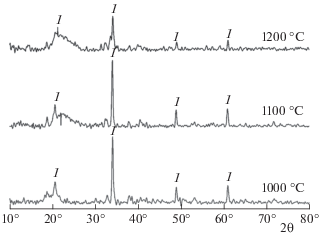
При 1200 °С в золе ТКО оксиды железа не обнаружены, вероятно, из-за реакций с оксидом фосфора и перехода полученных соединений (например, фосфата железа) в аморфную фазу. Отсутствие кристаллических фаз щелочных металлов на рентгенограмме (после нагрева золы до 1000 °С) косвенно свидетельствует об их переходе в аморфную фазу при более низких температурах.
С добавлением карбоната натрия (15% Na2O в золе) на рентгенограмме во всем исследуемом температурном диапазоне обнаруживаются пики, принадлежащие кристаллической фазе алюмосиликата натрия состава NaAlSi2O6 (жадеит). Приведем реакцию образования жадеита при высоких температурах:
Присутствие NaAlSi2O6 говорит о взаимодействии кварца с оксидами алюминия и карбонатом натрия. Геленит также присутствует в исследуемой смеси в интервале температур 1000–1200 °С, как и в модельном составе золы. Других соединений в кристаллической форме найдено не было.
При содержании оксида натрия в смеси, равном 25%, на рентгенограммах обнаруживается только пик, принадлежащий твердому раствору состава (NaFeO2)1 – x(SiO2)x, где 0 < x ≤ 0.327 [33], реакция образования которого приведена ниже:
Образование натрийсодержащих соединений снижает температуры плавления золы. Рентгенофазовый анализ подтверждает существование кристаллических фаз оксидов железа и алюминия, феррита натрия (с оксидом кремния), что было предсказано с помощью термодинамических расчетов.
ИК-фурье-спектроскопия золы ТКО
На рис. 7 представлены ИК-спектры золы ТКО с различным содержанием оксида натрия после прокаливания до 1100 °С. Наиболее интенсивные изменения полос поглощения наблюдаются в диапазоне волновых чисел 400–1200 см–1.
Рис. 7.
ИК-спектры Фурье золы ТКО с различным содержанием оксида натрия при 1100 °С: 1 – зола ТКО, 2 – зола ТКО с Na2CO3 (15% Na2O), 3 – зола ТКО с Na2CO3 (25% Na2O).
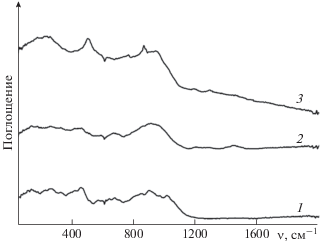
На ИК-спектрах образцов золы прослеживаются полосы поглощения с максимумами при 470, 640, 860, 1014 см–1. Пики при 470 и 640 см–1 обусловлены деформационными колебаниями связей Si–О–Si(Al), а полоса поглощения при 860 см–1 появляется из-за валентных колебаний Si–O–Si или Si–O–Al, что свидетельствует о присутствии алюмосиликатов натрия или кальция (Ca2Al2SiO7 и NaAlSi2O6) в золе. Полоса поглощения при 1014 см–1 относится к валентным колебаниям связей Si–О в сложных силикатных анионах [34]. С повышением содержания Na2O полоса поглощения при 1014 см–1 пропадает, а интенсивность полосы около 860 см–1 растет, что говорит о снижении доли силикатов в золе.
ВЫВОДЫ
Содержание оксида натрия оказывает значительное влияние на шлакуемость золы ТКО. Характерные температуры плавления золы ТКО снижаются на 30–50 °С при увеличении содержания Na2O на каждые 5%.
Основные критерии шлакуемости золы ТКО (фактор шлакования RS = 1.32, индекс вязкости шлака SR = 33.65, коэффициент обрастания Fu = = 6.27) показывают, что она склонна к шлакообразованию, а при добавлении оксида натрия количество шлака будет возрастать.
Согласно термодинамическим расчетам основным соединением золы ТКО является пиросиликат кальция, доля которого составляет ~59%. При температурах выше 640 °С образуется алюминат натрия (NaAlO2), затем при 850 °С – феррит натрия (NaFeO2). Выше 1250 °C часть натрия из алюмината натрия постепенно переходит в феррит натрия. Добавление карбоната натрия к золе ТКО приводит к увеличению концентраций силиката, алюмината и феррита натрия в системе, а при температуре выше 1300 °C – к сплавлению Na2CO3 с Ca3Si2O7, что ведет к дальнейшему росту концентрации силиката натрия.
Рентгенофазовый анализ показал, что в золе ТКО основными кристаллическими фазами являются Ca2Al2SiO7 (геленит), оксиды железа и алюминия (корунд). При повышении концентрации оксида натрия до 15% появляется фаза NaAlSi2O6 (жадеит). При 25%-ном содержании Na2O образуется в основном твердый раствор состава (NaFeO2)1 –x(SiO2)x. ИК-спектроскопия Фурье свидетельствует об образовании силикатов и алюмосиликатов натрия или кальция (Ca2Al2SiO7 и NaAlSi2O6) в золе.
Определение элементного состава, рентгенофазовый анализ, ИК-спектроскопия Фурье золы ТКО и ее смесей с Na2CO3 выполнены сотр. АЦКП ИПХФ РАН Н.Н. Дрёмовой, Р.Ю. Рубцовым, П.С. Барбашовой. Расшифровка рентгенограмм выполнена в лаборатории структурной химии Д.В. Корчагиным.
Исследование выполнено при финансовой поддержке Российским фондом фундаментальных исследований в рамках научного проекта № 19-08-00244, программы фундаментальных исследований Президиума РАН № 15 и госзадания № АААА-А19-119022690098-3.
Список литературы
Namsaraev Z.B., Gotovtsev P.M., Komova A.V., Vasilov R.G. // Renew. Sust. Energy Rev. 2018. V. 81. P. 625; https://doi.org/10.1016/j.rser.2017.08.045
Манелис Г.Б., Глазов С.В., Салганский Е.А., Лемперт Д.Б. // Успехи химии. 2012. Т. 81. № 9. С. 855.
Toledo M., Ripoll N., Céspedes J. et al. // Energy Convers. Manag. 2018. V. 172. P. 381; https://doi.org/10.1016/j.enconman.2018.07.046
Зайченко А.Ю., Жирнов А.А., Манелис Г.Б., Полианчик Е.В., Жолудев А.Ф. // Докл. АН. 2008. Т. 418. № 5. С. 635.
Глазов С.В., Кислов В.М., Салганский Е.А. // Журн. прикл. химии. 2018. Т. 91. № 10. С. 1396; https://doi.org/10.1134/S0044461818100031
Кислов В.М., Салганский Е.А., Цветков М.В., Цветкова Ю.Ю. // Журн. прикл. химии. 2017. Т. 90. № 5. С. 579.
Dmitrienko M.A., Nyashina G.S., Strizhak P.A. // J. Clean. Prod. 2018. V. 177. P. 284; https://doi.org/10.1016/j.jclepro.2017.12.254
Кислов В.М., Глазов С.В., Салганский Е.А., Колесникова Ю.Ю., Салганская М.В. // Физика горения и взрыва. 2016. Т. 52. № 3. С. 72; https://doi.org/10.15372/FGV20160310
Колесникова Ю.Ю., Кислов В.М., Салганский Е.А. // Хим. физика. 2016. Т. 35. № 9. С. 53; https://doi.org/10.7868/S0207401X16090041
Салганский Е.А., Кислов В.М., Глазов С.В., Колесникова Ю.Ю., Жолудев А.Ф. // Химия в интересах устойчивого развития. 2016. Т. 24. № 3. С. 303; https://doi.org/10.15372/KhUR20160304
Салганская М.В., Глазов С.В., Салганский Е.А. и др. // Хим. физика. 2008. Т. 27. № 1. С. 20.
Toledo M., Rosales C., Silvestre C., Caro S. // Intern. J. Hydrog. Energy. 2016. V. 41. № 46. P. 21131; https://doi.org/10.1016/j.ijhydene.2016.09.120
Salgansky E.A., Kislov V.M., Glazov S.V., Salganskaya M.V. // J. Combust. 2016. Article ID 9637082; https://doi.org/10.1155/2016/9637082
Кислов В.М., Жолудев А.Ф., Кислов М.Б., Салганский Е.А. // Журн. прикл. химии. 2019. Т. 92. № 1. С. 61; https://doi.org/10.1134/S0044461819010080
Зайченко А.Ю., Подлесный Д.Н., Цветков М.В., Салганская М.В., Чуб А.В. // Журн. прикл. химии. Т. 92. № 2. С. 245; https://doi.org/10.1134/S0044461819020166
Цветков М.В., Зюкин И.В., Фрейман В.М., Салганская М.В., Цветкова Ю.Ю. // Журн. прикл. химии. 2017. Т. 90. № 10. С. 1392.
Song W.J., Tang L.H., Zhu X.D. et al. // Energy Fuels. 2009. V. 24. № 1. P. 182; https://doi.org/10.1021/ef900537m
Liu B., He Q., Jiang Z., Xu R., Hu B. // Fuel. 2013. V. 105. P. 293; https://doi.org/10.1016/j.fuel.2012.06.046
Van Dyk J.C., Waanders F.B. // Ibid. 2007. V. 86. № 17–18. P. 2728; https://doi.org/10.1016/j.fuel.2007.03.022
Lv Y., Niu Y., Kan H., Wang D., Li P. // Ibid. 2019. V. 258. Article 116137; https://doi.org/10.1016/j.fuel.2019.116137
Melissari B. // Memoria Investigaciones en Ingeniería. 2014. V. 12. P. 31.
Wang Y., Xiang Y., Wang D. et al. // Energy Fuels. 2016. V. 30. № 2. P. 1437; https://doi.org/10.1021/acs.energyfuels.5b02722
Li G., Wang C.A., Yan Y. et al. // J. Energy Inst. 2016. V. 89. № 1. P. 48; https://doi.org/10.1016/j.joei.2015.01.011
Reifenstein A.P., Kahraman H., Coin C.D.A. et al. // Fuel. 1999. V. 78. № 12. P. 1449; https://doi.org/10.1016/S0016-2361(99)00065-4
Dunnu G., Maier J., Scheffknecht G. // Ibid. 2010. V. 89. № 7. P. 1534; https://doi.org/10.1016/j.fuel.2009.09.008
Li M., Li F., Liu Q., Fang Y., Xiao H. // Ibid. 2019. V. 244. P. 91; https://doi.org/10.1016/j.fuel.2019.01.161
Niu Y., Tan H., Hui S. // Prog. Energy Combust. Sci. 2016. V. 52. P. 1; https://doi.org/10.1016/j.pecs.2015.09.003
Bostrom D., Skoglund N., Grimm A. et al. // Energy Fuels. 2011. V. 26. № 1. P. 85; https://doi.org/10.1021/ef201205b
Трусов Б.Г. // Матер. XIV Междунар. конф. по химической термодинамике. Спб.: НИИХ СПбГУ, 2002. С. 483.
Kim M.R., Jang J.G., Lee S.K., Hwang B.Y., Lee J.K. // Korean J. Chem. Eng. 2010. V. 27. № 3. P. 1028; https://doi.org/10.1007/s11814-010-0156-0
Yin C., Luo Z., Ni M., Cen K. // Fuel. 1998. V. 77. № 15. P. 1777; https://doi.org/10.1016/S0016-2361(98)00077-5
Magdziarz A., Wilk M., Gajek M. et al. // Energy. 2016. V. 113. P. 85; https://doi.org/10.1016/j.energy.2016.07.029
Rulmont A., Tarte P., Winand J. M., Almou M. // J. Solid State Chem. 1992. V. 97. № 1. P. 156; https://doi.org/10.1016/0022-4596(92)90020-V
Saikia B.J., Parthasarathy G. // J. Modern Phys. 2010. V. 1. № 4. P. 206; https://doi.org/10.4236/jmp.2010.14031
Дополнительные материалы отсутствуют.
Инструменты
Химическая физика