Химическая физика, 2019, T. 38, № 1, стр. 55-61
Экологические характеристики инфракрасных горелочных устройств с каталитическим радиационным экраномН. Я. Василик, А. В. Порсин, В. М. Шмелёв
Н. Я. Василик 1, *, А. В. Порсин 2, В. М. Шмелёв 1
1 Институт химической физики им. Н.Н. Семёнова Российской академии наук
Москва, Россия
2 Институт катализа им. Г.К. Борескова Сибирского отделения Российской академии наук
Новосибирск, Россия
* E-mail: vasnja@mail.ru
Поступила в редакцию 21.05.2018
После доработки 20.07.2018
Принята к публикации 21.05.2018
Аннотация
Показана возможность существенного снижения концентрации монооксида углерода в продуктах сгорания смесей природного газа с воздухом в инфракрасных горелочных устройствах при установке над матрицей радиационного сетчатого экрана с каталитическим покрытием Pd–Ce/Al2O3. При использовании проницаемых матриц с радиационными сетчатыми экранами с каталитическим покрытием и без покрытий концентрация оксидов азота в продуктах сгорания не превышала 20 ppm в интервале значений удельной мощности горения от 20 до 100 Вт/см2. Использование экрана с каталитическим покрытием позволило получить в диапазоне значений удельной мощности горения от 30 до 60 Вт/см2 рекордно низкие концентрации CO в продуктах сгорания – на уровне 3–5 ppm. Разработанное каталитическое покрытие сохраняет работоспособность при многократных циклах нагрева сетчатого экрана с покрытием до температур 1400 К.
ВВЕДЕНИЕ
Инфракрасные горелочные устройства с проницаемыми матрицами находят широкое применение в быту и в промышленности [1, 2]. Современные конструкции матриц из металлической пены с керамическим покрытием и рекуперативными элементами позволяют обеспечить высокие значения удельной мощности горения вплоть до 120 Вт/см2 [3, 4], сохраняя устойчивый поверхностный режим горения. ИК горелочные устройства, работающие в режиме поверхностного горения, имеют концентрации вредных примесей в продуктах сгорания ниже, чем горелки открытого пламени (факельные, микрофакельные). При сжигании смесей природного газа с воздухом в режиме поверхностного горения концентрация оксидов азота не превышает, как правило, 10–40 ppm, концентрация монооксида углерода составляет порядка 40–100 ppm. С уменьшением удельной мощности горения концентрация NOx уменьшается, однако, эксперименты показывают, что концентрация CO при низкой интенсивности горения может возрастать до значений, существенно превышающих 100 ppm.
Наряду с инфракрасными (ИК) горелочными устройствами появляются горелочные устройства каталитического принципа действия, обладающие высокими экологическими характеристиками [5–7]. Концентрации оксидов азота и монооксида углерода в продуктах реакции в этих устройствах не превышают 1–10 ppm. Каталитическое горение реализуется при более низких температурах матрицы, чем в обычных горелочных устройствах. Как следствие, в каталитических горелках практически не образуются оксиды азота [8]. Существенным недостатком каталитического горения является низкая удельная интенсивность выделения энергии, которая, в сравнении с высокотемпературным горением на поверхности матриц, меньше в десятки раз. Это затрудняет создание компактных устройств большой мощности. Увеличению удельной мощности выделения энергии в каталитических горелках препятствует и другой недостаток – катализатор подвержен спеканию при высоких температурах [9, 10]. В работе [11] отмечалось, что катализатор, содержащий палладий, нанесенный на оксид алюминия, является одним из перспективных катализаторов при сжигании метана. Возможность объединения достоинств горения на поверхности матрицы ИК-горелки и в каталитической горелке в одном горелочном устройстве исследуется в данной работе.
ЭКСПЕРИМЕНТАЛЬНАЯ МЕТОДИКА
Эксперименты проводились с использованием двух типов матриц из металлической пены – обычной матрицы в виде пластины 80 × 80 мм толщиной 8 мм и составной рекуперационной матрицы, собранной из брусков металлической пены и пластин из жаропрочной стали. Длина брусков 80 мм, размер поперечного сечения бруска 8 × 8 мм. Длина пластин из жаропрочной стали 80 мм, ширина 16 мм, толщина 0.7 мм. Пластина из металлической пены и бруски матриц изготавливались из хромаля. Химический состав хромаля: Cr – 18%, Al – 6.5%, Co – 1.5%, Fe – основа. Средний диаметр ячеек в плоскости пластин (1.15 ± 0.21) мм; диаметр ячеек перпендикулярно к плоскости пластин (1.37 ± 0.07) мм. Объемная пористость матриц ~0.9, поверхностная проницаемость – 0.4. Поверхностная проницаемость определяется технологией изготовления матриц, а ее значение получено из анализа микрофотографии поверхности пластины. Боковая поверхность матриц “бронировалась” высокотемпературной замазкой. Схема макета горелочного устройства, схема рекуперационной матрицы, фотография поверхностного горения на рекуперационной матрице приведены на рис. 1. Макет включал в себя собственно горелочное устройство с цилиндрическим корпусом диаметром 80 мм с закрепляемой съемной квадратной матрицей, регулирующей и измерительную аппаратуру. Матрица закреплялась горизонтально. Для обеспечения однородности газового потока внутри корпуса горелочного устройства устанавливался перфорированный диск – распределитель потока газовой смеси. Над матрицей на расстоянии 8 мм от ее поверхности закреплялся радиационный экран в виде металлической сетки размером 80 × 80 мм с каталитическим покрытием (рис. 2а) или без покрытия (рис. 2б). Размер ячеек сеток 1.0 мм, диаметр проволоки 0.4 мм, живое сечение 0.4. Сетки без покрытия и с каталитическим покрытием были изготовлены из фехраля производства ЗАО “НПО Союзнихром”. Основные компоненты фехраля: хром – 22.1%, алюминий – 5.1%, сумма кремния, марганца, титана, никеля, углерода, фосфора и серы (в порядке убывания) – 1.0%, остальное – Fe. На сетку наносился Pd–Ce/Al2O3 катализатор, который был приготовлен следующим образом. Сначала на сетку наносили покрытие из η–Al2O3 согласно работе [12], далее – покрытие СеО2. Для нанесения СеО2 использовали пропитки по влагоемкости, причем в качестве предшественника CeO2 использовали раствор Ce(NO3)3. После пропитки образец сушили на воздухе при 110 °C в течение 1 ч и прокаливали при 600 °C в течение 1 ч. Затем наносили Pd из раствора PdCl2 также методом пропитки по влагоемкости. После пропитки следовала сушка на воздухе при 110 °C в течение 1 ч и прокаливании при 600 °C в течение 1 ч. В результате был получен Pd–Ce/Al2O3 катализатор, нанесенный на металлическую сетку, содержащий 5 мас. % Pd и 10% CeO2 от массы Al2O3. Содержание Al2O3 составляет 6% от массы сетки, толщина каталитического покрытия – около 50 мкм. Рекуперационная матрица обеспечивала устойчивое поверхностное горение при значениях удельной мощности горения от 20 до 120 Вт/см2. Максимальная температура рабочей поверхности обычной матрицы менее 1000 К [3, 4], для рекуперационной матрицы с теплопроводящими элементами до 1300 К [13]. В экспериментах с разными матрицами сравнивались: характеристики горелочных устройств с обычными матрицами без радиационного экрана-сетки; характеристики горелочных устройств с рекуперационными матрицами с расположенными сверху пластин мелкоячеистыми сетками с каталитическим покрытием или без покрытия (рис. 2). В ряде экспериментов вместо мелкоячеистых сеток на верхние края стальных пластин накладывали крупноячеистые сетки без покрытия из нержавеющей стали: сетка с ромбовидными ячейками, размеры диагоналей ромба 2.2 × 3.6 мм, живое сечение – 0.4 (рис. 3а) и сетка с квадратными ячейками из проволоки диаметром 1.2, размер стороны квадрата – 4 мм, живое сечение 0.6, рис. 3б. Во всех опытах использовалась смесь природного газа из городской магистрали и воздуха, образующаяся в смесителе, которая и поступала в горелочное устройство. Соотношение компонентов могло варьироваться в широком диапазоне при изменении коэффициента избытка воздуха α от 0.4 до 2.5. Расход газа измерялся и регулировался измерителем-регулятором расхода/давления фирмы Bronkhorst High-Tech (Нидерланды). Воздух нагнетался поршневым компрессором. Расход воздуха измерялся и регулировался измерителем-регулятором расхода/давления, модель F23AV фирмы Bronkhorst High-Tech. Для измерения эффективной температуры рабочей поверхности использовался радиационный пирометр (SMART SENSOR AR882) с рабочей полосой 8–14 мкм. Температура обратной стороны матрицы измерялась с помощью алюмель-хромелевой термопары толщиной 0.3 мм. Запись сигнала от термопары с использованием преобразователя Е–270 осуществлялась на компьютере. С помощью газового анализатора OPTIMA 7 фирмы MRU, Германия, измерялись концентрации оксидов азота, монооксида углерода, углекислого газа и кислорода в продуктах сгорания. Зонд газового анализатора диаметром 4 мм размещался над поверхностью матрицы или экрана в центральной части на расстоянии 10 мм от поверхности матрицы.
Рис. 1.
a – Схема макета горелочного устройства, б – схема рекуперационной матрицы, в – фотография поверхностного горения на рекуперационной матрице; 1 – корпус горелочного устройства, 2 – смеситель, 3 – распределитель потока газовой смеси, 4 – проницаемая матрица 5 – радиационный экран-сетка, 6 – расходомер газа, 7 – расходомер воздуха, 8 – термопара, 9 – преобразователь, 10 – газоанализатор, 11 – ИК-пирометр.
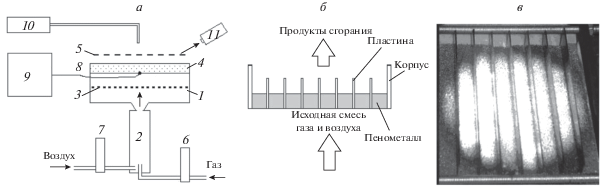
РЕЗУЛЬТАТЫ ЭКСПЕРИМЕНТОВ И ИХ ОБСУЖДЕНИЕ
В работах [3, 4, 13] показано, что температура поверхности используемых обычных проницаемых матриц в условиях поверхностного горения при коэффициенте избытка воздуха в газовой смеси 1.1 не превышает 1000 К в диапазоне изменения удельной мощности горения от 20 до 60 Вт/см2. В данных опытах коэффициент избытка воздуха не изменялся и его значение выбиралось равным 1.1. Размещение над поверхностью матрицы мелкоячеистой сетки-экрана с живым сечением ~0.4 приводило к увеличению температуры поверхности матрицы примерно на 100–150 К и расширяло пределы устойчивого поверхностного горения вплоть до величины удельной мощности горения 100 Вт/см2. Введение в конструкцию матрицы теплопроводящих элементов позволило обеспечить дополнительную рекуперацию тепла от продуктов сгорания к матрице. Рекуперация тепла происходит за счет конвективного и радиационного теплообмена. Теплопроводящие элементы, выступающие над поверхностью матрицы, играют роль радиационного экрана. Эффективность такого экрана по сравнению с обычным сетчатым экраном выше. Температура поверхности матрицы при использовании рекуператоров возрастает более чем на 200 К. В матрицах с комбинированным экраном в виде рекуперативных элементов и сетки температура поверхности горения достигает 1300 К (рис. 4), при этом максимальное значение плотности потока излучения от ее поверхности увеличивается в 1.7 раза. Устойчивый режим поверхностного горения на рекуперационной матрице был реализован в более широком диапазоне значений удельной мощности горения по сравнению с вариантом обычной проницаемой матрицы, а именно в диапазоне от 15 до 120 Вт/см2. Несмотря на дополнительный поток тепла в тело матрицы, температура обратной стороны матрицы остается достаточно низкой. При удельной мощности горения 20 Вт/см2 она составляет 500 К, уменьшаясь до 400 К с увеличением скорости потока входящей в горелочное устройство газовой смеси (рис. 4). Каталитическое покрытие на сетке не изменяло температуру поверхности горения и обратной стороны проницаемой матрицы и не оказывало существенного влияния на концентрацию оксидов азота в продуктах сгорания (рис. 5). Температуры сеток превышали значения температур поверхности горения на 50–100 К.
Рис. 4.
Зависимость температуры поверхности горения рекуперативной матрицы с мелкоячеистыми сетками от удельной мощности горения (1); зависимость температуры обратной поверхности рекуперативной матрицы от удельной мощности горения (2).
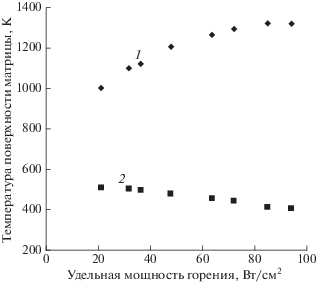
Рис. 5.
Зависимости концентраций оксидов азота в продуктах сгорания от удельной мощности горения: 1 – обычная матрица, 2 – рекуперативная матрица без сетки-экрана, 3 – рекуперативная матрица с мелкоячеистой сеткой, 4 – рекуперативная матрица с крупноячеистой сеткой с ромбовидными ячейками, 5 – рекуперативная матрица с крупноячеистой сеткой с прямоугольными ячейками, 6 – рекуперативная матрица c мелкоячеистой сеткой с каталитическим покрытием.
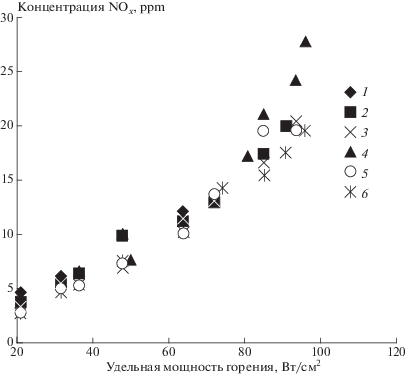
Интересно то, что концентрация оксидов азота в продуктах сгорания не изменяется существенным образом при введении в конструкцию ИК-горелки рекуперативных элементов в виде пластин и сеток, так как такое изменение конструкции ИК-горелки сопровождается, как уже отмечалось выше, значительным увеличением потока излучения. Увеличение потока излучения приводит к заметному падению температуры продуктов сгорания, что, казалось бы, должно сказаться заметным образом на концентрации оксидов азота. Однако поток излучения от обычной ИК-горелки с проницаемой матрицей из пенометалла без радиационного экрана уже существенно снижает температуру продуктов сгорания смеси природного газа и воздуха до значений примерно 1600–1700 К [14]. Концентрация оксидов азота, образующихся за счет окисления азота кислородом, при таких значениях температуры мала и поэтому более сильное охлаждение за счет излучения при введении рекуперативных элементов не оказывает существенного влияния на содержание оксидов азота в продуктах сгорания. Зависимости концентраций оксидов азота в продуктах сгорания смеси природного газа и воздуха от удельной мощности горения для ИК-горелок различных конструкций приведены на рис. 5. Размещение на теплопроводящих пластинах рекуперационной матрицы сеток разного типа приводит к небольшому снижению концентрации NOx (рис. 5).
Увеличение концентрации оксидов азота с увеличением удельной мощности горения объясняется тем, что при увеличении значений удельной мощности горения имеет место увеличение температуры продуктов сгорания, а радиационный КПД ИК-горелки уменьшается [15]. Покрытие мелкоячеистой сетки катализатором приводит к уменьшению концентрации оксидов азота, однако, этот эффект сравнительно небольшой и проявляется только при значениях удельной мощности горения более 80 Вт/см2.
Применение радиационного экрана в виде сетки или выступающих над поверхностью матрицы теплопроводных элементов приводит к существенному уменьшению концентрации монооксида углерода в продуктах сгорания (рис. 6). Комбинация из рекуперативных пластин с крупноячеистыми сетками более эффективна для уменьшения концентрации монооксида углерода, чем комбинация из пластин с мелкоячеистыми сетками Покрытие сетки катализатором еще более усиливает этот эффект. Значения концентрации CO для матрицы с каталитической мелкоячеистой сеткой не превышали 20 ppm в широком диапазоне изменения удельной мощности горения от 20 до 100 Вт/см2. Использование сетки-экрана с каталитическим покрытием позволило получить в диапазоне значений удельной мощности горения от 30 до 60 Вт/см2 рекордно низкие концентрации CO в продуктах сгорания – на уровне 3–5 ppm. Разработанное каталитическое покрытие эффективно работает не только в области температур сетки ниже 1000 К, но и при температурах более 1300 К, сохраняет работоспособность при многократных циклах нагрева сетки с покрытием до температур 1400 К.
Рис. 6.
Зависимости концентраций угарного газа в продуктах сгорания смеси природного газа с воздухом от удельной мощности горения: 1 – обычная матрица, 2 – рекуперативная матрица без сетки-экрана, 3 – рекуперативная матрица с мелкоячеистой сеткой, 4 – рекуперативная матрица с крупноячеистой сеткой с ромбовидными ячейками, 5 – рекуперативная матрица с крупноячеистой сеткой с прямоугольными ячейками, 6 – рекуперативная матрица c мелкоячеистой сеткой с каталитическим покрытием.
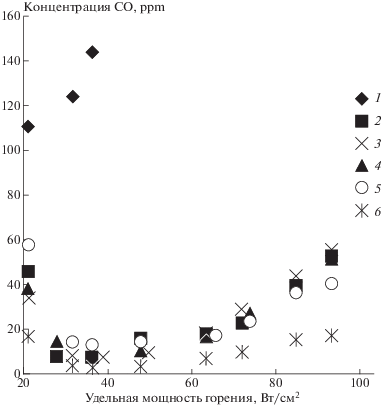
ЗАКЛЮЧЕНИЕ
Для всех исследованных конструкций ИК-горелок концентрация оксидов азота не превышала 20 ppm в интервале значений удельной мощности горения от 20 до 100 Вт/см2. Показана возможность существенного снижения монооксида углерода в продуктах сгорания при поверхностном горении смеси природного газа с воздухом в условиях, когда над матрицей установлен радиационный сетчатый экран с каталитическим покрытием. Наблюдалось заметное снижение концентрации монооксида углерода при использовании как обычных, так и высокотемпературных рекуперационных матриц. В диапазоне значений удельной мощности горения от 30 до 60 Вт/см2 на рекуперационных матрицах достигнуты рекордно низкие концентрации CO на уровне 3–5 ppm. В интервале значений удельной мощности горения от 20 до 100 Вт/см2 концентрация монооксида углерода не превышала 20 ppm.
Таким образом, каталитическое покрытие сетки-экрана оказывается очень эффективным способом уменьшения содержания монооксида углерода в продуктах сгорания инфракрасного горелочного устройства, особенно в случае необходимости регулирования мощности горения в широком диапазоне значений.
Работа выполнена за счет субсидии, выделенной ИХФ РАН на выполнение государственного задания по теме 44.8 “Фундаментальные исследования процессов превращения энергоемких материалов и разработка научных основ управления этими процессам” в 2017 г. (номер госрегистрации 0082-2016-0011).
Список литературы
Токарев П.С. Газовые горелки инфракрасного излучения и их применение в промышленности. Омск: Филиал ГОУ ВПО “РосЗИТЛП” г. Омска, 2009.
Malicoa I., Mujeebu M.A. // J. Adv. Thermofluid Res. 2015. V. l. № 1. P. 50.
Shmelev V. // Combust. Sci. Technol. 2014. V. 186. P. 943. doi: 10.1080/00102202.2014.890601
Василик Н.Я., Шмелев В.М. // Хим. физика. 2016. Т. 35 № 9. С. 35.
Боресков Г.К., Левицкий Э.А., Исмагилов З.Р. // ЖВХО. 1984. Т. 29. № 4. С. 19.
Porsin A.V., Kulikov A.V., Dalyuk I.K. et al. // J. Chem. Eng. J. 2015. V. 282. P. 233.
Куликов А.В., Загоруйко А.Н., Лопатин С.А. и др. // Научн. вестн. НГТУ. 2015. Т. 58. № 1. С. 257.
Ismagilov Z.R., Kerzhentsev M.A. // Catal. Rev. Sci. Eng. 1990. 32. № 1–2. P. 51.
Bartholomew C.H. // Appl. Catal., A: General. 2001. № 212. P. 17.
Euzen P., Gal J.-H.L., Rebours B. et al. // Catal. Today. 1999. № 47. P. 19.
Machida M., Taniguchi H., Kijimaa T. et al. // J. Mater. Chem. 1998. V. 8. № 3. P. 781.
Porsin A.V., Kulikov A.V., Rogozhnikov V.N. et al. // Catal. Today. 2016. № 273. P. 213.
Василик Н.Я., В.М. Шмелев В.М. // Горение и взрыв. 2017. Т. 10. № 2. С. 4.
Шмелев В.М. // ЖХФ. 2010. Т. 29. № 7. С. 1.
Василик Н.Я., Шмелев В.М. // Горение и взрыв / Под ред. Фролова С.М. М.: Торус Пресс, 2015. Вып. 8. № 1. С. 63.
Дополнительные материалы отсутствуют.
Инструменты
Химическая физика