Коллоидный журнал, 2023, T. 85, № 1, стр. 63-70
О важности подбора режима гидрофобизации для получения стойких супергидрофобных покрытий
Е. А. Кузина 1, *, Ф. Ш. Омран 1, А. М. Емельяненко 1, Л. Б. Бойнович 1
1 Институт физической химии и электрохимии им. А.Н. Фрумкина РАН
119071 Москва,
Ленинский просп., 31, корп. 4, Россия
* E-mail: kuzina.katya26.01@gmail.com
Поступила в редакцию 11.11.2022
После доработки 25.11.2022
Принята к публикации 29.11.2022
- EDN: KEVWVV
- DOI: 10.31857/S0023291222600614
Аннотация
Описан способ получения супергидрофобных покрытий на поверхности вольфрама и сплава алюминия Д16 с использованием наносекундной лазерной обработки с последующим химическим осаждением фтороксисилана из паровой фазы. На примере алюминия и вольфрама показано, что для получения химически стойких покрытий необходим подбор режима подготовки образцов для нанесения гидрофобизатора индивидуально для каждого материала. Варьирование временем предварительной обработки поверхности в кислородной плазме позволяет контролируемо изменять плотность поверхностных адсорбционных центров и управлять химической стойкостью слоя гидрофобного агента, а, значит, и покрытия в целом. На исследованных металлах получены супергидрофобные покрытия с углами смачивания более 170°, сохраняющимися при длительном непрерывном контакте с водными средами.
ВВЕДЕНИЕ
Супергидрофобные покрытия обычно используются как пассивные защитные покрытия. Они защищают поверхность от обледенения [1–3] и от обрастания [4–7], придают металлическим материалам стойкость к коррозии [8, 9], снижают водопоглощение древесины [10]. При разработке супергидрофобных материалов, которые будут длительное время находиться под влиянием различных разрушающих факторов, актуальной задачей является обеспечение высокой стойкости супергидрофобного состояния. Часто сразу после изготовления супергидрофобные покрытия демонстрируют высокие эксплуатационные характеристики, но под влиянием различных нагрузок свойства материала ухудшаются. Для быстрой деградации супергидрофобного материала при контакте с водными средами может быть несколько причин, связанных с особенностями приготовления поверхностей. Это, в первую очередь, неоднородное распределение молекул гидрофобного агента по глубине текстурированного поверхностного слоя. Неправильно подобранный метод нанесения гидрофобизатора может вызвать неоднородное покрытие поверхности текстуры гидрофобными молекулами, при котором часть внутренних поверхностей микро- и нанопор остаются непокрытыми гидрофобным агентом. Кроме того, слабая связь молекул гидрофобного агента и элементов текстуры, например, за счет физической адсорбции или слабой водородной связи, приводит к десорбции молекул гидрофобизатора при длительном контакте с водой [11]. Как правило, времена измерения углов смачивания составляют несколько минут, что значительно меньше времени жизни метастабильного супергидрофобного состояния, поэтому на этапе измерения начальных углов натекания и оттекания не удается обнаружить дефекты нанесения гидрофобного слоя на текстурированную поверхность. Однако при продолжительном погружении образца с супергидрофобным покрытием в водную среду дефекты полученного покрытия выявляются при анализе поведения углов смачивания и поверхностного натяжения капли тестовой жидкости [12, 13].
До настоящего времени было проведено множество исследований по оценке и увеличению стойкости супергидрофобных покрытий, но, в основном, внимание уделялось именно механической стойкости текстуры на поверхности [14–16] так как часто микро- и нанотекстура на поверхности бывает недостаточно прочной. Однако при эксплуатации супергидрофобных покрытий не менее важна химическая стойкость гидрофобизатора. Ранее нами использовались стандартизованные режимы подготовки поверхности с применением УФ/О3 [17] или плазменной обработки для пришивки к поверхности адсорбционно-активных центров перед нанесением гидрофобизатора [9, 18]. При этом детальный выбор оптимального времени обогащения поверхности гидрофобизуемого материала адсорбционно-активными центрами не проводился. В данной работе на примере подложек из алюминия и вольфрама мы покажем, что индивидуальный подбор времени плазменной обработки, зависящий от свойств обрабатываемого материала, важен для получения химически стойкого супергидрофобного состояния на различных материалах.
МАТЕРИАЛЫ И МЕТОДЫ
Для изучения влияния времени обработки в плазме на химическую стойкость супергидрофобных покрытий использовали пластины из вольфрама толщиной 0.5 мм марки ВА и пластины из алюминиевого сплава Д16 толщиной 3 мм. Перед лазерной обработкой пластины мыли под проточной водой от пыли и грязи, сушили и обезжиривали изопропиловым спиртом. Для создания текстуры на поверхности образцов их обрабатывали импульсным лазерным излучением. Применялся инфракрасный иттербиевый волоконный лазер с длиной волны 1.064 мкм, длительностью импульсов 200 нс, частотой импульсов от 20 до 30 кГц (в зависимости от материала), и пиковой мощностью до 0.95 мДж в моде TEM00. Плотность линий составляла 12.5 мм–1, скорость линейного перемещения луча 100 мм/с, флюенс 0.18 Дж/м2. Луч лазера фокусировался на поверхности обрабатываемого образца и, с помощью управляемой с компьютера двухосевой отклоняющей системы MS10 (Raylase, Германия), перемещался по поверхности образца. В зоне воздействия лазерного луча происходит нагрев до высокой температуры, плавление, возгонка и взрывная абляция материала. В этих процессах частицы материала удаляются с поверхности и, впоследствии, осаждаются из лазерного факела на поверхность вокруг зоны воздействия в виде микро- и наночастиц. При осаждении таких частиц на нагретую поверхность происходит диффузионная сварка частиц с поверхностью, что способствует хорошей адгезии микро- и наночастиц к обрабатываемому материалу и высоким прочностным свойствам получаемого текстурированного покрытия.
Для снижения поверхностной энергии образцов со сформированным при лазерной обработке слоем текстуры использовали нанесение гидрофобного агента – метокси-{3 [(2, 2, 3, 3, 4, 4, 5, 5, 6, 6, 7, 7, 8, 8, 8-пентадекафтороктил)-окси]-пропил}-силана, синтезированного в лаборатории академика А.М. Музафарова. Обогащение поверхности вольфрама хемосорбционно-активными центрами, необходимыми для дальнейшей гидрофобизации, проводили на установке Plasma Cleaner PDC-030 (Zhengzhou CY Scientific Instrument, Китай). В данной работе применяли кислородную плазму при давлении О2 – 20–30 Па [19, 20].
Гидрофобизация состоит из нескольких основных этапов. Первый – обработка в кислородной плазме для формирования на поверхности хемосорбционных центров. С ними будет связываться гидрофобный агент – фтороксисилан. Второй этап – хемосорбция гидрофобного агента из паров. Процесс происходит в герметичном сосуде в печи при температуре Т = 105°С. Чтобы удалить лишний, физически адсорбированный гидрофобизатор с поверхности, образцы отмывали сначала в спирте, а затем в ацетоне. После отмывки образцы помещали на 1 ч в печь, нагретую до 150°С.
Время и температура, при которой проводили осаждение гидрофобизатора из паров, соответствовали значениям, оптимизированным в предыдущих работах – 1 ч в печи при температуре 105°С [21]. Время обработки в плазме варьировали для определения оптимальных времен для каждого из исследованных металлов.
В качестве тестовой жидкости для определения углов смачивания и скатывания использовалась дистиллированная вода. Угол смачивания определяли на установке, подробно описанной в [13], как среднее арифметическое значений, полученных на пяти разных участках покрытия. Угол скатывания капли воды измеряли с помощью установки, представленной на рис. 1, помещая каплю воды объемом 15 мкл на горизонтальную поверхность. Регулирование наклона поверхности и скорости вращения происходило вручную. Углом скатывания считали угол наклона, при котором начиналось движение капли по поверхности. Точность отсчета углов скатывания на данной установке составляет 3ꞌ.
Химическую стойкость покрытия при контакте с водой и парами воды исследовали в атмосфере насыщенных водяных паров [13], чтобы снизить скорость испарения капли. Для исследования стойкости при контакте с водой, на поверхность образца помещали каплю воды и следили за изменением ее угла смачивания, поверхностного натяжения, контактного диаметра и объема во времени.
РЕЗУЛЬТАТЫ И ОБСУЖДЕНИЕ
Для начала было исследовано влияние обработки в плазме на угол смачивания исходного гладкого образца вольфрама. Для этого мы отмывали вольфрамовые пластины в ультразвуковой ванне сначала в изопропиловом спирте, а затем в дистиллированной воде в течение 10 мин, пластину промокали обеззоленным фильтром, после чего измеряли угол смачивания. Далее пластины обрабатывали в кислородной плазме в течение 5, 7, 10, 15 и 20 мин и снова измеряли углы смачивания. В табл. 1 приведены значения углов смачивания при разном времени обработки в плазме.
Таблица 1.
Углы смачивания вольфрама при различных временах обработки в плазме
Время обработки, мин | Угол смачивания, град |
---|---|
0 | 86.7 ± 2.3 |
5 | 42.5 ± 3.5 |
7 | 22.5 ± 1.3 |
10 | Полное растекание |
15 | Полное растекание |
20 | Полное растекание |
Углы смачивания сильно уменьшаются при увеличении времени обработки, а при времени обработки в плазме более 10 мин капля воды полностью растекается по поверхности, что говорит о том, что обработка в плазме является эффективным методом прививки гидроксильных групп, легко образующих гидратную оболочку при контакте с водой. Именно благодаря большому количеству гидратированных гидроксильных групп, поверхность вольфрамового образца показывает изменение угла смачивания от 86° для необработанного плазмой образца, до 0° – для обработанного.
Рассмотрим теперь влияние времени обработки в плазме на химическую стойкость текстурированных покрытий после хемосорбции на поверхность молекул фтороксисилана. Для этого обсудим подробнее процесс гидрофобизации. На первой стадии – при обработке поверхности в плазме – ионизированные частицы кислорода, контактируя с атомами на поверхности, образуют полярные гидроксильные и карбоксильные группы, которые являются хемосорбционными центрами.
На втором этапе – осаждение гидрофобизатора из паров – группа –ОСН3 гидрофобного агента взаимодействует с поверхностной группой –ОН по реакции:
Последней стадией гидрофобизации является нагрев в печи для сшивания молекул гидрофобизатора. После осаждения из паров на поверхности присутствует химически и физически адсорбированный гидрофобизатор. При нагреве соседние молекулы хемосорбированного гидрофобизатора образуют силоксановые связи, как показано на рис. 2.
Рис. 2.
Схема кросс-сшивки хемосорбированных молекул гидрофобизатора с образованием силоксановой связи.
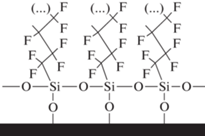
Физически адсорбированные молекулы остаются на поверхности и отрицательно влияют на сохранение супергидрофобного состояния покрытия. Это происходит потому, что три концевые функциональные группы –ОСН3 молекулы фто-роксисилана легко взаимодействуют с водой с образованием силанольных групп:
Гидратация силанольных групп при контакте с водой приводит к снижению угла смачивания и, в ряде случаев, к потере супергидрофобного состояния.
При малом времени обработки в плазме расстояние между хемосорбционными центрами на поверхности оказывается достаточно большим, что не позволяет молекулам сшиться друг с другом. В этой ситуации, после длительного нахождения в воде, на поверхности будут образовываться небольшие фильные участки, будет наблюдаться падение угла смачивания из-за гидратации несвязанных –ОН групп гидрофобизатора.
При слишком большом времени обработки в плазме на поверхности образуется много близко расположенных хемосорбционных –ОН центров. Адсорбция фтороксисиланов на такие центры и взаимодействие функциональных оксиметильных групп соседних молекул в присутствии воды приводит к образованию силоксановых связей, поперечно сшивающих адсорбционный монослой. При расстояниях между поверхностными –ОН группами менее длины Si–O–Si связи, формирующиеся силоксановые связи оказываются деформированными. Вследствие этого при длительном контакте такого покрытия с водой облегчается разрыв силоксановой связи с дальнейшим образованием концевых силанольных групп, что приводит к падению угла смачивания.
В оптимальном случае количество хемосорбционных центров должно быть таким, чтобы между ними было расстояние, достаточное для сшивания молекул гидрофобизатора, при этом не должно быть пустых или сильно наполненных участков.
Чтобы узнать, сколько именно времени нужно обрабатывать образцы вольфрама в плазме, мы приготовили несколько образцов, текстурированных с применением одного и того же режима лазерной обработки. Время обработки в плазме составило 5, 7, 10, 13, 15 и 20 мин. После обработки в плазме проводили хемосорбцию гидрофобизатора из паров, как описано выше, и далее образцы отжигали в сушильном шкафу. Все приготовленные описанным методом образцы демонстрировали супергидрофобное состояние, на что указывали их углы смачивания, которые превышали 170°, и низкие углы скатывания водных капель (<2°).
О химической стойкости судили по времени контакта капли с поверхностью, в течение которого угол смачивания капли оставался неизменным.
На рис. 3 изображены графики изменения угла смачивания поверхностей гидрофобизованного вольфрама при временах их обработки в плазме на этапе приготовления покрытий 5, 7, 10, 13, 15 и 20 мин (а) и поверхностного натяжения капли воды, контактировавшей с поверхностью, обработанной 5, 10 и 20 мин (б). Образец, который обрабатывали в плазме 5 мин, не показал долгосрочную стабильность при контакте с водой. Угол смачивания упал до значения 153.5° менее чем за сутки. 7-минутная обработка оказалась немного лучше, угол смачивания не падал в течение 31 ч, но потом начал резко уменьшаться. Такое поведение мы связываем с тем, что при растекании капля попала на участок с недостаточной плотностью молекул гидрофобизатора. Это тот случай, когда обработка в плазме была недостаточно длительной, чтобы получить равномерное распределение хемосорбционных центров по поверхности. Натекание капли на более фильный участок, не полностью закрытый слоем гидрофобизатора, вызывает взаимодействие воды с триоксидом вольфрама, образованным в процессе лазерного текстурирования, и формирование гидратов [22]. Как следствие, угол смачивания начинает уменьшаться. Обработки в плазме в течение 10 мин было достаточно, чтобы обеспечить стабильность супергидрофобного состояния в течение двух суток. Через 2500 мин капля, растекаясь, встречает дефект смачивания, после чего угол смачивания начинает падать. Обработка образцов в плазме в течение 13, 15 и 20 мин показала дальнейшее улучшение состояние покрытия на вольфраме и его большую химическую стойкость. При длительности плазменной обработки 15 и 20 мин стабильность угла смачивания сохраняется около трех суток. Наблюдающееся после 60 ч контакта капли с покрытием медленное падение угла, по-видимому, связано с испарением капли из-за небольшого недосыщения атмосферы в экспериментальной ячейке парами воды. Для дополнительного подтверждения высокой химической стойкости супергидрофобных покрытий, полученных при больших временах обработки в плазме, мы исследовали поведение поверхностного натяжения водной капли, контактировавшей с покрытием.
Рис. 3.
Изменение углов смачивания супергидрофобных поверхностей вольфрама при времени их обработки в плазме на этапе приготовления покрытий 5, 7, 10, 13, 15 и 20 мин (а), изменение поверхностного натяжения капли воды, контактировавшей с поверхностью, обработанной в плазме 5, 10, 20 мин (б).
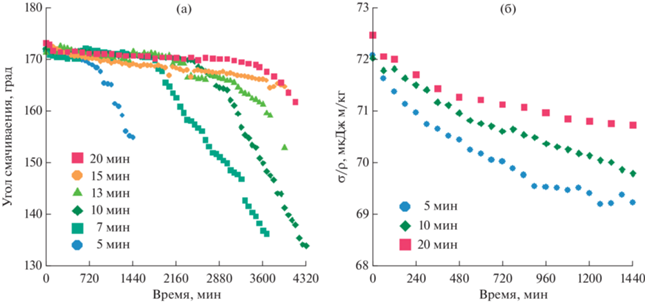
На рис. 3б показано изменение поверхностного натяжения капель, контактировавших с образцами, которые обрабатывали в плазме 5, 10 и 20 мин. Как было описано выше, химически стойкими образцами являются те, контакт капли воды с которыми не сопровождается значительным падением поверхностного натяжения. Согласно данным, представленным на рис. 3б, падение поверхностного натяжения водных капель наблюдается на всех образцах. Однако целесообразно выбрать тот режим обработки, при котором поверхностное натяжение будет падать в меньшей степени. Из графика следует, что поверхностное натяжение меньше всего меняется у образца, который обрабатывали в плазме в течение 20 мин. Именно он показал наибольшее постоянство угла смачивания при непрерывном длительном контакте с водой.
Таким образом, наибольшей стойкости супергидрофобного покрытия на вольфраме соответствует нанесение гидрофобизатора из паров на поверхность, предобработанную в кислородной плазме в течение 20 мин. Стойкость покрытия, полученного в этих условиях, оказывается достаточной для практического применения таких покрытий, сопровождающегося периодическим контактом покрытий с водой.
Здесь было также интересно исследовать стойкость полученных супергидрофобных покрытий и к солевым хлоридсодержащим растворам, являющимся коррозионно-активными средами. Данные по эволюции угла смачивания и поверхностного натяжения капли 0.5 М водного раствора NaCl на покрытии, полученном при 10 мин плазменной обработки, представлены на рис. 4.
Рис. 4.
Изменение угла смачивания (а) и поверхностного натяжения (б) для капли деионизованной воды (1) и капли 0.5 М водного раствора NaCl (2) на супергидрофобной поверхности вольфрама, полученной при 10 мин плазменной обработки.
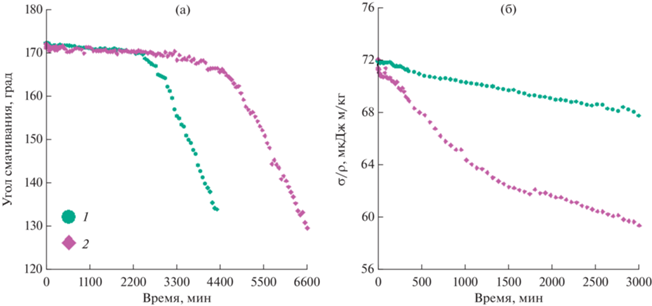
Для сравнения на этих же рисунках показаны данные для капли дистиллированной воды. Представленные результаты показывают, что в течение 24 ч угол смачивания раствором соли практически не меняется, указывая на хорошие защитные свойства покрытия. Однако падение поверхностного натяжения капли солевого раствора за 24 ч непрерывного контакта оказалось значительно больше, чем для капли воды на том же временном интервале. Полученный экспериментальный результат не удивителен, если учесть, что гидролиз связи Si–O–Metal в растворах солей идет более интенсивно, чем в деионизованной воде [11]. В исследуемой нами системе гидролиз связи Si–O–W приводит к десорбции гидрофобного агента с поверхности и его переходу на границу капля/пар, что и отражается в падении поверхностного натяжения капли раствора до ≈63 мН/м. В то же время, такое небольшое снижение указывает лишь на очень незначительную десорбцию гидрофобного агента, что обеспечивает длительное сохранение практически постоянного значения угла смачивания.
Представляло интерес выяснить, является ли подобранный режим обработки в плазме универсальным для различных металлических материалов с целью получения стойких супергидрофобных покрытий. Для этого нами была исследована стойкость супергидрофобных покрытий на лазерно-текстурированных поверхностях образцов из алюминиевого сплава Д16 при использовании того же гидрофобизатора, фтороксисилана, что и в описанных выше экспериментах, с использованием времен обработки в кислородной плазме 3, 5, 10 и 20 мин. Для всех образцов углы смачивания превышали 170°, а углы скатывания были менее 2°.
На рис. 5 представлены графики изменения угла смачивания и поверхностного натяжения для образцов из сплава алюминия Д16 при разном времени обработки в плазме.
Рис. 5.
Изменение углов смачивания (а) и поверхностного натяжения капли (б) при обработке образцов в плазме в течение 3, 5, 10 и 20 мин для супергидрофобной поверхности сплава алюминия Д16.
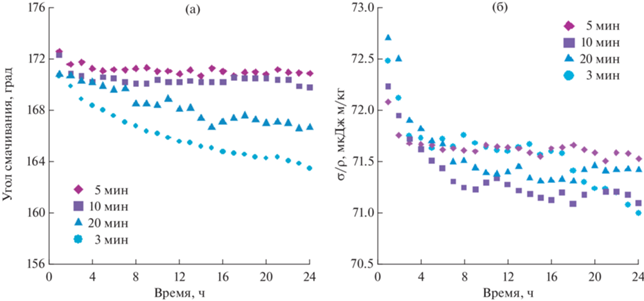
Образец, который обрабатывали в плазме в течение 3 мин, показал хоть и медленное, но непрерывное ухудшение супергидрофобного состояния, угол смачивания упал до 163° менее чем за 24 ч, что связано с недостаточным количеством хемосорбционных центров, как обсуждалось ранее. При обработке образцов в плазме 5 и 10 мин наблюдается незначительное падение угла, за сутки угол упал менее чем на 2°. Причем разброс данных находится в пределах погрешности, то есть эти два образца практически не различаются. Поведение угла смачивания для образцов, подвергнутых 20 мин обработки в плазме, оказывается заметно хуже. За сутки угол уменьшился примерно на 5°. Значит, при 20-мин обработке образуется много близко расположенных хемосорбционных центров с деформированными силоксановыми связями, которые разрушаются при контакте с водой.
Для выбора оптимального времени обработки был проведен также анализ изменения поверхностного натяжения капель. По данным на рис. 5б можно сделать вывод, что наименьшее падение поверхностного натяжения происходит при 5-минутной обработке в плазме. Отметим, что наблюдающиеся на рис. 5б колебания поверхностного натяжения согласуются с изменением температуры в лаборатории в течение суток, поскольку ночное понижение температуры на 1–2°C должно вызывать рост поверхностного натяжения водной капли.
ВЫВОДЫ
В работе исследовано влияние времени обработки в плазме на химическую стойкость полученных супергидрофобных покрытий при контакте с водой и солевым раствором. На примере алюминия и вольфрама показано, что оптимальные времена обработки оказываются различными для разных материалов. Поэтому разработка технологии получения химически стойких супергидрофобных покрытий должна включать определение оптимального времени обработки в плазме.
Список литературы
Rico V., Mora J., García P., Agüero A., Borrás A., González-Elipe A.R., López-Santos C. Robust anti-icing superhydrophobic aluminum alloy surfaces by grafting fluorocarbon molecular chains // Applied Materials Today. 2020. V. 21. P. 100815. https://doi.org/10.1016/j.apmt.2020.100815
Piscitelli F., Chiariello A., Dabkowski D., Corraro G., Marra F., Di Palma L. Superhydrophobic coatings as anti-icing systems for small aircraft // Aerospace. 2020. V. 7. № 1. P. 2. https://doi.org/10.3390/aerospace7010002
Balordi M., Cammi A., De Magistris G.S., Chemelli C. Role of micrometric roughness on anti-ice properties and durability of hierarchical super-hydrophobic aluminum surfaces // Surface and Coatings Technology. 2019. V. 374. P. 549–556. https://doi.org/10.1016/j.surfcoat.2019.06.001
Rasitha T.P., Vanithakumari S.C., Krishna D.N.G., George R.P., Srinivasan R., Philip J. Facile fabrication of robust superhydrophobic aluminum surfaces with enhanced corrosion protection and antifouling properties // Progress in Organic Coatings. 2022. V. 162. P. 106560. https://doi.org/10.1016/j.porgcoat.2021.106560
Trávníčková E., Pijakova B., Marešová D., Bláha L. Antifouling performance of photocatalytic superhydrophobic coatings against Klebsormidium alga // Journal of Environmental Chemical Engineering. 2020. V. 8. № 5. P. 104153. https://doi.org/10.1016/j.jece.2020.104153
Xu S., Wang Q., Wang N., Zheng X. Fabrication of su-perhydrophobic green surfaces with good self-cleaning, chemical stability and anti-corrosion properties // Journal of Materials Science. 2019. V. 54. № 19. P. 13006–13016. https://doi.org/10.1007/s10853-019-03789-x
Уколов А.И., Попова Т.Н. Эффективность применения коммерческих супергидрофобных покрытий в приложениях морской индустрии // Колло-ид. журн. 2022. Т. 84. № 4. С. 475–487. https://doi.org/10.31857/S0023291222040115
Yao W., Liang W., Huang G., Jiang B., Atrens A., Pan F. Superhydrophobic coatings for corrosion protection of magnesium alloys // Journal of Materials Science & Technology. 2020. V. 52. P. 100–118. https://doi.org/10.1016/j.jmst.2020.02.055
Lu Y., Guan Y., Li Y., Yang L., Wang M., Wang Y. Nanosecond laser fabrication of superhydrophobic surface on 316L stainless steel and corrosion protection application // Colloids and Surfaces A: Physicochemical and Engineering Aspects. 2020. V. 604. P. 125259. https://doi.org/10.1016/j.colsurfa.2020.125259
Коляганова О.В., Дуридивко М.О., Климов В.В., Ле М.Д., Харламов В.О., Брюзгин Е.В., Навроцкий А.В., Новаков И.А. Высоко- и супергидрофобные покрытия на основе льняного масла и сополимеров глицидилметакрилата и (фтор)алкилметакрилатов для поверхности древесины // Коллоид. журн. 2022. Т. 84. № 4. С. 421–432. https://doi.org/10.31857/S0023291222040073
Boinovich L.B., Emelyanenko A.M. The behaviour of fluoro- and hydrocarbon surfactants used for fabrication of superhydrophobic coatings at solid/water interface // Colloids and Surfaces A: Physicochemical and Engineering Aspects. 2015. V. 481. P. 167–175. https://doi.org/10.1016/j.colsurfa.2015.05.003
Kulinich S.A., Honda M., Zhu A.L., Rozhin A.G., Du X.W. The icephobic performance of alkyl-grafted aluminum surfaces // Soft Matter. 2015. V. 11. № 5. P. 856–861. https://doi.org/10.1039/C4SM02204A
Boinovich L.B., Emelyanenko A.M., Pashinin A.S. Analysis of long-term durability of superhydrophobic properties under continuous contact with water // ACS Applied Materials & Interfaces. 2010. V. 2. № 6. P. 1754–1758. https://doi.org/10.1021/am100241s
Zhang C., Liang F., Zhang W., Liu H., Ge M., Zhang Y., Tang Y. Constructing mechanochemical durable and self-healing superhydrophobic surfaces // ACS Omega. 2020. V. 5. № 2. P. 986–994. https://doi.org/10.1021/acsomega.9b03912
Boinovich L.B., Modin E.B., Sayfutdinova A.R., Emelyanenko K.A., Vasiliev A.L., Emelyanenko A.M. Combination of functional nanoengineering and nanosecond laser texturing for design of superhydrophobic aluminum alloy with exceptional mechanical and chemical properties // ACS Nano. 2017. V. 11. № 10. P. 10113–10123. https://doi.org/10.1021/acsnano.7b04634
Sebastian D., Yao C.W., Lian I. Mechanical durability of engineered superhydrophobic surfaces for anti-corrosion // Coatings. 2018. V. 8. № 5. P. 162. https://doi.org/10.3390/coatings8050162
Рудакова А.В. Фотоиндуцированное изменение гидрофильности поверхности тонких пленок // Коллоид. журн. 2021. Т. 83. № 1. С. 3–34. https://doi.org/10.31857/S0023291221010109
Sataeva N.E., Boinovich L.B., Emelyanenko K.A., Domantovsky A.G., Emelyanenko A.M. Laser-assisted processing of aluminum alloy for the fabrication of superhydrophobic coatings withstanding multiple degradation factors // Surface and Coatings Technology. 2020. V. 397. P. 125993. https://doi.org/10.1016/j.surfcoat.2020.125993
Latthe S.S., Sutar R.S., Kodag V.S., Bhosale A.K., Kumar A.M., Sadasivuni K.K., Liu S. Self-cleaning supe-rhydrophobic coatings: Potential industrial applications // Progress in Organic Coatings. 2019. V. 128. P. 52–58. https://doi.org/10.1016/j.porgcoat.2018.12.008
Ijaola A.O., Farayibi P.K., Asmatulu E. Superhydrophobic coatings for steel pipeline protection in oil and gas industries: a comprehensive review // Journal of Natural Gas Science and Engineering. 2020. V. 83. P. 103544. https://doi.org/10.1016/j.jngse.2020.103544
Кузина Е.А., Емельяненко К.А., Домантовский А.Г., Емельяненко А.М., Бойнович Л.Б. Получение стойких супергидрофобных покрытий на поверхности краски с применением лазерной обработки и нанесения гидрофобизатора // Коллоид. журн. 2022. Т. 84. № 4. С. 453–464. https://doi.org/10.31857/S0023291222040097
Zheng H., Ou J.Z., Strano M.S., Kaner R.B., Mitchell A., Kalantar-zadeh K. Nanostructured tungsten oxide-properties, synthesis, and applications // Adv. Funct. Mater. 2011. V. 21. № 12. P. 2175–2196. https://doi.org/10.1002/adfm.201002477
Дополнительные материалы отсутствуют.
Инструменты
Коллоидный журнал