Коллоидный журнал, 2022, T. 84, № 4, стр. 453-464
Получение стойких супергидрофобных покрытий на поверхности краски с применением лазерной обработки и нанесения гидрофобизатора
Е. А. Кузина 1, *, К. А. Емельяненко 1, А. Г. Домантовский 1, А. М. Емельяненко 1, Л. Б. Бойнович 1
1 Институт физической химии и электрохимии им. А.Н. Фрумкина РАН
119991 Москва,
Ленинский пр., д. 31, корп. 4, Россия
* E-mail: kuzina.katya26.01@gmail.com
Поступила в редакцию 29.04.2022
После доработки 12.05.2022
Принята к публикации 14.05.2022
- EDN: TZITQS
- DOI: 10.31857/S0023291222040097
Аннотация
Создана серия супергидрофобных покрытий с использованием метода лазерной обработки поверхности краски с последующей хемосорбцией гидрофобного агента. Варьирование режимов лазерной обработки позволило получить поверхности с различной морфологией. Кроме этого, исследована химическая и механическая стойкость покрытия. Представлен метод придания супергидрофобных свойств, позволяющий в значительной степени повысить химическую стойкость и достичь удовлетворительной механической стойкости супергидрофобного покрытия.
ВВЕДЕНИЕ
Сегодня авиационно-космический комплекс является одной из самых быстро развивающихся отраслей промышленности. Одним из направлений развития является создание лакокрасочных покрытий, способных соответствовать ряду требований – покрытия должны защищать детали самолета от воздействия влаги, воздействия ультрафиолетового излучения, агрессивного воздействия авиационно-ракетных топлив, сохраняя при этом эстетичный внешний вид. Однако, во многих случаях эта защита недостаточно эффективна: краска в условиях эксплуатации истирается при контакте с абразивными частицами, присутствующими в воздухе, не защищает в полной мере от коррозии, отслаивается от поверхностей при перепадах температур, покрывается толстым слоем льда при соприкосновении с переохлажденными каплями воды. Поэтому немаловажной задачей современных исследований является создание такого покрытия, которое будет эффективно защищать авиационные конструкционные материалы.
По данным литературы, супергидрофобные покрытия являются одними из самых эффективных защитных покрытий. Высокие антикоррозионные свойства [1–3], стойкость к биологическим загрязнениям [4–6], к обледенению [7–9] и стабильность супергидрофобных покрытий при их эксплуатации обусловлены особыми свойствами таких покрытий при контакте с водной средой, малой площадью контакта с агрессивными жидкостями и высокой адгезией молекул гидрофобного агента к материалу покрытия. Супергидрофобность может заметно увеличить устойчивость к различным эксплуатационным нагрузкам. Однако супергидрофобным покрытиям присущи некоторые недостатки, обсуждавшиеся в [10, 11] и связанные с недостаточной химической стойкостью гидрофобизатора, который нанесен на текстуру, и невысокой механической стойкостью элементов текстуры поверхности. Ранее в литературе обсуждались методы увеличения стойкости покрытий к различным воздействиям, и было показано [10–14], что проблема механической и химической стойкости супергидрофобных покрытий может быть решена путем подбора состава поверхностного слоя, морфологии и химического состава гидрофобного агента.
Для создания супергидрофобных покрытий на различных материалах существует три основных требования. Это придание поверхности материала низкой поверхностной энергии, формирование на поверхности обрабатываемого материала текстуры, характеризующейся многомодальной шероховатостью, и, наконец, подбор формы и размеров элементов текстуры, для обеспечения требуемого юнговского угла [15].
К настоящему времени разработано множество методов придания поверхности шероховатости. Для этой цели применяют, например, плазменное травление поверхности полимеров [16, 17], нанесение пленок сублимирующихся материалов [18], применение органических и неорганических наполнителей, встроенных в матрицу гидрофобного материала [19], контролируемое агрегирование наночастиц на поверхности [20] и др. Зачастую отдельные элементы текстуры в данных методах оказываются достаточно хрупкими, что приводит к низкой износостойкости покрытий. Поэтому был предложен метод получения нано- и микротекстур на поверхности с применением лазерной обработки [11, 13, 21, 22], который позволяет повышать механическую прочность текстуры за счет изменения химического и фазового состава, а также структуры материала.
Большая часть данных литературы относится к супергидрофобным покрытиям, которые были созданы на стекле [23], металлических подложках, включая алюминий [13], сталь [1, 24], медь [25], титановый сплав [26] и на различных полимерных материалах [27–30]. Создание и исследования супергидрофобных покрытий на поверхности краски в литературе до последнего времени отсутствовали. Недавно был предложен метод получения супергидрофобных лакокрасочных покрытий с использованием фемтосекундного импульсного лазера [31]. Однако, в этой работе не в полной мере рассмотрена эволюция свойств полученного покрытия при длительном воздействии возможных эксплуатационных нагрузок, что является довольно важной частью анализа. Исследование стойкости позволяет оценить возможность длительного использования полученных покрытий в жестких атмосферных условиях.
В данном исследовании мы впервые применили наносекундную лазерную обработку для создания супергидрофобного покрытия на элементах конструкций из углепластика, покрытых слоем краски. Такие материалы обычно используются для беспилотных летательных аппаратов. Были подобраны такие режимы текстурирования, при которых не произошло изменения цвета краски и нарушения красочного слоя. Кроме того, было изучено поведение полученного супергидрофобного покрытия в условиях, характерных для эксплуатации покрытий, т.е. при контакте с водой, водяными парами и при абразивном износе.
МАТЕРИАЛЫ И МЕТОДЫ
В качестве подложек для приготовления супергидрофобных покрытий использовали пластину из углепластика, на которую была нанесена краска – фторполиуретановая эмаль марки ВЭ-69 (производитель – ФГУП “ВИАМ”). Она обеспечивает требуемые оптические и декоративные характеристики и защищает полимерные композиционные материалы от разрушающего воздействия окружающей среды [32]. Для придания поверхности шероховатости и создания поверхностной текстуры мы использовали обработку поверхности импульсным лазерным излучением. В данной работе использовался инфракрасный иттербиевый волоконный лазер с длиной волны 1.064 мкм, с возможностью выбора длительности импульсов в интервале от 4 до 200 нс, частотой импульсов от 20 до 100 кГц, пиковой мощностью до 0.95 мДж в моде TEM00. Луч лазера фокусировался на поверхности обрабатываемого образца и, с помощью управляемой с компьютера двухосевой отклоняющей системы MS10 (Raylase, Германия), перемещался по поверхности образца в двух взаимно перпендикулярных направлениях. В зоне воздействия лазерного луча происходит нагрев до высокой температуры, плавление и возгонка или взрывная абляция материала краски, в процессе которой частицы материала вылетают с поверхности и осаждаются вокруг зоны воздействия в виде микро- и наночастиц.
При подборе режима, меняя такие параметры, как мощность лазера, скорость обработки, частоту и длительность импульса, мы получали различные текстуры. Лакокрасочное покрытие может эксплуатироваться в интервале температур от ‒60 до 120°С. Поэтому нужно подбирать параметры текстурирования таким образом, чтобы не изменить свойства краски. Кроме того, слой краски достаточно тонкий (35–55 мкм), поэтому необходимо использовать низкую мощность лазера для того, чтобы не удалить слой краски при абляции.
Мощность лазера измеряли с помощью установки Thermal Powermeter S322C (THORLabs USA).
Перед обработкой пластины мыли под проточной водой от пыли и грязи, сушили, обезжиривали изопропиловым спиртом и далее текстурировали.
Для снижения поверхностной энергии краски со сформированным при лазерной обработке слоем текстуры, использовали нанесение гидрофобного агента – метокси-{3[(2,2,3,3,4,4,5,5,6,6,7,7,8,8,8-пентадекафтороктил)-окси]-пропил}-силана, синтезированного в лаборатории А.М. Музафарова. Для подготовки поверхности краски к гидрофобизации использовали установку Plasma Cleaner PDC-030 (Zhengzhou CY Scientific Instrument, Китай). С помощью атмосферной плазмы при давлении 30–50 Па проводилась очистка поверхности от органических и биологических загрязнений [33]. При реакции ионизированных частиц кислорода, азота и водорода с атомами на поверхности краски происходит удаление с поверхности различных загрязнений и формирование полярных карбонильных и карбоксильных групп на очищенной поверхности [34]. Полярные ка-боксильные группы являются хемосорбционными центрами для молекул используемого нами гидрофобизатора.
Для приготовления образцов супергидрофобного покрытия на краске в этой работе использовались два протокола. Первый включал в себя следующие операции. После лазерного текстурирования образцы погружали в воду и помещали в ультразвуковую ванну на 10 мин для очистки от наночастиц, имеющих низкую адгезию к поверхности краски. Далее образцы сушились при 105°С в течение 30 мин. После сушки образцы подвергались обработке в атмосферной плазме в течение 5 минут для образования хемосорбционных центров [35, 36]. Стоит отметить, что в методах, описанных в литературе, как правило, использовали другой метод прививки гидроксилов – образцы обрабатывали в ультрафиолете и озоне. Данный метод не подходит для используемой краски, так как длительное воздействие ультрафиолета может способствовать разрушению краски. При обработке плазмой также имеет место воздействие ультрафиолета, но оно не такое длительное – 5 мин вместо предложенных в литературе 90 [21]. Далее образцы выдерживали в герметичном сосуде с насыщенными парами фтороксисилана в течение 1 ч при температуре 105°С. Гидрофобный агент конденсировался на поверхности, хемосорбируясь на активных центрах микро- и наноэлементов текстуры. После хемосорбции фтороксисилана образцы отмывали в изопропиловом спирте, а затем в ацетоне, для удаления физически адсорбированных молекул гидрофобизатора. Далее образцы сушили в печи при температуре 105°С, при этом образовывался поперечно сшитый силоксановыми связями слой фтороксисилана на текстурированной лазером поверхности.
Далее представлен порядок приготовления образцов по второму протоколу.
Сначала образцы текстурировали режимом 1 (детали обработки см. ниже) для получения нано- и микротекстур на поверхности. Затем образцы погружали в деионизованную воду и обрабатывали в ультразвуковой ванне для удаления наночастиц с низкой адгезией к поверхности. Образцы сушили в печи при температуре 105°С, а затем обрабатывали в атмосферной плазме в течение 5 минут при давлении 30–50 Па. Чтобы раскрыть мелкие поры, в которые не могут проникнуть частицы гидрофобизатора, образцы выдерживали в растворе декана и фтороксисилана (концентрация 0.01%) в течение 2 ч, а затем сушили образцы в печи в течение 2 ч, чтобы полностью удалить декан с поверхности. Далее погружали образец с текстурированной поверхностью в воду и отбивали наночастицы со слабой адгезией к поверхности в ультразвуковой ванне на низкой мощности в течение 3 мин. Гидрофобизация из паров фтороксисилана проводилась в герметичном сосуде при 105°С. Далее, образцы отмывались в спирте, а затем в ацетоне для удаления физически адсорбированных молекул гидрофобизатора. Для получения сшитого слоя гидрофобизатора образцы выдерживали 1 ч в сушильном шкафу при температуре 105°С. При наличии в системе достаточного количества воды доминирующим процессом становится поликонденсация трифункциональных силанов в двухмерные силоксаны, привитые к поверхности. Отличие второго протокола от первого заключается в дополнительных операциях по нанесению гидрофобизатора на стенки нанопор из раствора в декане за счет набухания краски и по удалению наночастиц со слабой адгезией к поверхности перед повторным нанесением гидрофобизатора, уже из паров.
В качестве тестовой жидкости для определения углов смачивания и скатывания использовалась дистиллированная вода. Угол контакта определяли, как среднее арифметическое значений, полученных на пяти разных местах покрытия. Угол скатывания капли воды измеряли, помещая каплю воды объемом 15 мкл на горизонтальную поверхность и затем, медленно наклоняли эту поверхность до тех пор, пока капля не начнет скатываться. С использованием гониометрической шкалы определяли угол наклона, при котором начиналось движение капли по поверхности. Критерием правильности подбора режима текстурирования принимали угол смачивания выше 170 градусов и угол скатывания меньше 5 градусов.
Химическую стойкость покрытия при контакте с водой и парами воды исследовали внутри двойной кюветы, позволяющей поддерживать 100% влажность. Для исследования стойкости при контакте с водой, на поверхность образца помещали каплю воды и следили за изменением ее угла смачивания, поверхностного натяжения, контактного диаметра и объема во времени. Эксперимент проводили в атмосфере насыщенных водяных паров, чтобы снизить скорость испарения капли.
Для проверки стойкости к контакту с парами воды образец выдерживали в двойной кювете в условиях влажности, близкой к 100%, в течение нескольких часов. Каждый час образец доставали из кюветы, измеряли углы смачивания и скатывания, а затем помещали обратно в пары.
Механическую стойкость структур поверхности проверяли по стандарту ASTM F735 [37, 38]. Образец закреплялся на дне емкости, засыпался слоем калиброванного песка (фракция от 500 до 800 мкм) высотой 20 мм. Емкость с песком помещали на платформу вибрационного шейкера Vibramax 100 (Heidolph, Германия), которая совершала возвратно-поступательные движения с частотой 1050 мин–1 и амплитудой 3 мм. Силы инерции заставляют всю массу песка перемещаться внутри емкости и оказывать значительное абразивное воздействие на поверхность закрепленного на дне емкости образца.
РЕЗУЛЬТАТЫ И ОБСУЖДЕНИЕ
В нашей работе было исследовано большое количество образцов, полученных при различных режимах обработки поверхности лазером. Рекомендуемая максимальная температура эксплуатации используемой нами краски составляет 120°С. Поэтому во всех режимах лазерной обработки была снижена мощность и увеличена скорость обработки, что позволяло снизить локальный нагрев поверхности при взаимодействии с лазерным лучом. В табл. 1 представлены некоторые режимы обработки поверхности, при которых получалась многомодальная текстура поверхности и после гидрофобизации наблюдались наибольшие углы смачивания и наименьшие углы скатывания.
Таблица 1.
Параметры текстурирования
Образец | Мощность, Вт |
Частота импульсов, кГц | Длительность импульса, нс | Скорость линейного перемещения луча, мм/с | Плотность линий, мм–1 |
---|---|---|---|---|---|
1 | 18.1 | 300 | 20 | 1500 | 20 |
18.0 | 200 | 30 | 7500 | 20 | |
2 | 18.1 | 300 | 20 | 1500 | 20 |
18.0 | 200 | 30 | 3250 | 20 | |
3 | 18.1 | 300 | 20 | 3250 | 20 |
18.0 | 200 | 30 | 7500 | 20 | |
4 | 15.2 | 300 | 20 | 1500 | 20 |
18.0 | 200 | 30 | 7500 | 20 | |
5 | 15.2 | 300 | 20 | 1500 | 20 |
15.2 | 200 | 30 | 7500 | 20 |
Для детального понимания процессов, происходящих на поверхности, мы исследовали смачивание поверхности нашего образца на каждом этапе создания покрытий. Для этого измеряли углы смачивания с помощью автоматизированной установки, созданной в лаборатории и описанной в литературе [39].
Угол смачивания — характеристика, которая чрезвычайно чувствительна к химическому составу и состоянию поверхности. Таким образом, с помощью исследования угла смачивания можно быстро и без применения сложных, дорогостоящих методов исследования выявлять различные процессы, происходящие с подложкой [40].
Из соотношения Дерягина–Венцеля [41]
(1)
$\cos {\kern 1pt} \theta = \left( {S{\text{/}}{{S}_{0}}} \right)\cos {\kern 1pt} {{\theta }_{0}} = r{\kern 1pt} \cos {\kern 1pt} {{\theta }_{0}},$Таблица 2.
Углы смачивания до и после текстурирования
Исходный ![]() |
Сразу после текстурирования ![]() |
Через 15 мин контакта ![]() |
---|---|---|
80.2 ± 1.3 | 130.2 ± 1.1 | <90 |
На представленных в табл. 2 изображениях видно, что после лазерного текстурирования угол смачивания увеличился от 80° до 130°. Можно было бы предположить, что не падение угла смачивания, как следует из уравнения Дерягина-Венцеля, а его рост после текстурирования поверхности, может быть связан с карбонизацией поверхностного слоя. Такая карбонизация может возникать в результате высокотемпературного локального нагрева поверхности при лазерной обработке и ее взаимодействия с компонентами воздушной среды с образованием гидрофобных С–Н связей на поверхности. Однако, изучение эволюции угла смачивания во времени в условиях насыщенных водяных паров показало, что с течением времени угол падал до ~60 градусов. Такое поведение угла смачивания можно объяснить тем, что сразу после нанесения капли воды на текстурированную краску устанавливается метастабильное состояние на сложном рельефе краски. Метастабильность связана с захватом воздуха в шероховатой текстуре в момент помещения капли на подложку.
Данные по изменению угла смачивания на текстурированном образце с увеличением времени контакта капли с краской показаны на рис. 1. Из этих данных следует, что угол смачивания начинает резко уменьшаться уже через несколько минут контакта и выходит на постоянное значение ≈60°, подтверждающее, что сама краска достаточно гидрофильна и наблюдавшийся сразу после нанесения капли угол в 130.2 ± 1, соответствовал метастабильному состоянию.
Рис. 1.
Изменение угла смачивания капли, нанесенной на поверхность после текстурирования. Измерения проводились в насыщенных водяных парах.
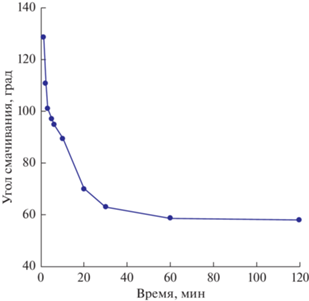
Ранее в литературе были подробно описаны теоретические основы создания супергидрофобных покрытий [41]. На шероховатых поверхностях реализуются два типа смачивания: гомогенный и гетерогенный. При гомогенном режиме вода смачивает всю поверхность твердого тела, заполняет все впадины рельефа, а при гетерогенном режиме внутри впадин находится воздух в термодинамически устойчивом состоянии. Угол смачивания в гомогенном режиме рассчитывают на основе соотношения Дерягина–Венцеля (уравнение (1)).
В гетерогенном режиме смачивания, который реализуется для супергидрофобных покрытий, угол смачивания описывается соотношением Касси–Бакстера:
где f – доля проекции смоченной площади на поверхность подложки с учетом частичного заполнения пор, r – коэффициент шероховатости смоченной поверхности.В табл. 3 представлены результаты измерения углов смачивания и скатывания после лазерной обработки и гидрофобизации для образцов, приготовленных по первому протоколу.
Таблица 3.
Углы смачивания и скатывания после гидрофобизации для разных режимов текстурирования
Режим | Угол смачивания, град | Угол скатывания, град |
---|---|---|
1 | 170.7 ± 0.7 | 4.0 ± 0.8 |
2 | 170.0 ± 1.3 | 6.0 ± 2.4 |
3 | 170.9 ± 0.3 | 6.1 ± 1.1 |
4 | 171.1 ± 0.8 | 4.9 ± 1.0 |
5 | 170.1 ± 0.6 | 10.6 ± 3.2 |
Наилучшим режимом приготовления образцов по первому протоколу оказался режим 1, поскольку в этом режиме достигались углы смачивания более 170° и наименьший угол скатывания (менее 4.5°). Для дальнейшей работы мы использовали образцы, полученные именно этим режимом.
Поскольку любые покрытия подвержены деградации при длительном нахождении в условиях эксплуатации, нами был проведен анализ долговечности наших покрытий при длительном контакте с водой. На рис. 2 представлен график зависимости угла смачивания и поверхностного натяжения капли воды во времени. Измерения проводились в условиях 100% влажности, что позволяет связать наблюдающееся изменение углов смачивания во времени, в основном, с невысокой стойкостью супергидрофобного покрытия при контакте с водой.
Рис. 2.
Изменение угла смачивания (1) и отношения поверхностного натяжения к плотности жидкости (2) для супергидрофобного образца, приготовленного по первому протоколу, при длительном контакте водной капли с поверхностью.
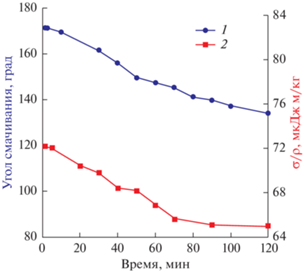
Уже через 2 ч угол смачивания падал до 135 град. При этом поверхностное натяжение капли тоже падало. Такую быструю деградацию супергидрофобного состояния мы связали с наличием на поверхности большого количества мелких пор, внутрь которых не может проникнуть гидрофобизатор. Попадание воды в эти гидрофильные поры приводит к их заполнению водой и, согласно закону Касси для химически гетерогенной поверхности, к понижению угла смачивания. Кроме того, часть молекул гидрофобизатора, физически адсорбированных на поверхности образца, по-видимому, десорбируется с поверхности краска/вода и переходит на поверхность капли. Такой переход инициируется снижением полной энергии системы за счет понижения поверхностной энергии капли и облегчается при низкой энергии физической адсорбции молекул гидрофобизатора к поверхности краски. На рис. 2 этот процесс проявляется в падении поверхностного натяжения капли.
Для увеличения стойкости поверхности к контакту с водой мы предложили поменять протокол изготовления супергидрофобного покрытия. Для покрытия гидрофобизатором внутренней поверхности пор и удаления с поверхности наночастиц, имеющих слабую адгезию к поверхности краски, было предложено изготавливать покрытие по второму протоколу. Стойкость покрытий к контакту с водой исследовали сразу после приготовления образцов и спустя сутки. Оказалось, что те образцы, которые были подвергнуты испытанию сразу после приготовления, проявили достаточно высокую стойкость к контакту с водой. Совсем иначе вели себя образцы, хранившиеся в лаборатории до испытания в течение суток. Сначала угол смачивания практически не менялся, но в какой-то момент времени начинал резко падать. Такое поведение можно объяснить тем, что в первом случае декан не полностью удалялся с поверхности и некоторое время оставался внутри пор текстуры краски. Таким образом, при испытаниях сразу после изготовления образцов, остававшийся в порах декан служил защитным барьером от проникновения воды в поры. В течение длительного хранения образца декан полностью испарялся из пор, открывая на поверхности участки, не покрытые гидрофобизатором. Когда капля воды попадала на такой участок, взаимодействие краски с водой приводило к нарушению осевой симметрии капли, а угол смачивания падал. Чтобы решить эту проблему, необходимо было удалить декан с поверхности до гидрофобизации из паров.
Для этого, после выдерживания текстурированной краски в декане и сушки, в ультразвуковой ванне отбивали наночастицы с низкой адгезией к поверхности. Чтобы не разрушить рельеф, удаление наночастиц с низкой адгезией к поверхности и остатков декана из пор проводили при низкой мощности ультразвуковой ванны в течение 3 мин. Углы смачивания и скатывания для нескольких образцов, приготовленных по улучшенному таким образом второму протоколу, представлены в табл. 4.
Таблица 4.
Значение углов смачивания и скатывания для четырех образцов, приготовленных по второму протоколу
Углы смачивания, град | Углы скатывания, град | |
---|---|---|
1 | 168.9 ± 0.7 | 4.5 ± 1.4 |
2 | 167.4 ± 2.5 | 5.3 ± 0.7 |
3 | 168.2 ± 0.5 | 4.6 ± 1.1 |
4 | 169.1 ± 0.8 | 4.8 ± 0.9 |
Сравнение начальных углов смачивания на образцах, полученных по первому протоколу (табл. 3, первая строка) с углами смачивания образцов, полученных по второму протоколу (табл. 4), показывает, что дополнительное удаление наночастиц незначительно уменьшило углы смачивания и увеличило углы скатывания. Понижение связано с частичным удалением нанотекстуры поверхности при обработке в ультразвуковой ванне. Отметим, что при этом также был полностью удален оставшийся в порах декан и большая часть элементов текстуры со слабой адгезией к поверхности, что позволило добиться большей стойкости супергидрофобного состояния при контакте с водой и с парами воды. Стоит отметить, что у всех образцов, приготовленных по второму протоколу, получены близкие по значению углы смачивания и скатывания, что говорит о хорошей воспроизводимости используемого метода получения покрытий.
На рис. 3 представлено изменение угла смачивания, формируемого каплей воды, в зависимости от времени контакта с образцом в атмосфере, насыщенной парами воды. Синими квадратами показаны данные для образцов, приготовленных по второму протоколу, а красными кружками – для образцов, приготовленных без дополнительного удаления наночастиц. Из рисунка видно, что удаление наночастиц, слабо связанных с поверхностью и способных удаляться с нее каплей воды за счет капиллярных сил, позволяет добиться значительного повышения стойкости покрытия при контакте с водой по сравнению с образцами, приготовленными по первому протоколу. Угол на образцах, приготовленных по второму протоколу, практически не меняется в течение 24 ч. Угол смачивания на образцах, приготовленных без дополнительной очистки в ультразвуковой ванне от слабо связанных с поверхностью наночастиц, не меняется некоторое время. Однако, при контакте натекающего фронта капли со слабо связанными с поверхностью наночастицами происходит отрыв частиц капиллярными силами и формирование дефекта смачивания. Поскольку на образующемся дефекте смачивания отсутствует гидрофобизатор, взаимодействие воды с дефектом приводит к деградации поверхностного слоя и разрушению супергидрофобного состояния.
Рис. 3.
Изменение угла смачивания во времени для двух видов образцов (1 – образцы, у которых удалялись наночастицы с низкой адгезией к поверхности в ультразвуковой ванне, 2 – без удаления наночастиц). Разные линии с одинаковыми значками соответствуют разным образцам, изготовленным по соответствующему протоколу.
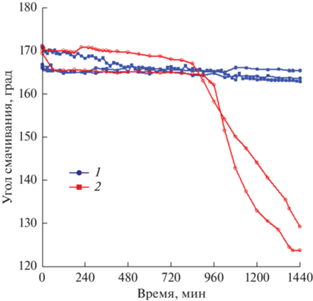
Проверка стойкости покрытия к контакту с парами воды также проводилась в двойной кювете для поддержания 100% влажности. Данные по изменению углов смачивания и скатывания при длительном контакте с парами для образцов, приготовленных по второму протоколу, представлены в табл. 5.
Таблица 5.
Значения углов смачивания и скатывания после контакта с парами воды
Время контакта с парами воды, ч | Угол смачивания, град | Угол скатывания, град |
---|---|---|
0 | 168.6 ± 0.5 | 3.6 ± 0.8 |
1 | 168.3 ± 0.6 | 5.0 ± 0.8 |
2 | 165.9 ± 0.5 | 6.1 ± 1.6 |
3 | 165.8 ± 0.9 | 7.1 ± 1.5 |
4 | 164.8 ± 0.8 | 7.3 ± 2.1 |
5 | 164.6 ± 0.7 | 7.8 ± 1.8 |
20 | 166.5 ± 0.5 | 9.8 ± 3.2 |
24 | 166.8 ± 1.0 | 10.0 ± 3.5 |
48 | 168.5 ± 0.9 | 11.9 ± 3.0 |
После выдержки при 105°С в течение 1 ч | 168.7 ± 1.0 | 5.2 ± 0.9 |
Из представленных в табл. 5 данных следует, что супергидрофобные свойства поверхности при кратковременном контакте с парами воды незначительно ухудшаются, однако более длительный контакт с парами сопровождается некоторым ростом угла смачивания с одновременным ростом и угла скатывания. Такое поведение углов скатывания можно рассматривать, как указание на формирование единичных дефектов смачивания, которые гидратируются при контакте с парами воды. В то же время восстановление угла смачивания при длительном контакте с парами требует дальнейших исследований. При этом, если образцы после длительного контакта с водой повторно выдержать при 105°С в течение 1 ч, то углы скатывания уменьшаются, указывая на удаление гидратной оболочки и взаимодействие силанольных групп соседних молекул гидрофобизатора с формированием силоксановой связи.
Кроме анализа химической стойкости супергидрофобной поверхности краски при контакте с водой и парами воды, мы также исследовали стойкость образцов к абразивным нагрузкам. Для этого был использован метод обработки образца в вибрирующем слое песка, используемый в стандарте ASTM F735 [37].
Время испытания составляло 20 мин. Каждые пять минут образец доставали, мыли в ультразвуковой ванне, чтобы удалить частицы песка, сушили в течение 15 мин на воздухе и измеряли углы смачивания и скатывания. В табл. 6 представлены значения улов смачивания и скатывания после абразивного воздействия различной длительности.
Таблица 6.
Углы смачивания и скатывания, измеренные после абразивного воздействия
Время воздействия | Угол смачивания, град | Угол скатывания, град |
---|---|---|
0 мин | 169.2 ± 0.6 | 4.5 ± 0.8 |
5 мин | 157.9 ± 2.3 | 22.5 ± 3.6 |
10 мин | 155.3 ± 2.1 | 25.1 ± 4.8 |
15 мин | 154.1 ± 3.4 | 25.8 ± 3.8 |
20 мин | 152.9 ± 3.6 | 27.2 ± 2.9 |
Заметное уменьшение углов смачивания связано с тем, что при интенсивном истирании поверхности песком, движущимся с высокой скоростью, частично удалялась нано- и микротекстура поверхности. Кроме того, возможно, частично удалялся и гидрофобизатор, который находился на элементах текстуры. В то же время следует отметить, что для интенсивного абразивного воздействия, которому подвергалось супергидрофобное покрытие в описанном выше испытании, наблюдается незначительное ухудшение супергидрофобного состояния. Чтобы проверить эти предположения, был выполнен элементный анализ поверхностного слоя до и после абразивной нагрузки, а также исследована морфология поверхности.
Особенностью исследуемого образца является то, что краска — это диэлектрик. В таком случае, при электронно-микроскопическом исследовании, происходит накопление отрицательного заряда в приповерхностной области, что приводит к искажению изображения, получаемого в сканирующем электронном микроскопе. Чтобы устранить влияние накопленного заряда, до исследования на поверхность образца наносилось токопроводящее углеродное покрытие толщиной порядка 20–30 нм. Анализ, выполненный с большой площади для усреднения случайных изменений, вызванных разными факторами (характерный размер участка ~200 × 200 мкм2), показывает, что в среднем состав поверхностного слоя до и после абразивных нагрузок практически не изменился.
Однако, после абразивной обработки на поверхности образца появляются места, на которых заметно уменьшение количества фтора, что связано, скорее всего, с частичным удалением гидрофобизатора. Этот факт проиллюстрирован на рис. 4, на котором приведены относительные интенсивности пиков фтора и кислорода. Характерный размер участков, от которых получены эти спектры, составляет ~10 × 10 мкм2. Участков, на которых фтор не определяется, что могло бы быть свидетельством полного удаления гидрофобизатора, не обнаружено. Скорее всего, это связано с тем, что фтор также входит в состав полимерного связующего, которое используется при приготовлении краски. Чтобы это проверить, был выполнен элементный анализ необработанной краски.
На рис. 5 представлены типичные спектры необработанного слоя краски. Элементный анализ выполнен с большой площади для усреднения случайных изменений, вызванных разными факторами.
Из представленных данных по составу краски можно сделать вывод, что необработанная краска действительно содержит фтор. Поэтому нельзя точно определить, удаляется ли при абразивной нагрузке гидрофобизатор полностью или частично.
По данным электронной микроскопии, главным отличием в текстуре образцов до и после абразивной обработки является появление большого числа достаточно плоских участков с характерным размером ~10 мкм. На этих участках многомодальная шероховатость выражена существенно меньше и именно на них наблюдается пониженное содержание фтора по сравнению с исходным образцом. На рис. 6 приведены типичные изображения при одинаковом увеличении до (слева) и после (справа) абразива.
Рис. 6.
Морфология поверхности (изображения супергидрофобного покрытия на поверхности краски до механических испытаний (a, в, д) и после испытания на абразивный износ (б, г, е)).
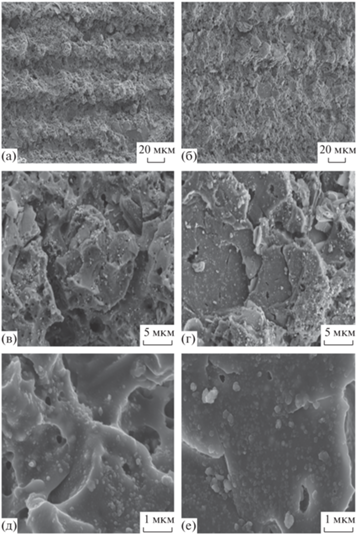
Кроме стойкости покрытия к различным нагрузкам было исследовано явление самоочистки супергидрофобного покрытия после приложения абразивной нагрузки в течение 20 мин. Образец помещали на наклонной поверхности с углом наклона 30 град и посыпали его тонким слоем красного перца. После этого капали на поверхность каплю воды объемом 15 мкл. Скатываясь, капля собирала весь перец, который находился у нее на пути. На рис. 7 представлен процесс очищения поверхности образца от перца каплей воды. Эти данные однозначно свидетельствуют о сохранении супергидрофобных свойств и свойств самоочистки нашего покрытия даже после приложения интенсивной абразивной нагрузки.
ВЫВОДЫ
В ходе данной работы использовали наносекундную лазерную обработку поверхности краски для придания ей многомодальной шероховатости, необходимой для достижения супергидрофобного состояния. Варьирование режимов лазерной обработки позволило получить морфологию поверхности, хемосорбция гидрофобного агента на которой приводит к получению максимальных значений углов смачивания (170.7 ± 0.7) и минимальных углов скатывания (4.0 ± 0.8). Кроме этого, были проведены испытания полученных супергидрофобных покрытий на стойкость к контакту с водой и парами воды, к абразивным нагрузкам. Полученные результаты показывают, что лазерная обработка краски в сочетании с гидрофобизацией фтороксисиланами позволяет получать покрытия с высокой стойкостью к типичным эксплуатационным нагрузкам.
Список литературы
Boinovich L.B., Gnedenkov S.V., Alpysbaeva D.A., Egorkin V.S., Emelyanenko A.M., Sinebryukhov S.L., Zaretskaya A.K. Corrosion resistance of composite coatings on low-carbon steel containing hydrophobic and superhydrophobic layers in combination with oxide sublayers // Corrosion science. 2012. V. 55. P. 238–245.
Delimi A., Galopin E., Coffinier Y., Pisarek M., Boukherroub R., Talhi B., Szunerits S. Investigation of the corrosion behavior of carbon steel coated with fluoropolymer thin films // Surface and Coatings Technology. 2011. V. 205. № 16. P. 4011–4017.
Ishizaki T., Masuda Y., Sakamoto M. Corrosion resistance and durability of superhydrophobic surface formed on magnesium alloy coated with nanostructured cerium oxide film and fluoroalkylsilane molecules in corrosive NaCl aqueous solution // Langmuir. 2011. V. 27. № 8. P. 4780–4788.
Selim M.S., El-Safty S.A., Fatthallah N.A., Shenashen M.A. Silicone/graphene oxide sheet-alumina nanorod ternary composite for superhydrophobic antifouling coating // Progress in Organic Coatings. 2018. V. 121. P. 160–172.
He X., Cao P., Tian F., Bai X., Yuan C. Autoclaving-induced in-situ grown hierarchical structures for construction of superhydrophobic surfaces: a new route to fabricate antifouling coatings // Surface and Coatings Technology. 2019. V. 357. P. 180–188.
Rasitha T.P., Vanithakumari S.C., Krishna D.N.G., George R.P., Srinivasan R., Philip J. Facile fabrication of robust superhydrophobic aluminum surfaces with enhanced corrosion protection and antifouling properties // Progress in Organic Coatings. 2022. V. 162. P. 106560.
Antonini C., Innocenti M., Horn T., Marengo M., Amirfazli A. Understanding the effect of superhydrophobic coatings on energy reduction in anti-icing systems // Cold Regions Science and Technology. 2011. V. 67. № 1–2. P. 58–67.
Бойнович Л.Б., Домантовский А.Г., Емельяненко А.М., Миллер А.Б., Потапов Ю.Ф., Ходан А.Н. Противообледенительные свойства супергидрофобных покрытий на алюминии и нержавеющей стали // Изв. АН. Сер. Хим. 2013. № 2. С. 383–390.
Lv L., Liu H., Zhang W., Chen J., Liu Z. Facile UV-curable fabrication of robust, anti-icing superhydrophobic coatings based on polyurethane // Materials Letters. 2020. V. 258. P. 126653.
Boinovich L.B., Emelyanenko A.M. The behaviour of fluoro- and hydrocarbon surfactants used for fabrication of superhydrophobic coatings at solid/water interface // Colloids and Surfaces A: Physicochemical and Engineering Aspects. 2015. V. 481. P. 167–175.
Boinovich L.B., Emelyanenko K.A., Domantovsky A.G., Emelyanenko A.M. Laser tailoring the surface chemistry and morphology for wear, scale and corrosion resistant superhydrophobic coatings // Langmuir. 2018. V. 34. № 24. P. 7059–7066.
Garcia-Giron A., Romano J.M., Batal A., Dashtbozorg B., Dong H., Solanas E.M., Dimov S.S. Durability and wear resistance of laser-textured hardened stainless steel surfaces with hydrophobic properties // Langmuir. 2019. V. 35. № 15. P. 5353–5363.
Sataeva N.E., Boinovich L.B., Emelyanenko K.A., Domantovsky A.G., Emelyanenko A.M. Laser-assisted processing of aluminum alloy for the fabrication of superhydrophobic coatings withstanding multiple degradation factors // Surface and Coatings Technology. 2020. V. 397. P. 125993.
Zhao G.C., Li J., Huang Y.F., Yang L.M., Ye Y., Walsh F.C., Chen J., Wang S.C., Robust Ni/WC superhydrophobic surfaces by electrodeposition // RSC Adv. 2017. № 7. 44896–44903.
Boinovich L., Emelyanenko A. The prediction of wettability of curved surfaces on the basis of the isotherms of the disjoining pressure // Colloids and Surfaces A: Physicochemical and Engineering Aspects. 2011. V. 383 (1–3), P. 10–16.
Woodward I., Schofield W.C.E., Roucoules V., Badyal J.P.S. Super-hydrophobic surfaces produced by plasma fluorination of polybutadiene films // Langmuir. 2003. V. 19. № 8. P. 3432–3438.
Tserepi A., Gogolides E., Tsougeni K., Constantoudis V., Valamontes E.S. Tailoring the surface topography and wetting properties of oxygen-plasma treated polydimethylsiloxane // Journal of Applied Physics. 2005. V. 98. № 11. P. 113502.
Nakajima A., Hashimoto K., Watanabe T., Takai K., Yamauchi, G., Fujishima A. Transparent superhydrophobic thin films with self-cleaning properties // Langmuir. 2000. V. 16. № 17. P. 7044–7047.
Ferrari M., Ravera F., Liggieri L. Preparation of a superhydrophobic surface by mixed inorganic-organic coating // Applied physics letters. 2006. V. 88. № 20. P. 203125.
Zhao Y., Lu Q., Chen D., Wei Y. Superhydrophobic modification of polyimide films based on gold-coated porous silver nanostructures and self-assembled monolayers // Journal of Materials Chemistry. 2006. V. 16. № 46. P. 4504–4509.
Емельяненко А.М., Домантовский А.Г., Емельяненко К.А., Бойнович Л.Б. Получение износостойких супергидрофобных покрытий с применением лазерного микро- и нанотекстурирования // Российские нанотехнологии. 2015. Т. 10. № 7–8. С. 62–68.
Boinovich L.B., Modin E.B., Sayfutdinova A.R., Emelyanenko K.A., Vasiliev A.L., Emelyanenko A.M. Combination of functional nanoengineering and nanosecond laser texturing for design of superhydrophobic aluminum alloy with exceptional mechanical and chemical properties // ACS nano. 2017. V. 11. № 10. P. 10113–10123.
Latthe S.S., Sutar R.S., Kodag V.S., Bhosale A.K., Kumar A.M., Sadasivuni K.K., Liu S. Self-cleaning superhydrophobic coatings: potential industrial applications // Progress in Organic Coatings. 2019. V. 128. P. 52–58.
Ijaola A.O., Farayibi P.K., Asmatulu E. Superhydrophobic coatings for steel pipeline protection in oil and gas industries: a comprehensive review // Journal of Natural Gas Science and Engineering. 2020. V. 83. P. 103544.
Rao A.V., Latthe S.S., Mahadik S.A., Kappenstein C. Mechanically stable and corrosion resistant superhydrophobic sol–gel coatings on copper substrate // Applied Surface Science. 2011. V. 257. № 13. P. 5772–5776.
Zhang F., Chen S., Dong L., Lei Y., Liu T., Yin Y. Preparation of superhydrophobic films on titanium as effective corrosion barriers // Applied Surface Science. 2011. V. 257. № 7. P. 2587–2591.
Terpilowski K., Goncharuk O., Gun’ko V.M. Macro and micro wettability of hydrophobic siloxane films with hierarchical surface roughness // Smart Materials and Structures. 2018. V. 27. № 7. P. 075002.
Kravets L.I., Yarmolenko M.A., Rogachev A.A., Gainutdinov R.V., Gilman A.B., Altynov V.A., Lizunov N.E. Formation of Superhydrophobic Coatings on the track-etched membrane surface by the method of electron-beam deposition of polymers in vacuum // Inorganic Materials: Applied Research. 2020. V. 11. № 2. P. 476–487.
Wen G., Guo Z. G., Liu W. Biomimetic polymeric superhydrophobic surfaces and nanostructures: from fabrication to applications // Nanoscale. 2017. V. 9. № 10. P. 3338–3366.
Das S., Kumar S., Samal S.K., Mohanty S. and Nayak S.K. A review on superhydrophobic polymer nanocoatings: recent development and applications // Industrial & Engineering Chemistry Research. 2018. V. 57. № 8. P. 2727–2745.
Martinez-Calderon M., Haase T.A., Novikova N.I., Wells F.S., Low J., Willmott G.R., Aguergaray C. Turning industrial paints superhydrophobic via femtosecond laser surface hierarchical structuring // Progress in Organic Coatings. 2022. V. 163. P. 106625.
Меркулова Ю.И., Кузнецова В.А., Сердцелюбова А.С. Лакокрасочные покрытия для защиты полимерных композиционных материалов // Полимерные композиционные материалы нового поколения и технологии их переработки. 2020. С. 48–55.
Fridman A. Plasma chemistry. Cambridge university press, 2008.
Sanchis M.R., Calvo O., Fenollar O., Garcia D., Balart R. Surface modification of a polyurethane film by low pressure glow discharge oxygen plasma treatment, . Journal of Applied Polymer Science. 2007. V. 105(3). P. 1077−1085.
Genzer J., Efimenko K. Creating long-lived superhydrophobic polymer surfaces through mechanically assembled monolayers // Science. 2000. V. 290. № 5499. P. 2130–2133.
Fadeev A.Y., McCarthy T.J. Self-assembly is not the only reaction possible between alkyltrichlorosilanes and surfaces: monomolecular and oligomeric covalently attached layers of dichloro-and trichloroalkylsilanes on silicon // Langmuir. 2000. V. 16. № 18. P. 7268–7274.
ASTM F735-17 Standard Test Method for Abrasion Resistance of Transparent Plastics and Coatings Using the Oscillating Sand Method; ASTM International: West Conshohocken, PA, USA, 2017.
Guenther K.H., Kaminski L.R. Abrasion Testing of Vacuum Coated Plastic Lenses // Ophthalmic Optics. International Society for Optics and Photonics.1986. V. 601. P. 69–75.
Бойнович Л.Б., Емельяненко А.М. Автоматизированная установка для измерения поверхностного натяжения жидкостей и краевых углов смачивания // Приборы и техника эксперимента. 2002. № 2. С. 167.
Boinovich L., Emelyanenko A. A wetting experiment as a tool to study the physicochemical processes accompanying the contact of hydrophobic and superhydrophobic materials with aqueous media // Advances in Colloid and Interface Science. 2012. V. 179. P. 133–141.
Бойнович Л.Б., Емельяненко А.М. Гидрофобные материалы и покрытия: принципы создания, свойства и применение // Успехи химии. 2008. Т. 77. № 7. С. 619–638.
Дополнительные материалы отсутствуют.
Инструменты
Коллоидный журнал