Химия твердого топлива, 2020, № 4, стр. 28-33
ПРИМЕНЕНИЕ НАНОГЕТЕРОГЕННЫХ МОЛИБДЕНСУЛЬФИДНЫХ КАТАЛИЗАТОРОВ ПРИ ГИДРООБЛАГОРАЖИВАНИИ СМОЛЫ ПОЛУКОКСОВАНИЯ УГЛЯ МЕСТОРОЖДЕНИЯ ШУБАРКУЛЬ
Н. Т. Смагулова 1, 2, *, Ж. К. Каирбеков 1, **, А. С. Малолетнев 3, Л. К. Кудреева 1, 2, А. Н. Сабитова 1, 2
1 РГП Казахский национальный университет имени аль-Фараби
050040 Алматы, Республика Казахстан
2 ДГП НИИ новых химических технологий и материалов
050012 Алматы, Республика Казахстан
3 Горный институт НИТУ МИСиС
119049 Москва, Россия
* E-mail: nazym2011@inbox.ru
** E-mail: zh_kairbekov@gmail.com
Поступила в редакцию 27.11.2019
После доработки 31.01.2020
Принята к публикации 30.03.2020
Аннотация
Для интенсификации технологии переработки каменноугольной смолы полукоксования угля месторождения Шубаркуль (Республика Казахстан) выполнено исследование по ее гидрооблагораживанию в присутствии наногетерогенных молибденсульфидных каталитических систем (содержание Мо 0.025–0.12%), полученных in situ в каменноугольной смоле с добавками сульфидирующего агента – элементной серы в количестве 0.03–0.09 мас. % на сырье. Установлено, что эффективное содержание Мо в катализаторе составляет 0.025%, а количество серы – 0.03%, что позволяет при 5 МПа и 400°С получить максимальный выход суммарных жидких продуктов (76.8%), которые содержат преимущественно дизельные фракции.
ВВЕДЕНИЕ
Одним из основных недостатков современных технологий каталитической гидрогенизации высокомолекулярного углеводородного сырья является применение гетерогенных катализаторов, которым присущи определенные проблемы, связанные с их дезактивацией под влиянием реакционной среды, сопровождающейся изменением текстуры катализатора, адсорбцией на их поверхности продуктов реакции и уменьшением доли активной поверхности, ее зауглероживанием, потерей механической прочности и др. В большинстве случаев вследствие сложности регенерации гетерогенных катализаторов срок их службы существенно сокращается.
В опубликованной литературе отмечается, что для переработки углей и тяжелых видов углеводородного сырья (угольных дистиллятов, тяжелых нефтей, битумов и нефтяных остатков) более эффективны катализаторы, вносимые в технологический процесс в форме высокодисперсных частиц, равномерно распределенных в объеме сырья [1, 2]. С точки зрения эффективности диспергирования в сырье наиболее перспективны наногетерогенные катализаторы, получаемые in situ из прекурсоров в реакционной среде [3].
В качестве прекурсоров могут использоваться водо- [2, 4] и маслорастворимые [5] соединения переходных металлов. Чаще всего применяются монометаллические молибден- или вольфрамсодержащие прекурсоры, формирующие в углеводородной среде в присутствии сульфидирующего агента соответственно MoS2 или WS2.
Гидрооблагораживание высокоароматических фракций и остатков в присутствии дисульфида молибдена, синтезированного in situ из водных растворов прекурсора, достаточно широко исследовано. Получены обширные данные о морфологии катализатора, возможностях его промотирования, оптимизирован состав эмульсий и т.д. [6–8].
В работе [9] были получены NoMoS- и CoMoS-катализаторы in situ в углеводородном сырье путем разложения биметаллических водорастворимых прекурсоров, каталитические свойства которых исследованы в реакциях гидрирования и гидрообессеривания модельных соединений. Модельное сырье представляло собой 10%-ные растворы бициклических ароматических углеводородов (БЦА) в н-гексадекане и 5%-ный раствор дибензотиофена (ДБТ) в бензоле. Установлено, что оптимальное соотношение в катализаторе промотор:молибден составляло 0.25:1 и исследованные катализаторы проявили высокую активность в реакциях гидрирования и гидрообессеривания, в том числе при рециркуляции сырья.
На примере процесса гидрогенизации угля было показано [9], что биметаллический Со/Мо-содержащий прекурсор (Мо2Со2S4Cp2(CO)2, где Ср – циклопентадиен) обеспечивает большую конверсию, чем смесь карбонилов молибдена и кобальта.
Отмечается [10], что модифицирование наногетерогенных Fe-содержащих катализаторов добавками элементной серы (0.75–1.25% от массы катализатора) позволяет при гидрогенизации угля увеличить выход суммарных жидких продуктов до 62.3–67.3% по сравнению с осуществлением процесса в присутствии немодифицированных катализаторов.
Наряду с применением наногетерогенных катализаторов in situ в нефтяном или угольном пастообразователе процесс гидрогенизации углей можно интенсифицировать предварительным озонированием сырья. Авторами [10] установлена положительная роль предварительного озонирования угля, которое позволяет при гидрогенизации увеличить выход суммарных жидких продуктов на 13.3% по сравнению с выходом жидких продуктов при использовании необработанного озоном угля. В работе [11] определено, что предварительное озонирование в течение 60 мин позволяет при последующей каталитической гидрогенизационной переработке каменноугольной смолы (5 МПа, 450°С, наногетерогенный Мо-содержащий катализатор in situ в нефтяном пастообразователе) увеличить выход суммарных жидких продуктов на 44.8% и на 17.7% выход фракции с т. кип. до 180°С по сравнению с их содержанием в исходной смоле.
В статье исследованы каталитические свойства ненанесенных молибден-сульфидных катализаторов в реакциях гидрирования и гидрообессеривания каменноугольной смолы полукоксования угля Шубаркульского месторождения с получением данных, необходимых для интенсификации технологии переработки смолы в сырье для получения игольчатого кокса, бессернистого нафталина, высокочистого бензола для органического синтеза и других химических продуктов с использованием процесса гидрогенизации.
ЭКСПЕРИМЕНТАЛЬНАЯ ЧАСТЬ
В качестве исходного сырья использовали смолу без предварительного обезвоживания (содержание воды 3.4%) и дистилляции в смеси с приготовленным катализатором и остатком дистилляции с т. кип. выше 320°С нефти месторождения Кумколь (Республика Казахстан), взятых в соотношении 1 : 1. Характеристика смолы приведена в табл. 1, нефтяной остаток имел следующие характеристики: плотность при 20°С 0.8077 г/см3; вязкость 9.69 мм2/с; содержание, мас. %: парафины 14.73; асфальтены 1.52; смолы 8.2; элементный состав, мас. %: С 83.85; H 11.27; S 1.81; N 0.80; О 2.27.
Таблица 1.
Характеристика смолы полукоксования угля месторождения Шубаркуль
Показатель | Значение показателя |
---|---|
Содержание воды, % | 3.4 |
Плотность при 20°C, г/см3 | 1.071 |
Зольность, % | 0.11 |
Фракционный состав, мас. %: | |
н. кип., °С | 112–120 |
выкипает до 180°С | 2.4 |
180–330°С | 19.0 |
выше 330°С + потери | 78.6 |
Содержание, мас. %: | |
полиароматические углеводороды | 60.0 |
вещества, не растворимые в толуоле | 1.3 |
вещества, не растворимые в хинолине | 0.2 |
Температура вспышки в закрытом тигле, °С | 121 |
Коксуемость по Конрадсону, % | 2.3–3.5 |
Массовая доля серы, % | 0.35 |
Содержание фактических смол + асфальтены, % | 27.0 |
Приготовление катализатора осуществляли добавлением в смолу водного раствора парамолибдата аммония (3.0 мас. % от сырья), а также сульфидирующей добавки элементной серы (в порошкообразном виде) в количестве 0.03–0.09% от массы катализатора и диспергированием полученной смеси в гомогенизаторе при температуре 130°С и скорости вращения пластин 1500 об./мин. Концентрация металла составляла 0.025, 0.05 и 0.12% в расчете на сырье.
Опыты проводили в условиях лабораторной установки высокого давления с пустотелым реактором объемом 0.25 дм3 и перемешивающим устройством. Смесь cмолы с катализатором и добавкой серы, нагретую до 70–80°С, загружали в реактор, который предварительно продували аргоном и заполняли водородом при начальном давлении 2–3 МПа. Включали обогрев реактора, а при достижении 150°С перемешивающее устройство. Температуру замеряли термопарой и автоматически поддерживали с точностью ±2°C. Рабочее давление водорода составляло 5.0 МПа, температура 350–450°С, время реакции 15 мин. Давление водорода 5.0 МПа было выбрано в качестве эффективного на основании экспериментальных данных [11] и результатов, полученных в [12, 13].
Групповой углеводородный состав полученных дистиллятных фракций смолы определяли на хроматографе “ХРОМАТЭК” (Германия), содержание серы – на приборе “POST LEKI P1437” (Германия) методом энергодисперсионной рентгенофлуоресцентной спектрометрии. ИК-спектры получали на ИК-спектрометре SPECTRUM-65 фирмы “PERKIN ELMER” при частотах 4000–450 см–1. Фазовый состав твердых продуктов оценивали методом РФА на приборе ДРОН-2. Форму и размеры твердых частиц определяли по фотоснимкам, полученным на сканирующем электронном микроскопе HITACHI S-4800.
РЕЗУЛЬТАТЫ И ОБСУЖДЕНИЕ
Результаты гидрогенизации смолы приведены в табл. 2, из которой видно, что при температуре 400°С в присутствии катализатора, содержащего 0.025% Mo и 0.03% добавок серы, суммарный выход дистиллятных фракций составляет 76.8%, в том числе 75.1% дизельной фракции, что существенно выше 65.1 и 50.4% при осуществлении процесса в присутствии катализатора 0.05% Мо + + 0.06% S и 57.9 и 48.6% – при использовании катализатора 0.12% Мо + 0.09% S соответственно. Увеличение добавок серы с 0.03 до 0.09% и повышение температуры процесса до 450°С приводят к снижению суммарного выхода жидких продуктов и дизельной фракции и к увеличению образования газа и воды.
Таблица 2.
Результаты гидрогенизации смолы (5 МПа, τ = 15 мин, смола:нефтяной пастообразователь = 1:1, лабораторная установка высокого давления)
Добавка серы, % от массы катализатора | Темпе-ратура, °С | Выход жидких продуктов с т. кип., °С | Суммарный выход дистиллятной фракции, % | Газ + Н2О, мас. % | Шлам, мас. % | Потери, мас. % | ||
---|---|---|---|---|---|---|---|---|
до 180 | 180–250 | 250–320 | ||||||
Без катализатора и добавок серы | 350 | 5.3 | 11.4 | 13.2 | 29.9 | 36.0 | 16.2 | 17.9 |
400 | 7.8 | 15.3 | 24.0 | 47.1 | 36.3 | 9.1 | 7.5 | |
450 | 10.3 | 7.6 | 12.9 | 30.8 | 36.0 | 19.3 | 13.9 | |
В присутствии наногетерогенного дисульфида молибдена | ||||||||
0.025% Mo + 0.03% S | 350 | 1.3 | 15.2 | 42.0 | 58.5 | 22.8 | 14.5 | 4.2 |
400 | 1.7 | 22.8 | 52.3 | 76.8 | 8.2 | 9.2 | 5.8 | |
450 | 1.2 | 11.5 | 38.8 | 51.5 | 26.4 | 14.2 | 7.9 | |
0.05% Мо + 0.06% S | 350 | 4.2 | 6.4 | 23.3 | 33.9 | 34.9 | 14.6 | 16.6 |
400 | 14.7 | 18.7 | 31.7 | 65.1 | 10.7 | 18.5 | 5.7 | |
450 | 10.3 | 7.6 | 13.7 | 31.6 | 37.4 | 17.4 | 13.6 | |
0.12% Mo + 0.09% S | 350 | 4.2 | 6.4 | 23.2 | 33.8 | 40.0 | 17.8 | 8.4 |
400 | 9.3 | 14.0 | 34.6 | 57.9 | 22.1 | 10.6 | 9.4 | |
450 | 5.3 | 7.1 | 12.6 | 25.0 | 45.0 | 18.9 | 11.1 |
Установлено, что эффективное содержание Мо в катализаторе составляет 0.025%, а количество сульфидирующей добавки серы – 0.03%, что позволяет при 5 МПа и 400°С получить максимальный суммарный выход легких и средних дистиллятов (76.8%) по сравнению с их содержанием в исходной смоле (21.4%) и при других исследованных технологических параметрах осуществления процесса. Образующиеся смоляные дистилляты содержат преимущественно дизельные фракции (75.1%).
Химический состав смоляных дистиллятов приведен в табл. 3, из которой видно, что для получения компонентов моторных топлив со свойствами, отвечающими требованиям современных стандартов, смоляной бензин должен подвергаться гидроочистке и платформингу для крупномасштабного производства и цеоформингу – на малогабаритных установках. Дизельные фракции должны подвергаться гидрооблагораживанию и деароматизации.
Таблица 3.
Химический состав дистиллятных фракций, полученных гидрогенизацией смолы (5 МПа, 400°С, τ = 15 мин, лабораторная установка высокого давления)
Показатель | Дистиллятная фракция с т. кип., °С | ||
---|---|---|---|
80–180 | 180–250 | 250–320 | |
Без катализатора | |||
Плотность при 20°С, г/см3 | 1.0106 | 1.0812 | 1.2350 |
Йодное число, г J2/на 100 г продукта | 43.50 | 42.35 | 40.47 |
Групповой углеводородный состав, мас. %: | |||
н-парафины | 55.40 | 16.02 | 16.42 |
изопарафины | 10.14 | 14.65 | 13.75 |
ароматические углеводороды | 17.20 | 55.40 | 56.41 |
нафтены | 14.48 | 10.85 | 11.98 |
олефины | 2.30 | 3.08 | 1.44 |
циклоолефины | 0.48 | – | – |
Содержания серы, мас.% | 0.07 | 0.09 | 0.11 |
В присутствии Мо-катализатора (0.025% Мо + 0.03% S) | |||
Плотность при 20 °С, г/см3 | 0.9013 | 1.0004 | 1.1206 |
Йодное число, г J2/на 100 г продукта | 38.42 | 36.57 | 32.51 |
Групповой углеводородный состав, мас. %: | |||
н-парафины | 51.54 | 25.73 | 21.61 |
изопарафины | 8.67 | 26.23 | 24.62 |
ароматические углеводороды | 22.95 | 28.37 | 38.40 |
нафтены | 14.04 | 18.25 | 14.23 |
олефины | 1.28 | 1.42 | 1.14 |
Содержание серы, мас.% | 0.01 | 0.03 | 0.08 |
Фазовый состав твердых продуктов, полученных в процессе гидрооблагораживания смолы, определяли методом РФА. На дифрактограмме (рис. 1) видно, что при проведении процесса с добавлением серы появляется пик 6.08 град, который свидетельствует об образовании гексагонального MoS2, фазы, состоящей из кристаллитов размером 50–70 Å. При проведении процесса без добавления серы на дифрактограмме присутствуют фазы МоО2 и МоS2. По-видимому, в этом случае МоS2 образуется вследствие сульфидирования Мо серой, содержащейся в смоле.
Рис. 1.
Дифрактограмма кристаллической фазы дисульфида молибдена при осуществлении гидрооблагораживания смолы: без добавления в процесс серы (а); с добавлением 0.03% серы (б).
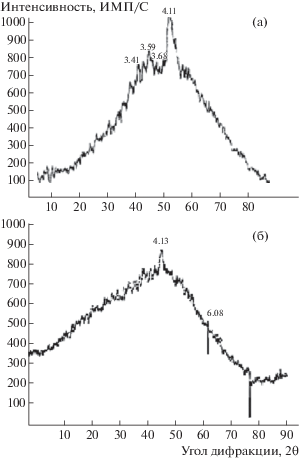
На фотоснимках, полученных с помощью СЭМ (рис. 2), отчетливо видно, что образовавшийся MoS2 представляет собой суспензию мелкодисперсных сферических частиц низкой степени кристалличности диаметром 500 и 1000 нм (0.5–1.0 мкм). Следует отметить, что образование каталитически активной фазы низкой кристалличности способствует высокой поверхностной концентрации активных центров катализатора, а сферическая форма частиц (глобул) дисульфида молибдена делает поверхность катализатора стерически доступной для гидрирования высокомолекулярных компонентов смолы, что позволяет проводить процесс гидрооблагораживания смолы в присутствии микроколичеств катализатора, составляющих от 0.02 до 0.05% металла в расчете на сырье.
Рис. 2.
Электронно-микроскопические снимки формирования в каменноугольной смоле частиц (глобул) MoS2 с диаметрами: 500 нм (а); 1000 нм (б).
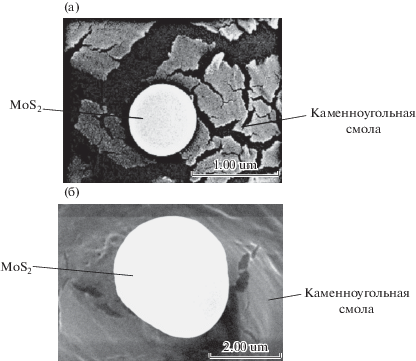
Таким образом, на основании результатов проведенного экспериментального исследования можно сделать вывод о том, что гидрооблагораживание каменноугольной смолы в присутствии наногетерогенного дисульфида молибдена осуществляется достаточно эффективно и позволяет при 5 МПа и 400°С получить максимальный выход дистиллятных продуктов (76.8%) по сравнению с их содержанием в исходной смоле (21.4%), которые можно использовать для получения игольчатого кокса, бессернистого нафталина, высокочистого бензола для органического синтеза и других химических продуктов с применением процесса гидрогенизации.
Список литературы
Кричко А.А., Озеренко А.А., Фросин С.Б., Зекель Л.А., Малолетнев А.С. // Катализ в промышленности. 2007. № 2. С. 30.
Зекель Л.А., Краснобаева Н.В., Кадиев Х.М., Хаджиев С.Н., Шпирт М.Я. // ХТТ. 2010. № 6. С. 22.
Хаджиев С.Н. // Нефтехимия. 2011. Т. 51. № 1. С. 3.
Ortiz-Moreno H., Ramires J., Cuevas R., Marroquin G., Ancheyta J. // Fuel. 2012. V. 100. P. 186.
Сизова И.А., Куликова А.Б., Онищенко М.И., Сердюков С.И., Максимов А.Л. // Нефтехимия. 2016. Т. 56. № 1. С. 52.
Song C., Saini A.K., Schobert H.H. // Proc. 8th Int. Conf. on Coal Sci. and Techn. (ICCS’8). Oviedo, Spain: Elsevier Sci. Publ., 1995. P. 1215.
Song C., Saini A.K., Schobert H.H. // Proc. 9th Int. Conf. on Coal Sci. and Techn. (ICCS’9). Essen, Germany: Elsevier Sci. Publ., 1997. P. 1397.
Pereira-Almao P., Scott Carlos E., Carbognani-Ortega L. // Advanced catalytic materials: current status and future progress. Switzerland: Springer Nature Switzerland AG, 2019. P. 129.
Петрухина Н.Н., Сизова И.А., Максимов А.Л. // Катализ в промышленности. 2017. Т. 17. № 2. С. 112.
Chunshan Song, Parfitt D.S., Schobert H.H. // Energy & Fuels. 1994. V. 8. P. 313.
Kairbekov Zh.K., Maloletnev A.S., Smagulova N.T., Sabitova A.N. // Solid Fuel Chemistry. 2018. V. 52. № 5. P. 320. https://doi.org/10.3103/S0361521918030047
Рохина Е.Ф., Шевченко Г.Г., Рохин А.В., Латышев В.П. // Рос. конф. (с межд. участием) “Глубокая переработка твердого ископаемого топлива – стратегия России в XXI веке”. Тез. докл., Звенигород.: Изд-во. МГУИЭ, 2007. С. 72.
Кричко А.А., Озеренко А.А., Малолетнев А.С., Зекель Л.А., Фросин С.Б., Шпирт М.Я. // Катализ в промышленности. 2007. № 3. С. 23.
Дополнительные материалы отсутствуют.
Инструменты
Химия твердого топлива