Химия твердого топлива, 2020, № 1, стр. 26-29
ИССЛЕДОВАНИЕ ПЕКА И КОКСА, ПОЛУЧЕННЫХ ИЗ СМОЛЫ ПОЛУКОКСОВАНИЯ ВЫСОКОСЕРНИСТЫХ ГОРЮЧИХ СЛАНЦЕВ ВОЛЖСКОГО БАССЕЙНА
А. Л. Лапидус 1, 2, *, Н. Ю. Бейлина 3, **, Д. С. Худяков 1, ***, Ф. Г. Жагфаров 1, ****
1 ФГАОУ ВО РГУ нефти и газа (НИУ) имени И.М. Губкина
119991 Москва, Россия
2 ФГБУН Институт органической химии имени Н.Д. Зелинского РАН
119991 Москва, Россия
3 АО Научно-исследовательский институт конструкционных материалов на основе графита “НИИграфит”
111524 Москва, Россия
* E-mail: albert@ioc.ac.ru
** E-mail: beilinan@mail.ru
*** E-mail: ltybc672@rambler.ru
**** E-mail: firdaus_jak@mail.ru
Поступила в редакцию 01.04.2019
После доработки 02.09.2019
Принята к публикации 04.10.2019
Аннотация
Представлены результаты исследования тяжелого остатка после ректификации сланцевой смолы полукоксования Перелюбского месторождения (пека) и полученного из него кокса.
Сланцевая смола была получена в процессе термического разложения горючего сланца Перелюбского месторождения без доступа воздуха в реакторе производительностью 8 кг/ч сухого измельченного горючего сланца при температуре 560°С, скорости продвижения горючего сланца 23.5 см/мин в течение 7 мин и разделена на две части простым отстаиванием. Верхняя (более легкая) часть смолы была разделена на фракции в аппарате ректификации нефти АРН-2. Из смолы от начала кипения до 410°С с интервалом в 20°С выделены 17 фракций, доля остатка после ректификации в сумме с потерями составила 29.3 мас. %.
Дальнейшая работа проводилась с остатком после вакуумной перегонки на аппарате АРН-2 в количестве 381.65 г.
Для сланцевого пека были определены зольность, выход летучих веществ, доля веществ, нерастворимых в толуоле, и температура размягчения по методу “Кольцо и стержень” ГОСТ 9950-83 (табл. 1). Первые три показателя были получены в соответствии с ГОСТ [1–3].
Таблица 1.
Показатели сланцевого пека после ректификации сланцевой смолы полукоксования Перелюбского месторождения
Показатель | Значение показателя |
---|---|
Зольность, % | 0.1150 |
Выход летучих веществ, % | 83.7300 |
Доля веществ нерастворимых в толуоле, % | 0.6100 |
Температура размягчения, °С | 55.5 |
Полученный пек по температуре размягчения можно отнести к «мягким пекам». Для пека характерно очень низкое содержание α-фракции (нерастворимых в толуоле веществ) и низкая зольность.
Для определения параметров термического разложения продукта был проведен дериватографический анализ исследуемого образца в среде гелия со скоростью подъема температуры 10 град/мин. Дериватограмма представлена на рис. 1.
Рис. 1.
Дериватограмма сланцевого пека. Потеря массы, мас. %: 1 – 0.7, 2 – 70.9, 3 – 81.4; температура, °С: 1 ' – 255, 2 ' – 520, 3 ' – 800.
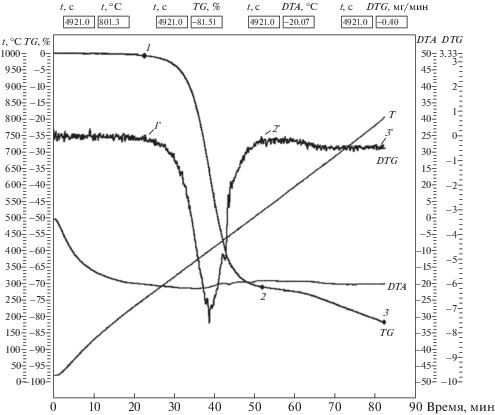
Основной интервал термического разложения пека находился в области 255–520°С. До температуры 255°С потеря массы равна 0.7%, при 520°С – 70.9%, после окончания нагрева (при температуре 800°С) – 81.4%. Экспериментально показано, что полученный из сланцевой смолы при вакуумной дистилляции пек отличается низкой термической стойкостью, высоким выходом летучих продуктов, а выход коксового остатка из него в условиях высокой скорости подъема температуры не превышает 17 мас. %.
Коксование сланцевого пека проводилось методом дистилляции в кубовой установке без доступа воздуха в замедленном режиме подъема температуры в течение 5 ч, показатели температуры регистрировались каждые 10 мин. Конечная температура коксования – 900°C. После окончания опыта куб охлаждали в течение 24 ч. Материальный баланс процесса коксования представлен в табл. 2, а режим проведения процесса коксования – на рис. 2.
Таблица 2.
Материальный баланс процесса коксования
Показатель | Масса, г | % |
---|---|---|
Взято: | ||
Сланцевый пек | 208.4 | 100 |
Итого: | 208.4 | 100 |
Получено: | ||
Газ | 66.9 | 32.1 |
Конденсат | 65.1 | 31.2 |
Кокс | 76.4 | 36.7 |
Итого: | 208.4 | 100 |
Показано, что в выбранном режиме процесса коксования удается повысить выход кокса в 2 раза по сравнению с выходом кокса, полученным в режиме дифференциального термического анализа.
Для кокса, полученного из сланцевого пека, были определены зольность и выход летучих веществ (табл. 3). В табл. 4 приведены экспериментальные данные элементного анализа сланцевого пека и кокса, полученного на его основе.
Таблица 3.
Показатели кокса, полученного из сланцевого пека, %
Показатель | Значение показателя |
---|---|
Зольность | 0.5000 |
Выход летучих веществ | 1.0500 |
Таблица 4.
Элементный состав сланцевого пека и кокса, полученного на его основе, мас. %
Образец | N | C | H | S |
---|---|---|---|---|
Сланцевый пек | 1.00 ± 0.02 | 80.70 ± 0.05 | 7.80 ± 0.05 | 6.90 |
Кокс (T = 900°С) | 1.26 ± 0.02 | 93.90 ± 0.05 | 0.47 ± 0.01 | 2.71 |
Обращает внимание существенное снижение сернистости кокса по сравнению с содержанием серы в пеке.
В ходе эксперимента определялась плотность сланцевого пека и кокса, полученного на его основе в соответствии с [4] (табл. 5).
Таблица 5.
Значения плотности для кокса и для пека
Образец | Действительная плотность, г/см3 |
---|---|
Сланцевый пек | 1.14 |
Кокс (T = 900°C) | 1.83 |
Кокс (T = 1300°C) | 2.03 |
Была определена микроструктура полученного кокса в соответствии с ГОСТ 26132-84. Для проведения анализа из представительной пробы было отобрано 7 г кокса с размером частиц 2–4 мм и изготовлено два шлиф-брикета. Далее с использованием светового металлографического микроскопа проводилась оценка структуры приготовленного из кокса шлифа методом сравнения структуры в поле зрения микроскопа с эталонами, приведенными в приложении к стандарту ГОСТ 26132-84 [5]. Всего для каждого шлифа проанализировано 30 полей зрения. Диаграмма по оценке микроструктуры представлена на рис. 3, микроструктура характерного участка шлифа в поле зрения микроскопа – на рис. 4.
По распределению структурных составляющих видно, что полученный кокс имеет однородную изотропную структуру. Превалирующая часть структурных составляющих (95%) характеризуется, согласно ГОСТ 26132-84, как “весьма мелковолокнистая, с существованием границ между структурными элементами”, с размером волокон 3–10 мкм, т.е. оцениваемая баллом 2.0.
ОБСУЖДЕНИЕ РЕЗУЛЬТАТОВ
В результате проведенных исследований из сланцевой смолы полукоксования методом вакуумной дистилляции получен пек. Определены следующие характеристики пека: зольность 0.115%, выход летучих 83.73%, температура размягчения 56°C, выход веществ, нерастворимых в толуоле, 0.61%. Полученный пек можно отнести к мягким. Данный образец не соответствует требованиям, предъявляемым к среднетемпературному каменноугольному электродному пеку, указанным в [6]. Пек, полученный из сланцевой смолы, не может использоваться в качестве связующего или пропиточного материала в электродной или алюминиевой промышленности в связи с высоким содержанием в нем серы. Для получения из него кондиционного пека требуется гидроочистка исходной смолы или самого мягкого пека и дальнейшее его окисление с целью повышения в нем коксообразующей составляющей – α-фракции, и выхода кокса.
Кокс, полученный на основе сланцевого пека, обладает изотропной структурой (чего не было получено ранее из прямогонной смолы горючих сланцев) и имеет зольность 0.5%, выход летучих 1.05%, плотность при 900°C 1.83 г/см3, плотность при 1300°C 2.03 г/см3, средний балл микроструктуры 2. Выход кокса составил 36.7% в расчете на исходный пек. Данные показатели зольности и выхода летучих веществ удовлетворяют требованиям, предъявляемым к коксам нефтяным и пековым, указанным в [7]. Однако из-за высокого содержания серы (2.7 мас. %) применение такого кокса в промышленном масштабе возможно при производстве анодных масс и обожженных анодов в алюминиевой промышленности, но нецелесообразно при получении конструкционного графита. Кокс можно использовать для изготовления конструкционных графитов при условии предварительной очистки от сернистых соединений пека, подвергаемого коксованию.
Содержание серы в коксе можно снизить применив к исходной смоле гидроочистку, но возможен и вариант замедленного коксования, при котором в исходный пек добавляется 5–10 мас. % тонко измельченного кокса [8]. В результате коксования содержание серы в коксе уменьшается, а структура остается изотропной.
Таким образом, из приведенных данных видно, что на основе прямогонной сланцевой смолы, полученной в процессе переработки горючих сланцев Перелюбского месторождения, можно получить мягкий пек и кокс изотропной структуры, которые целесообразно использовать при производстве анодных материалов алюминиевой индустрии.
Список литературы
ГОСТ 7846-73. Пек каменноугольный. Метод определения зольности. Введ. 01.01.75. М.: Изд-во стандартов, 2001. 5 с.
ГОСТ 9951-73. Пек каменноугольный. Метод определения выхода летучих веществ. Введ. 01.01.75. М.: Изд-во стандартов, 1998. 8 с.
ГОСТ 7847-73. Пек каменноугольный. Метод определения массовой доли веществ, нерастворимых в толуоле. Введ. 01.01.75. М.: Изд-во стандартов, 1997. 9 с.
ГОСТ 10220-82. Кокс каменноугольный. Метод определения плотности и пористости. Введ. 24.01.1982. М.: Государственный комитет по стандартам, 1982. 10 с.
ГОСТ 26132-84. Коксы нефтяные и пековые. Метод оценки микроструктуры. Введ. 07.01.85. М.: Изд-во стандартов, 2006. 20 с.
ГОСТ 10200-83. Пек каменноугольный электродный. Введ. 07.08.99. М.: Изд-во стандартов, 2005. 12 с.
ГОСТ 22898-78. Коксы нефтяные и пековые. Технические условия. Введ. 01.01.79. М.: Изд-во стандартов, 1995. 24 с.
Бейлина Н.Ю., Петров А.В. // Изв. ВУЗов. Сер. Химия и химическая технология. 2011. Т. 54 (7). С. 95.
Дополнительные материалы отсутствуют.
Инструменты
Химия твердого топлива