Химия твердого топлива, 2023, № 5, стр. 55-68
ИНТЕНСИФИКАЦИЯ ПРОЦЕССА ВОСПЛАМЕНЕНИЯ КАМЕННОГО УГЛЯ ПУТЕМ ДОБАВЛЕНИЯ БИОМАССЫ В УСЛОВИЯХ ФАКЕЛЬНОГО СЖИГАНИЯ
А. В. Жуйков 1, 2, *, Д. О. Глушков 2, **, А. И. Цепенок 3, ***, А. О. Плешко 2, ****
1 Сибирский федеральный университет
660041 Красноярск, Россия
2 Национальный исследовательский Томский политехнический университет
634050 Томск, Россия
3 ООО “ЗиО-Энерджи”
630049 Новосибирск, Россия
* E-mail: azhuikov@sfu-kras.ru
** E-mail: dmitriyog@tpu.ru
*** E-mail: alexey.tsepenok@gmail.com
**** E-mail: p.andrey12@mail.ru
Поступила в редакцию 28.05.2023
После доработки 28.05.2023
Принята к публикации 07.06.2023
- EDN: HBIEXC
- DOI: 10.31857/S0023117723050080
Аннотация
С применением современных методик, аналитического и экспериментального оборудования определены характеристики процессов термического разложения и горения, включая концентрации основных компонентов дымовых газов (CO, CO2, NOx, H2S + SO2), при нагреве мелкодисперсных частиц (100–200 мкм) черногорского каменного угля, древесины лиственницы и смесей на их основе. Содержание биомассы в составе топливных смесей на основе угля составляло 10, 20 и 30 мас. %. Методом синхронного термического анализа для индивидуальных твердых топлив и их смесей установлены температуры, при которых происходит воспламенение коксового остатка и завершение процесса горения. Опилки лиственницы более реакционно способные по сравнению с черногорским каменным углем, благодаря наиболее низкой температуре, при которой происходит зажигание углеродного остатка, поэтому добавление даже 10% биомассы к углю оказывает положительное влияние на реакционную способность смеси. В условиях нагрева топлив в потоке воздуха при температурах 500–800°С с помощью программно-аппаратного комплекса высокоскоростной видеорегистрации быстропротекающих процессов определены времена задержки зажигания. По результатам проведенных исследований установлено, что времена задержки зажигания рассматриваемых топлив в потоке разогретого воздуха варьируются в диапазоне от 0.02 до 0.22 с, а добавление 10–30 мас. % биомассы к углю снижает времена задержки зажигания топливных смесей до 50%. Анализ дымовых газов при горении твердых топлив позволил установить концентрации основных антропогенных выбросов, использование биомассы в качестве добавки к углю снижает выбросы диоксида углерода, оксидов азота и соединений серы (H2S + SO2) на 2.2–13.5%; 6.2–28.9% и 18.2–33.3% растет соответственно.
1. ВВЕДЕНИЕ
В настоящее время растет потребность развития топливно-энергетического комплекса путем вовлечения перспективных видов твердого топлива, так как значительная, а во многих регионах основная, выработка тепловой и электрической энергии происходит путем сжигания твердого ископаемого топлива, продукты горения которого (газообразные и твердые) оказывают негативное воздействие на окружающую среду, в том числе на здоровье человека [1]. К перспективным топливам можно отнести двухкомпонентные смеси на основе твердых горючих. Состав топливных смесей формируют в зависимости от решаемых задач, например для утилизации отходов деревообрабатывающих предприятий; интенсификации процесса воспламенения углей средней и высокой степени метаморфизма, снижения уровня выбросов загрязняющих веществ, снижения углеродного следа. В случае, если реакционная способность углей (например, низкой степени метаморфизма) относительно высока, то биомассу можно добавлять для снижения зольности и содержания вредных газообразных компонентов в дымовых газах [2–4].
При формировании топливных смесей важно обоснование соотношения твердых горючих компонентов (например, угля и биомассы). Как правило, биомасса имеет относительно низкую теплоту сгорания при высоком содержании летучих компонентов, что характеризует ее высокую реакционность по сравнению с твердыми ископаемыми топливами, для которых характерна относительно высокая теплота сгорания при низком содержании летучих компонентов [5]. В условиях факельного сжигания твердого топлива высокое содержание биомассы в смеси может оказать негативное влияние на интенсификацию шлакования поверхностей нагрева из-за высокого содержания соединений щелочных и щелочноземельных металлов [6, 7]. Еще один негативный фактор практического применения биомассы – ее гидрофильная поверхность. При хранении на складе биомасса впитывает влагу из окружающей среды, что влияет на снижение теплоты сгорания, поэтому необходимо предусматривать дополнительные мероприятия по ее сушке [8, 9]. При использовании древесной биомассы также необходимо учитывать саму структуру топливных частиц, состоящих из волокон, которые достаточно трудно поддаются измельчению в отличие от угля. Анализируя перечисленные достоинства и недостатки биомассы, необходимо всесторонне обосновывать долю ее содержания в топливной смеси при совместном сжигании с углем [10–13].
Цель данной работы – установление характеристик интенсификации процесса воспламенения каменного угля путем добавления биомассы в условиях факельного сжигания с оценкой состава дымовых газов. Результаты исследования можно использовать при проектировании энергетических установок, работающих на твердом топливе.
2. МАТЕРИАЛЫ И МЕТОДЫ
2.1. Топлива. При проведении экспериментальных исследований использованы следующие твердые топлива:
1) черногорский каменный уголь марки Д (далее условное обозначение У), Черногорский угольный разрез, Республика Хакасия, Россия;
2) опилки лиственницы (далее условное обозначение Б), деревообрабатывающее предприятие Красноярска, Россия.
Черногорский длиннопламенный каменный уголь добывается на территории Черногорского угольного месторождения (окрестности г. Черногорска, Республика Хакасия, Россия), являющегося одним из основных промышленных месторождений Минусинского угольного бассейна. Черногорский уголь используется в качестве энергетического топлива как при производстве тепловой энергии в котельных малой мощности, так и на крупных ТЭЦ.
Лиственница на территории Сибири – распространенный вид древесины хвойных пород, которая используется в качестве сырья на лесоперерабатывающих предприятиях для производства различных изделий. Типичные отходы этих предприятий в виде опилок подлежат утилизации, так как они представляют экологическую и пожарную опасность в условиях складирования на промышленных площадках в больших объемах.
Основные характеристики твердых топлив (угля и древесины) приведены в табл. 1.
Таблица 1.
Результаты технического и элементного анализов угля и биомассы
Топливо | Wa | Ad | Vdaf | Элементный состав, мас. % на daf | $Q_{s}^{{daf}}$, МДж/кг | ||||
---|---|---|---|---|---|---|---|---|---|
C | H | N | S | O | |||||
% | |||||||||
У | 4.5 | 3.5 | 44.0 | 53.6 | 3.5 | 1.4 | 0.4 | 41.1 | 31.0 |
Б | 4.1 | 0.2 | 80.0 | 50.4 | 5.9 | 0.3 | – | 43.3 | 19.6 |
Технический и элементный анализы твердых топлив проводились в рамках стандартных методик: влага аналитическая по ГОСТ Р 33503-2015; зольность по ГОСТ Р 55661-2013; выход летучих компонентов по ГОСТ Р 55660-2013; теплота сгорания по ГОСТ Р 147-2013; содержание углерода, водорода, азота по ГОСТ Р 32979-2014, кислорода по ГОСТ Р 27313-2015, серы ГОСТ 8606-2015. При проведении аналитических исследований использовалось оборудование: муфельная печь Snol 7.2/1300 (AB “Umega”, Литва) для определения содержания летучих веществ и зольности; калориметр C6000 (IKA, Германия); элементный анализатор Vario MACRO cube (Elementar Analysensysteme GmbH, Германия); анализатор влажности MA-150 (Sartorius, Германия).
При подготовке твердых топлив к проведению исследований применялось следующее оборудование. Дисковой мельницей Retsch DM 200 (Retsch GmbH, Германия) измельчались топливные частицы. Просеивающей машиной RETSCH AS 200 BASIC (Retsch GmbH, Германия) отделялись топливные частицы размерами 100–200 мкм. Указанный диапазон размеров топливных частиц соответствует размерам пылеугольного топлива, применяемого при факельном сжигании на объектах теплоэнергетики [14].
Вследствие достаточно существенного отличия структуры частиц твердых топлив (угля и биомассы), которая может оказывать влияние на процесс горения, анализ их поверхностей осуществлялся с помощью сканирующего электронного микроскопа ТМ4000 (Hitachi, Япония) (ускоряющее напряжение 20 кэВ), оборудованного энергодисперсионным спектрометром и системой рентгеновского микроанализа Quantax 75 (Bruker, Германия), в режиме низкого вакуума (без напыления платины).
Одним из аспектов частичной замены угля на биомассу (в отличие от полного перехода на твердое биотопливо) в условиях промышленной энергогенерации является отсутствие высоких капитальных затрат на реконструкцию действующего технологического оборудования. Кроме того, на основании опыта эксплуатации энергогенерирующих объектов на топливных смесях сделан вывод, что основным негативным фактором существенного увеличения доли биомассы в твердотопливной смеси является снижение теплоты сгорания (при идентичном расходе топлива или увеличении расхода твердотопливной смеси при идентичном энерговыделении). Теплота сгорания биомассы на 63% ниже, чем у угля (табл. 1), соответственно, добавление 10% биомассы к углю снижает теплоту сгорания смеси на 4%; увеличение доли биомассы в смеси до 20% ведет к снижению теплоты сгорания на 8%, а увеличение доли биомассы до 30% снижает теплоту сгорания топлива на 12% по сравнению с углем. Достаточно существенное снижение теплоты сгорания твердотопливной смеси ведет к ухудшению технико-экономических показателей процесса энергогенерации.
Анализ результатов экспериментальных исследований [15–18] позволил сделать вывод, что доля биомассы в твердотопливных смесях, как правило, составляет от 10 до 30%. Это объясняется следующими технологическими аспектами:
• относительно низкая температура шлакования золы биомассы (менее 1000°С) может оказать серьезное влияние на интенсивность загрязнения поверхностей нагрева и изменение теплового режима топки котла, что потребует реконструкции системы очистки поверхностей нагрева или ограничения номинальной мощности котла;
• увеличение доли биомассы в топливной смеси ведет к необходимости глубокой модернизации системы топливоприготовления, существующие системы подготовки угля к сжиганию не обеспечивают размол биомассы до размеров угольных частиц вследствие волокнистой структуры древесины;
• для хранения биомассы на территории объектов теплоэнергетики необходимо сооружать навесы для защиты от влаги из-за развитой пористой структуры частиц, что в свою очередь влияет на ограничение объема ее потребления;
• эффективность пневматического транспортирования твердотопливных смесей с относительно высокой долей биомассы снижается (по сравнению с углем) из-за высокой пластичности и вариативности форм частиц биомассы с волокнистой структурой;
• отличия в насыпной плотности угля и биомассы обуславливают сложности при предварительном перемешивании компонентов топливной смеси;
• увеличение влажности топлива приводит к росту расхода дымовых газов, повышению нагрузки на золоулавливающие установки и дымососы.
В работе рассмотрены индивидуальные твердые топлива и смеси на их основе следующего компонентного состава (по массе): У 100%; У 90% + Б 10%; У 20% + Б 80%; У 30% + Б 70%; Б 100%.
2.2. Синхронный термический анализ. Проведение синхронного термического анализа в рамках данного исследования обусловлено получением данных для оценки реакционной способности угля, биомассы и их смесей при нагреве, а также для определения кинетических характеристик процессов их горения. Для проведения анализа использовался термический анализатор SDT Q600 (TA Instruments-Waters LLC, США): пределы допускаемой абсолютной погрешности измерения температуры ±1°C, пределы допускаемой относительной погрешности измерения теплового потока ±5%, пределы допускаемой приведенной погрешности измерения массы ±1%. Термический анализ проводился в потоке воздуха с расходом 50 мл/мин при скорости нагрева 20°C/мин, начальные массы навесок топлив составляли около 6 мг. Обработка данных проводилась с помощью ПО Universal Analysis 2000 (TA Instruments-Waters LLC, США).
Для анализа характеристик процессов при нагреве топлив в окислительной среде использовались профили кривых термогравиметрии (ТГ – убыль массы навески), дифференциальной термогравиметрии (ДТГ – скорость убыли массы навески) и дифференциальной-сканирующей калориметрии (ДСК – тепловые эффекты).
Энергия активации и предэкспоненциальный множитель для описания процессов горения угля, биомассы и их смесей определены методом Коутса–Редферна [19, 20] с использованием выражений:
Реакционная способность топлива в условиях относительно медленного нагрева обратно пропорциональна температуре (ТДТГ), соответствующей максимальной скорости убыли массы (ДТГmax), т.е. с уменьшением ТДТГ реакционная способность топлива увеличивается [21, 22]. Температура, при которой происходит зажигание углеродистого остатка (Ti), определялась по методу пересечения кривых ТГ и ДТГ, а температура, при которой процесс горения завершался (Tb), соответствовала скорости убыли массы, равной 1%/мин, после крайнего экстремума ДТГ в области высоких температур [23, 24].
2.3. Экспериментальный стенд сжигания топлив в потоке разогретого воздуха. Определение характеристик процесса зажигания как индивидуальных топлив, так и топливных смесей проводилось на лабораторном стенде (рис. 1) по апробированной методике [25]. Основными компонентами стенда являются: воздушный вентилятор высокого давления 1 ROBUST (LEISTER, Германия): мощность 0.25 кВт, максимальный расход воздуха 1200 л/мин, максимальное статическое давление 8 кПа; воздухонагреватель 2 LEISTER LE 5000 HT (LEISTER, Германия): мощность 11 кВт, максимальная температура воздуха на входе 100°C, максимальная температура воздуха на выходе 900°C, минимальный расход воздуха 635 л/мин; трубчатая муфельная печь 3 General Therm RT 1000.1100 SP (Nevaterm, Россия): мощность 13 кВт, кварцевый цилиндр длиной 1 м и внутренним диаметром 0.1 м, обогреваемая длина 0.9 м, максимальная температура 900°C.
Рис. 1.
Внешний вид экспериментального стенда: 1 – воздушный вентилятор; 2 – воздухонагреватель; 3 – муфельная печь с кварцевой трубой; 4 – воздухоохладитель; 5 – вытяжная вентиляция; 6 – система рециркуляции разогретого воздуха; 7 – механизм ввода мелкодисперсных частиц топлива в поток разогретого воздуха; 8 – термопары; 9 – многоканальный регистратор; 10 – щит управления; 11 – щит электропитания; 12 – блок управления вытяжной вентиляцией.
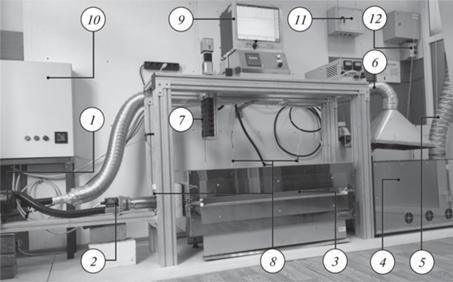
Воздушный вентилятор 1 совместно с воздухонагревателем 2 нагнетают поток разогретого воздуха (со скоростью 5 м/с) в кварцевый цилиндр длиной 1 м, а трубчатая муфельная печь 3 поддерживает равномерное распределение температуры (гарантированно в диапазоне 20–850°C) по всей длине кварцевого цилиндра за счет минимизации теплоотвода в окружающую среду. Температура воздушного потока после воздухонагревателя 2, на входе в кварцевый цилиндр, в средней его части и на выходе регистрировалась четырьмя термопарами 8 (номинальная статическая характеристика ХА, диапазон измеряемых температур 0–1100°С, точность при измерении температур более 400°С составляет ±0.004T, инерционность менее 3 с). Рабочие спаи термопар располагались вдоль оси симметрии воздушного потока. Показания термопары, расположенной на выходном патрубке воздухонагревателя 2, использовались в качестве обратной связи при регулировании температуры потока разогретого воздуха. Показания трех термопар, расположенные в кварцевом цилиндре муфельной печи 3, регистрировались многоканальным регистратором 9 РМТ-59 (Элемер, Россия): 12 измерительных каналов, цикл опроса всех каналов менее 1 с, диапазон измеряемых температур от –50 до 1100°С (при подключении термопар с номинальной статической характеристикой ХА), класс точности A, пределы допускаемой основной приведенной погрешности ±0.25%.
Воздухоохладитель 4 (комплектно с трубчатой муфельной печью General Therm RT 1000.1100 SP) предназначен для снижения температуры до 150°C воздушного потока и дымовых газов, удаляемых в атмосферу посредством вытяжной вентиляции 5. Система рециркуляции разогретого воздуха 6 служит для отвода теплоты, аккумулируемой воздухоохладителем, и повышения эффективности лабораторного стенда за счет подачи разогретого воздуха с температурой не более 100°С на вход воздушного вентилятора 1.
С помощью автоматизированного механизма 7 порция топлива массой около 5 мг через керамический канал диаметром 6 мм, проходящий сквозь верхнюю крышку муфельной печи 3 (рис. 1) и соответствующее отверстие в стенке кварцевой трубы, вводилась в воздушный поток. Процессы, протекающие при движении мелкодисперсных твердых частиц в воздушном потоке (внутри кварцевого цилиндра) на протяжении 0.9 м, регистрировались через смотровую щель муфельной печи 3 (рис. 1) высокоскоростной цветной видеокамерой Phantom V411 (Vision Research, США): скорость съемки 4000 кадров в секунду при разрешении 1008 × 56 пикселей, глубина изображения 12 бит, размер пикселя матрицы 20 мкм, минимальное время экспозиции 1 мкс. Комплектно с видеокамерой использовался широкоугольный объектив Distagon 1.4/35 ZF.2 T* (Carl Zeiss, Германия): диафрагма при минимальном фокусном расстоянии 1.4, минимальное фокусное расстояние 35 мм. Видеокамера располагалась перпендикулярно трубчатой муфельной печи 3 на расстоянии около 2 м от смотровой щели.
Автоматизированная обработка видеозаписей выполнялась с помощью стандартного ПО Phantom Camera Control (Vision Research, США). Цветные видеозаписи исследуемого процесса конвертировались в монохромный формат. Далее эти видеозаписи последовательно обрабатывались алгоритмом, который покадрово контролировал значения оттенков серого (от 0 до 4095 – от черного до белого цвета, соответственно) в каждой точке (пикселе) области видеорегистрации. В черно-белой цветовой гамме интервал интенсивности свечения 3520–4095 соответствует интенсивному экзотермическому реагированию, т.е. процессу горения топлива. Момент зажигания регистрировался автоматически по достижению (или превышению) порогового значения (3520 в оттенках серого) интенсивности свечения в какой-либо точке в области видеорегистрации. Таким образом определялась координата плоскости, перпендикулярная направлению движения воздушного потока, в которой зажигалась частица топлива. Систематическая и случайная погрешности определения времен td, обусловленные скоростью видеорегистрации и разбросом экспериментальных данных, не превышали 0.5 и 15% соответственно.
Для угля, биомассы и топливных смесей на основе этих компонентов проводились серии экспериментов (от 5 до 10) при постоянных значениях температуры (Tg) потока разогретого воздуха (диапазон 500–800°C с шагом 50°C) в кварцевом цилиндре муфельной печи 3 (рис. 1). Контролируемая область видеорегистрации составляла L = 0.9 м. Это расстояние проходили частицы топлива от плоскости поперечного сечения кварцевого цилиндра с координатой x = 0, где они вводились в воздушный поток, до его выходного сечения x = L.
Достоверно установить время задержки зажигания путем деления значения установленной координаты на мгновенное значение скорости движения частиц топлива в потоке воздуха невозможно. Это объясняется тем, что частицы разных размеров (100–200 мкм) вводились с начальной скоростью Vp = 0 в воздушный поток, скорость которого Va = = 5 м/с постоянна вдоль всей длины кварцевого цилиндра муфельной печи 3 (рис. 1). При движении таких частиц в воздушном потоке в условиях роста скорости (частицы разгоняются с Vp = 0 до Vp = Va) ее значения достаточно существенно отличаются для частиц разных размеров и плотностей [26].
Для определения значений td было получено аппроксимационное выражение td = f(x) для твердых частиц дисперсностью 100–200 мкм путем решения задачи в рамках теории гидродинамики гетерогенных сред, основные положения которой достаточно подробно описаны в [27]. Предполагалось, что твердые частицы плотностью ρp сферической формы (размеры соответствовали средним размерам указанного диапазона Dp = = 150 мкм) вводились с начальной скоростью Vp = 0 в горизонтальный воздушный поток c характеристиками Va = 5 м/с, ρa = 0.383 кг/м3, µa = 40.5 × 10–6 Па с. Были приняты средние значения плотности и динамической вязкости воздуха в диапазоне температур 500–800°C, т.к. их значения в этом диапазоне изменяются менее чем на 30 и 20% соответственно. После ввода порции топлива в воздушный поток объемная концентрация частиц в условиях их движения в цилиндрической трубе диаметром 0.1 м составляла менее 0.02 (разреженная дисперсная система), поэтому при решении сформулированной задачи рассматривалось движение одиночной частицы, характеристики которой не зависят от соседних частиц. В рамках используемого упрощенного подхода не учитывалось влияние динамического и теплового запаздывания частиц на характеристики воздушного потока. Предполагалось, что на частицу действует только сила сопротивления (несущая сила воздушного потока). Действие силы тяжести не учитывалось, так как при анализе видеограмм зарегистрировано прямолинейное движение частиц в горизонтальном направлении.
Установлено, что при указанных выше исходных данных режим течения частиц разных размеров в воздушном потоке характерен для переходной области, так как Re = 7.09 (промежуточный режим обтекания частицы дисперсной фазы реализуется в диапазоне чисел Рейнольдса Re = 0.015–700 [28]). В таких условиях зависимость безразмерной скорости частицы от безразмерного времени имеет вид [29]:
Таким образом, согласно приведенным выражениям, чем больше размер частиц и их плотность, тем больше времени и расстояния (которое ограничено конструкцией экспериментального стенда L = 0.9 м) требуется для роста их скорости до значения Va, что соответствует результатам исследования [26, 30] и реальным условиям протекания аэродинамических процессов в топках котлов при факельном сжигании твердого натурального топлива [31, 32]. В таких условиях в экспериментах скорость частиц с большей плотностью (уголь ρp = 800 кг/м3) будет ниже по сравнению с частицами меньшей плотности (биомасса ρp = 540 кг/м3) при L = 0.9 м, Dp = 150 мкм и прочих идентичных условиях.
Условия проведения эксперимента соответствуют условиям факельного сжигания твердого натурального топлива в топках котлов в отличие от условий широко распространенного термогравиметрического анализа твердого топлива при нагреве в окислительной среде. В последнем случае реализуется низкотемпературное зажигание топлива. При типичных скоростях нагрева 5–20°C/мин камеры термогравиметрического анализатора топливо прогревается относительно равномерно с постепенным выходом влаги и летучих компонентов. Интенсивность этих эндотермических процессов при умеренном подводе теплоты относительно невысока, и они не оказывают существенное влияние на процессы тепломассопереноса как в самой пористой частице твердого топлива, так и в ее окрестности. В таких условиях воспламенение формирующейся горючей газовой смеси происходит при относительно невысоких температурах, а выделяющаяся теплота способствует прогреву и воспламенению коксового остатка. При реализации механизма высокотемпературного зажигания частиц топлива температурные градиенты на границе “частица–разогретый воздух” достигают нескольких сотен градусов (как правило, не менее 500°C). При достаточно быстром нагреве топлива интенсивные нестационарные процессы испарения влаги и термического разложения оказывают достаточно существенное влияние на процессы теплопередачи и гидродинамики в системе “частица – разогретый воздух”. Выделяющиеся холодные пары воды и летучие компоненты формируют газовую оболочку в окрестности частицы, тем самым препятствуя непосредственному взаимодействию углеродистого остатка с разогретым воздухом. В целом эти условия быстротечны, а более высокие значения пороговых температур, необходимых для зажигания частиц топлива при высокотемпературном механизме (по сравнению с низкотемпературным механизмом), характеризуются жесткими ограничениями по длительности протекания процесса воспламенения, обусловленными конструкцией и габаритами технологического оборудования.
2.4. Экспериментальный стенд для анализа состава дымовых газов. На рис. 2 представлена схема экспериментального стенда для определения состава дымовых газов при сжигании индивидуальных твердых топлив и смесей на их основе.
Рис. 2.
Схема экспериментального стенда: 1 – электрическая трубчатая муфельная печь; 2 – координатный механизм; 3 – ноутбук с ПО; 4 – газоанализатор; 5 – зонд для забора газа; 6 – топливо.
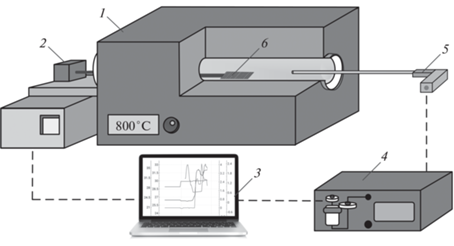
Сжигание исследуемых топлив проводилось в электрической трубчатой муфельной печи 1 Nabertherm R 50/250/13 (Nabertherm, Германия): внутренний диаметр керамической трубки 0.04 м, длина 0.45 м; диапазон варьирования температуры 20–1200°C; температура регулируется по показаниям встроенной термопары с номинальной статической характеристикой ПП. Для анализа состава дымовых газов применялся газоанализатор Test 1 (ООО “Бонэр”, Россия), оснащенный электрохимическими сенсорами: О2 (диапазон 0–25%, абсолютная погрешность ±0.2%), СО (диапазон 0–40 000 ppm, относительная погрешность ±5%), SO2 (диапазон 0–1000 ppm, относительная погрешность ±5%), NO (диапазон 0–2000 ppm, относительная погрешность ±5%), NO2 (диапазон 0–500 ppm, относительная погрешность ±7%), H2S (диапазон 0–500 ppm, относительная погрешность ±5%), HCl (диапазон 0–2000 ppm, относительная погрешность ±5%). Дополнительно газоанализатор оснащен оптическими сенсорами СО2 (диапазон 0–30%, приведенная погрешность ±2%), СН4 (диапазон 0–30%, приведенная погрешность ±5%), СО (диапазон 0–30%, приведенная погрешность ±5%) и полярографическим сенсором Н2 (диапазон 0–5%, абсолютная погрешность ±5%). В состав прибора входят модульный зонд, конденсатосборник и система фильтрации для осушения и очищения газовой пробы. Специальное программное обеспечение газоанализатора Test 1 позволяло в режиме реального времени контролировать изменение концентраций антропогенных газов в процессе горения твердого топлива.
При проведении экспериментов муфельная печь 1 предварительно прогревалась до заданной температуры Tg. Навеска топлива 6 массой около 0.2 г при помощи координатного механизма 2 подавалась в камеру сгорания. С противоположной от координатного механизма стороны в трубку муфельной печи вводился зонд газоанализатора 5. На время проведения эксперимента оба отверстия трубки муфельной печи закрывались герметично теплоизолирующим материалом. В ходе протекания процессов зажигания и горения дымовые газы через модульный зонд 5 поступали в корпус газоанализатора 4 (проходя стадии осушения и фильтрации), в котором измерялись концентрации компонентов газовой смеси. После окончания каждого эксперимента газовые каналы газоанализатора и полость трубки муфельной печи продувались воздухом для удаления остатков дымовых газов. В рамках одной серии выполнялось от 5 до 10 экспериментов при идентичных начальных условиях. Определение средних по времени концентраций газов осуществлялось с помощью метода трапеций, подробно описанного авторами [33].
3. РЕЗУЛЬТАТЫ И ОБСУЖДЕНИЕ
3.1. Характеристики зажигания и горения топлив в условиях термогравиметрического анализа. Процессы горения индивидуальных топлив иллюстрируют профили кривых ТГ и ДТГ, приведенные на рис. 3. Здесь условно выделены основные стадии, протекающие при нагреве топлив в диапазоне температур 30–800°С. На начальном этапе прогрева твердых топлив (до 130°С) происходит испарение влаги (рис. 3, а; стадия 1), сопровождающееся увеличением скорости убыли массы навески (рис. 3, б; стадия 1). Дальнейший прогрев топлив ведет к их термическому разложению (рис. 3; стадия 2), сопровождающемуся выходом летучих веществ с дальнейшим их воспламенением и горением. У биомассы из-за относительно высокого содержания летучих веществ (табл. 1) этот процесс интенсифицируется в области более низких температур 130–185°С (рис. 3, б) против 130–420°С (рис. 3, б) у угля. Летучие вещества выгорают в окрестности поверхности топливных частиц, что способствует интенсификации воспламенения коксового остатка. Температура, при которой происходит воспламенение коксового остатка биомассы, составляет 294°С, угля – 421°С.
Рис. 3.
Кривые ТГ (а), ДТГ (б) при нагреве угля (У) и биомассы (Б) и их смесей (У 90% + Б 10%; У 80% + Б 20%; У 70% + Б 30%).
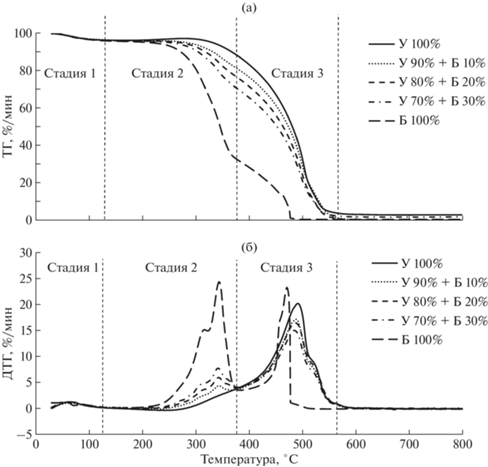
Для процесса горения биомассы характерны два явно выраженных экстремума на профилях кривых ДТГ, а для угля – один экстремум (рис. 3, б). В случае биомассы первый максимум (рис. 3, б; стадия 3) при температурах 200–380°С соответствует горению летучих веществ продуктов термического разложения (целлюлоза, гемицеллюлоза и часть лигнина), при этом максимальная скорость убыли массы составляет 24.3%/мин (рис. 3, б). Второй экстремум ДТГ (рис. 3, б; стадия 3) находится в области более высоких температур (380–484°С) и соответствует горению коксового остатка биомассы с максимальной скоростью убыли массы навески 23.2%/мин. Из-за относительно высокого содержания летучих веществ в биомассе (табл. 1) максимальная скорость убыли массы навески в первом максимуме выше, чем во втором.
Для угля основной максимум на кривой ДТГ (рис. 3, б) при температурах 280–570°С иллюстрирует процессы горения летучих веществ и интенсивного выгорания углеродистого остатка, при этом максимальная скорость убыли массы составляет 20.2%/мин (рис. 3, б). В случае же условного разделения основного экстремума на стадии выгорания летучих веществ и углеродистого остатка (стадии 2 и 3) максимальная скорость убыли массы для летучих веществ составляет 2.7%/мин, для углеродистого остатка приведенные выше значения – 20.2%/мин. Процесс горения коксового остатка биомассы завершается при температуре 484°С, угля – при температуре 570°С (рис. 3).
При добавлении 10 мас. % биомассы к углю стадия 2 протекает в диапазоне температур 130–407°С с максимальной скоростью убыли массы 4.4%/мин (рис. 3). Стадия 3 (рис. 3), сопровождающаяся зажиганием и горением углеродистого остатка, протекает в диапазоне температур 408–567°С с максимальной скоростью убыли массы 17.1%/мин. Температура, при которой происходит зажигание углеродистого остатка, составляет 408°С. Завершается процесс горения при температуре 567°С.
В смеси с добавлением 20 мас. % биомассы к углю стадия 2 (рис. 3) соответствует диапазону температур 130–393°С с максимальной скоростью убыли массы 6.0%/мин (табл. 2). Стадия 3 (рис. 3) протекает в диапазоне температур 394–563°С с максимальной скоростью убыли массы 16.5%/мин. Завершается процесс горения при температуре 563°С.
Таблица 2.
Характеристики процессов, протекающих при нагревании индивидуальных топлив и топливных смесей
Характеристика | Топливо | ||||
---|---|---|---|---|---|
100% У | 90% У + 10% Б | 80% У + 20% Б | 70% У + 30% Б | 100% Б | |
ДТГmax1, %/мин | 1.3 | 1.2 | 1.2 | 1.3 | 1.3 |
ТДТГ1, °C | 63 | 63 | 64 | 65 | 55 |
ДТГmax2, %/мин | 2.7 | 4.4 | 6.0 | 7.7 | 24.3 |
ТДТГ2, °C | 350 | 344 | 344 | 343 | 344 |
Ti, °C | 421 | 408 | 394 | 378 | 294 |
ДТГmax3, %/мин | 20.2 | 17.1 | 16.5 | 15.0 | 23.2 |
ТДТГ3, °C | 492 | 488 | 486 | 484 | 471 |
Tb, °C | 570 | 567 | 563 | 556 | 484 |
Примечание. ДТГmax1 – максимальная скорость убыли массы в диапазоне температур, соответствующем испарению влаги, %/мин; ТДТГ1 – температура, соответствующая ДТГmax1, °C; ДТГmax2 – максимальная скорость убыли массы в диапазоне температур, соответствующем выгоранию летучих веществ, %/мин; ТДТГ2 – температура, соответствующая ДТГmax2, °C; Ti – температура, соответствующая воспламенению коксового остатка, °C; ДТГmax3 – максимальная скорость убыли массы в диапазоне температур, соответствующем выгоранию коксового остатка, %/мин; ТДТГ3 – температура, соответствующая ДТГmax3, °C; Tb – температура, соответствующая завершению процесса горения топлива, °C.
При увеличении доли биомассы в смеси до 30% стадия 2 (рис. 3) протекает в диапазоне температур 130–377°С. Максимальная убыль массы в этом диапазоне достигает 7.7%/мин. Стадия 3 (рис. 3) соответствует диапазону температур 378–556°С, при этом максимальная убыль массы достигает 15%/мин.
Основные установленные характеристики процессов нагрева индивидуальных топлив и топливных смесей представлены в табл. 2. Анализ полученных характеристик горения (табл. 2) твердотопливных смесей и индивидуального угля (энергетического топлива) позволил установить следующие количественные отличия. Для биомассы по сравнению с углем характерны более низкие температуры, при которых происходит воспламенение углеродистого остатка, TДТГ соответствующей стадии 3 и температуры, при которой происходит завершение процесса горения (294; 471 и 484°С против 421; 492 и 570°С соответственно). Добавление к углю 10; 20 и 30 мас. % биомассы снижает температуру, при которой происходит зажигание, на 3; 7 и 11%, соответственно, по сравнению с углем. Аналогично происходит снижение температуры, соответствующей максимальной скорости убыли массы при горении углеродистого остатка, на 1; 1 и 2%, соответственно, по сравнению с углем. Температура, при которой происходит завершение процесса горения, снижается на 1; 1 и 3%, соответственно, по сравнению с углем (табл. 2). Снижение этих температурных характеристик свидетельствует о том, что добавление даже 10 мас. % биомассы к углю положительно влияет на основные характеристики воспламенения угля. Однако увеличение содержание биомассы в смеси может повлиять на ухудшение технико-экономических показателей энергетической установки (см. п. 2.3).
Основные кинетические параметры включают в себя средне-интегральные значения энергии активации и предэкспоненциального множителя (табл. 3).
Таблица 3.
Кинетические характеристики процесса горения твердых топлив и их смесей
Топливо | Е, кДж/моль | А, с–1 | R2 |
---|---|---|---|
У 100% | 51.0 | 3 × 107 | 0.9955 |
У 90% + Б 10% | 36.7 | 2 × 108 | 0.9924 |
У 80% + Б 20% | 43.9 | 5 × 107 | 0.9991 |
У 70% + Б 30% | 44.8 | 3 × 107 | 0.9953 |
Б 100% | 64.0 | 4 × 105 | 0.9979 |
Коэффициент корреляции (табл. 3) для всех топлив составил от 0.9924 до 0.9991, что свидетельствует о приемлемой достоверности выбранного метода Коутса-Редферна для описания эффективных кинетических характеристик исследуемого процесса.
При нагревании топлива протекают как эндотермические процессы, сопровождающиеся поглощением теплоты (например, испарения влаги), так и экзотермические процессы, при которых выделяется теплота (например, горение летучих веществ и углеродистого остатка). При анализе кривых дифференциальной сканирующей калориметрии можно количественно оценить значения этих тепловых эффектов. Результаты анализа представлены в табл. 4.
Таблица 4.
Тепловые эффекты процессов при нагревании угля, биомассы и их смесей
Топливо | Тепловой эффект, МДж/кг | ||
---|---|---|---|
Стадия 1 (эндо) | Стадия 2 (экзо) | Стадия 3 (экзо) | |
У 100% | 1.4 | 1.4 | 28.2 |
У 90% + Б 10% | 1.5 | 1.8 | 26.6 |
У 80% + Б 20% | 1.6 | 2.2 | 24.9 |
У 70% + Б 30% | 1.3 | 2.5 | 23.8 |
Б 100% | 1.5 | 3.1 | 14.8 |
Основное тепловыделение происходит в процессе горения углеродистого остатка (табл. 4). Небольшое теплопоглощение связано с испарением влаги на стадии 1. При добавлении биомассы к углю на стадии 2 тепловыделение увеличивается за счет большего содержания летучих веществ в древесине (табл. 1). На стадии 3 при выгорании углеродистого остатка удельное тепловыделение снижается из-за меньшей доли угля в смеси, теплота сгорания которого выше, чем у биомассы из-за большего содержания углеродистой составляющей (табл. 1).
3.2. Характеристики зажигания топлив в потоке разогретого воздуха. На рис. 4 представлены кривые зависимостей времен задержки зажигания частиц (размерами 100–200 мкм) угля и биомассы, а также их смесей от температуры окислителя в диапазоне 500–800°C при движении мелкодисперсных частиц топлива в потоке разогретого воздуха со скоростью Va = 5 м/с. Аппроксимационные кривые проведены через точки, характеризующие средние значения времен задержки зажигания (td), установленные в сериях из 5–10 экспериментов при идентичных начальных условиях. Левой границей температурного диапазона является минимальное значение Ta = = 500°C, при котором в условиях проведения эксперимента воспламеняется биомасса (за промежуток времени менее 0.2 с). Правая граница соответствует максимальному значению температуры воздушного потока Ta = 800°C, которое гарантированно поддерживается на контролируемом участке кварцевой трубы (рис. 1). Времена задержки зажигания возрастают в следующей последовательности: биомасса (Б 100%), смесь угля и биомассы (У 70% + Б 30%), смесь угля и биомассы (У 80% + Б 20%), смесь угля и биомассы (У 90% + Б 10%, У 100%), уголь (У 100%).
Рис. 4.
Зависимости времен задержки зажигания частиц угля, биомассы и их смесей (У 90% + Б 10%; У 80% + Б 20%; У 70% + Б 30%) от температуры разогретого воздуха.
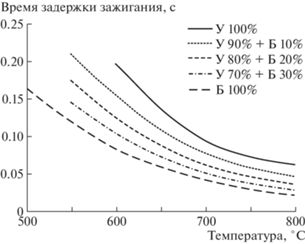
Наименьшие значения времен задержки зажигания td биомассы по сравнению с углем объясняются наименьшим содержанием влаги, наибольшим содержанием летучих компонентов в ее составе (см. табл. 1) и большим количеством пор, трещин и каналов на поверхности частиц. На рис. 5 представлены снимки СЭМ частиц угля и биомассы. Частица угля имеет сферическую форму, на поверхности которой расположено большое количество узких пор и трещин, через которые окислитель может проникать в глубинные слои (рис. 5, а). Частица биомассы имеет продолговатую цилиндрическую форму, внутри ее расположены относительно крупные каналы. Поверхность древесины покрыта большим количеством отверстий, что характерно для ее структуры. При качественном сравнении угля и биомассы частицы последней имеют большее число каналов и пор крупного размера, что свидетельствует о высокой удельной площади поверхности частиц (рис. 5, б).
Рис. 5.
СЭМ-изображения топливных частиц: черногорский каменный уголь; увеличение 250 (а); опилки лиственницы; увеличение 300 (б).
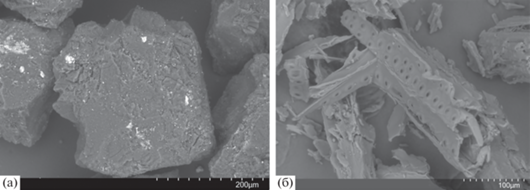
После ввода мелкодисперсных частиц угля в поток разогретого воздуха практически вся подводимая теплота от внешнего источника расходуется на протекание эндотермических процессов фазового превращения (испарение влаги) и термического разложения, сопровождающихся поглощением теплоты (табл. 4). Кроме того, уголь имеет достаточно плотную структуру преимущественно с закрытыми порами относительно внешней газовой среды. Чем выше значение Vdaf, тем меньше время задержки зажигания соответствующего топлива при прочих идентичных условиях, поэтому для угля в отличие от биомассы требуется больше энергии (и соответственно времени при Ta = const) на развитие гетерогенного горения. Стоит отметить, что чем больше содержание биомассы в топливной смеси, тем интенсивней протекает процесс ее воспламенения. Отличия времен задержки зажигания топливных смесей и черногорского каменного угля (рис. 4) составляют 20–48% (при температуре 600°C).
Типичные кадры видеограмм высокоскоростной видеорегистрации процессов зажигания и горения частиц угля и биомассы, а также их смесей приведены на рис. 6–10. С шагом ∆t = 0.10 c от момента воспламенения топлива показана динамика развития процесса горения мелкодисперсных частиц топлив размерами 100–200 мкм в потоке разогретого воздуха при Ta = 700°C. На расстояниях, пройденных горючими частицами от начала их прогрева до момента воспламенения, и интенсивности процессов горения при идентичных начальных условиях. Из полученных результатов видно, что широко используемый на практике черногорский каменный уголь не только воспламеняется дольше остальных составов, но и обладает наименьшей полнотой выгорания (рис. 6). Древесина лиственницы, наоборот, характеризуется наименьшими временами задержки зажигания. Таким образом, биомасса может использоваться в качестве добавки для интенсификации процессов зажигания и горения твердых ископаемых топлив (черногорского каменного угля). Данный вывод подтверждается результатами, представленными на рис. 6–10.
Рис. 6.
Кадры видеограммы зажигания и горения частиц черногорского каменного угля размерами 100–200 мкм в условиях движения в потоке разогретого воздуха при Ta = 700°С (Δt = 0.01 с): td = 0.095 с (a); t = td+∆t (б); t = td+2∆t (в); t = td+3∆t (г).
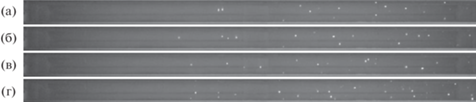
Рис. 7.
Кадры видеограммы зажигания и горения частиц древесины лиственницы размерами 100–200 мкм в условиях движения в потоке разогретого воздуха при Ta = 700°С (Δt = 0.01 с): td = 0.043 с (a); t = td+∆t (б); t = td+2∆t (в); t = td+3∆t (г).
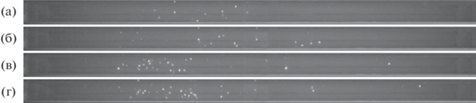
Рис. 8.
Кадры видеограммы зажигания и горения частиц смеси У 90% + Б 10% размерами 100–200 мкм в условиях движения в потоке разогретого воздуха при Ta = 700°С (Δt = 0.01 с): td = 0.079 с (a); t = td+∆t (б); t = td+2∆t (в); t = td+3∆t (г).
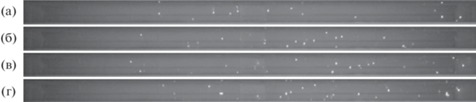
Рис. 9.
Кадры видеограммы зажигания и горения частиц смеси У 80% + Б 20% размерами 100–200 мкм в условиях движения в потоке разогретого воздуха при Ta = 700°С (Δt = 0.01 с): td = 0.063 с (a); t = td+∆t (б); t = td+2∆t (в); t = td+3∆t (г).
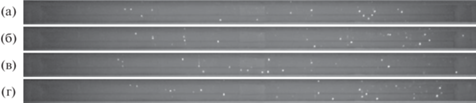
Рис. 10.
Кадры видеограммы зажигания и горения частиц смеси У 70% + Б 30% размерами 100–200 мкм в условиях движения в потоке разогретого воздуха при Ta = 700°С (Δt = 0.01 с): td = 0.052 с (a); t = td+∆t (б); t = td+2∆t (в); t = td+3∆t (г).
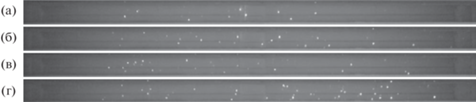
Удельная площадь поверхности топливных частиц играет важную роль в процессе зажигания и горения топлив. Чем больше углерода вступает в реакцию с окислителем (воздухом), тем топливная частица выгорает быстрее и полнее. Окислитель может проникать вглубь топливной частицы через поры, каналы, трещины и взаимодействовать с углеродом, но повышенное содержание летучих веществ в топливе может препятствовать этому в условиях интенсивного термического разложения. Чем выше содержание летучих веществ в топливе, тем дольше по времени протекает процесс горения частицы, так как их интенсивное выделение в условиях термического разложения препятствует проникновению разогретого окислителя в поры частицы.
3.3. Состав дымовых газов. На рис. 11 представлены средние значения концентраций антропогенных газов при протекании процессов горения угля, биомассы и их смесей в трубчатой муфельной печи при 800°С. Увеличение концентрации биомассы в составе смеси (от 10 до 30%) ведет к снижению содержания СО2 (на 2.2–13.5%) и повышению содержания CO (на 9.3–52.3%) в дымовых газах (рис. 11, а) по сравнению с аналогичным процессом сжигания угля без добавления биомассы. Максимальное среднее значение СO2 зарегистрировано для угля (2.30%), так как СО2 является основным углеродосодержащим газом в продуктах сгорания для угольных топлив. Диоксид углерода образовывался при расщеплении и преобразовании термически нестабильных карбоксильной (COOH) и карбонильной (=CO) функциональных групп. Также разложение органических (полициклических ароматических углеводородов, органических кислот) и неорганических веществ (CaCO3) приводило к формированию данного газа. Концентрация CO при сжигании биомассы максимальна (2.10%), что обусловлено пиролизом лигнина или вторичными реакциями разложения. Высокое содержание влаги в биомассе (см. табл. 1) снижает энергетические характеристики горения, калорийность топлива и увеличивает объем продуктов сгорания. В результате образуется больше продуктов неполного сгорания, в частности СО.
Рис. 11.
Состав дымовых газов при горении твердых топлив и топливных смесей при температуре 800°С: CO2 и CO (а); NOx и H2S+SO2 (б). Составы: 1 – У 100%; 2 – У 90% + Б 10%; 3 – У 80% + Б 20%; 4 – У 70% + Б 30%; 5 – Б 100%.
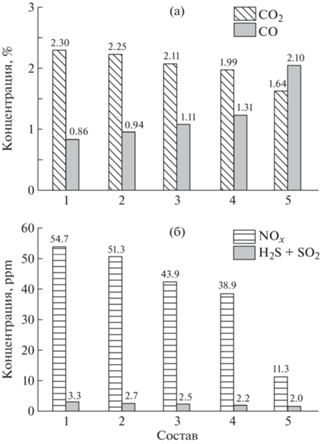
Средние значения концентрации оксидов азота, образующихся при сжигании исследуемых топлив, представлены на рис. 11, б. Наименьшие концентрации зарегистрированы при сжигании топлив с низким содержанием топливного азота, в частности, биомассы (содержание NOx составляет 11.3 ppm). Уголь в своем составе содержит больше азотистых соединений (табл. 1), что объясняет более высокие значения выбросов NOx, образующихся при его горении вследствие реакций [34]:
Сравнение концентраций NOx показало, что увеличение доли биомассы в составе смеси позволяет снизить выбросы оксидов азота на 6.2–28.9% по сравнению с углем. Наибольшая концентрация соединений серы (H2S+SO2) в продуктах сгорания характерна для угля (3.3 ppm), что происходит вследствие выделения наибольшего количества серы при ее сжигании (рис. 11, в), этот результат подтверждается результатами элементного анализа топлив (табл. 1). Относительно низкое содержание сероводорода в продуктах сгорания биомассы, по сравнению с другими составами, может быть связано с совместным протеканием процессов окисления сульфидов и химического взаимодействия окислов серы с гидроксидами железа и алюминия, а также с соединениями активных металлов (Me: K, Ca, Ba, Mg, Na), которые содержатся в большом количестве в биомассе: MeO + SO2 + 1/2O2 → MeSO4; MeOH + SO2 + + 1/2O2 → MeSO4 [35, 36]. При этом диапазон варьирования концентраций выбросов соединений серы (H2S+SO2) для разных топливных составов относительно небольшой (2.0–3.3 ppm).
Таким образом, добавление биомассы к углю способствует снижению концентраций выбросов диоксида углерода, оксидов азота, соединений серы. Результаты позволяют сделать вывод об экологической перспективности развития технологий сжигания топливных смесей на основе широко распространенных углей с добавлением биомассы в небольших количествах.
ЗАКЛЮЧЕНИЕ
В результате экспериментальных исследований для частиц черногорского каменного угля, древесины лиственницы и смесей на их основе (У 90% + Б 10%; У 80% + Б 20%; У 70% + Б 30%) определены характеристики процессов термического разложения и горения, а также состав дымовых газов. По результатам синхронного термического анализа установлена температура, при которой происходит воспламенение коксового остатка (для угля 421 и 294°С для биомассы), и температура, при которой происходит завершение процесса горения (для угля 570 и 484°С для биомассы). Времена задержки зажигания топлив в условиях конвективного нагрева при варьировании температуры окислителя в диапазоне 500–800°C изменяются от 0.02 до 0.22 с. Анализ состава продуктов сгорания позволил выявить содержание CO, CO2, NOx, H2S+SO2 для черногорского каменного угля (0.86; 2.30%; 54.70; 3.30 ppm соответственно) и древесины лиственницы (2.10; 1.64%, 11.30; 2.00 ppm соответственно).
Добавление биомассы к углю способствует улучшению экологических характеристик процесса горения без существенного ухудшения энергетических характеристик. По результатам сканирующей электронной микроскопии установлено наличие в частицах биомассы большого количества крупных пор и каналов в отличие от угля, что оказывает положительное влияние на интенсификацию процессов ее зажигания и горения. Среди рассмотренных топливных смесей состав с добавлением 20 мас. % биомассы является наиболее перспективным для практического применения наряду с широко распространенными твердыми натуральными топливами. Его теплота сгорания незначительно ниже аналогичной характеристики по сравнению с углем, а дальнейшее увеличение массовой доли в смеси приводит к снижению теплоты сгорания более чем на 10%. Добавление 20 мас. % биомассы к углю позволило снизить температуру, при которой происходит воспламенение коксового остатка, на 7%; температуру, при которой завершается процесс горения, на 1%; энергию активации на 16%; время задержки зажигания частиц в потоке разогретого воздуха на 38–43%; содержание диоксида углерода, оксидов азота и соединений серы (H2S+SO2) в дымовых газах на 8.3; 19.7 и 24.2% соответственно.
Список литературы
Yang W., Pudasainee D., Gupta R., Li W., Wang B., Sun L. // Fuel Process. Technol. 2021. V. 213. P. 106657.
Xia Y., Zhang J., Tang C., Pan W. // J. Energy Inst. 2023. P. 101191.
Ashraf A., Sattar H., Munir S. // J. Energy Inst. 2022. V. 100. P. 55.
Roni M.S., Chowdhury S., Mamun S., Marufuzzaman M., Lein W., Johnson S. // Renew. Sust. Energ. Rev. 2017. V. 78. P. 1089.
Vassilev S.V., Vassileva C.G., Vassilev V.S. // Fuel. 2015. V. 158. P. 330.
Madanayake B.N., Gan S., Eastwick C., Ng H.K. // Fuel Process. Technol. 2017. V. 159 P. 287.
Teixeira P., Lopes H., Gulyurtlu I., Lapa N., Abelha P. // Biomass & Bioenergy. 2012. V. 39. P. 203.
Agbor E., Zhang X., Kumar A. // Renew Sustain Energy Rev. 2014. V. 40. P. 930.
Sahu S.G., Chakraborty N., Sarkar P. // Renew. Sust. Energ. Rev. 2014. V. 39. P. 575.
Tillman D.A. Biomass & Bioenergy. 2000. V. 19. № 6. P. 365.
Ashraf A., Sattar H., Munir S. // Fuel. 2019. V. 235. P. 504.
Idris S.S., Rahman N.A., Ismail K. // Bioresour Technol. 2012. V. 123. P. 581.
Chen C., Qin S., Chen F., Lu Z., Cheng Z. // J. Energy Inst. 2019. V. 92. P. 364.
Glushkov D.O., Kuznetsov G.V., Chebochakova D.A., Lyakhovskaya O.E., Anufriev I.S., Shadrin E.Yu. // Appl. Therm. Eng. 2018. V. 142. P. 371.
Bhuiyan A.A., Blicblau A.S., Islam A.K.M.S., Naser J. // J. Energy Inst. 2018. V. 91. № 1. P. 1.
Gil M.V., Rubiera F. // New Trends Coal Convers. 2019. P. 117.
Рябов Г.А. // Энергетика за рубежом. Приложение к журналу “Энергетик”. 2022. № 3. С. 2.
Рябов Г.А. // Теплоэнергетика. 2022. № 6. С. 17. [Thermal Engineering, 2022, vol. 69, no. 6. p. 405. https://doi.org/10.1134/S0040601522060052]https://doi.org/10.1134/S0040363622060054
Coats A.W., Redfern J.P. // Nature. 1964. V. 201. P. 68.
Guo F., He Y., Hassanpour A., Gardy J., Zhong Z. // Energy. 2020. V. 197. P. 117147.
Yuan Y., Zuo H., Wang J., Gao Y., Xue Q., Wang J. // Fuel. 2022. V. 324. P. 124727.
Armakan S., Civan M., Yurdakul S. // J. Therm. Anal. Calorim. 2022. V. 147. № 22. P. 12855.
Liu Y., Tan W., Liang S., Bi X., Sun R., Pan X. // Biomass Conv. Bioref. 2022.
Chen L., Wen C., Wang W., Liu T., Liu E., Liu H., Li Z. // Renew. Energ. 2020. V. 161. P. 867.
Glushkov D.O., Matiushenko A.I., Nurpeiis A.E., Zhuikov A.V. // Fuel Process. Technol. 2021. V. 223. P. 106986.
Volkov R.S., Strizhak P.A. // Exp. Therm. Fluid Sci. 2018. V. 97. P. 392–407.
Antonov D.V., Kuznetsov G.V., Strizhak P.A. // J. Eng. Phys. Thermophys. 2020. V. 93. № 2. P. 1055.
Arkhipov V.A., Vasenin I.M., Trofimov V.F., Usanina A.S. // Fluid Dyn. 2013. V. 48. № 2. P. 143.
Arkhipov V.A., Boiko V.M., Goldin V.D., Maslov E.A., Orlov S.E., Poplavskiy S.V., Usanina A.S., Zharova I.K. // IOP Conf. Ser.: Mater. Sci. Eng. 2016. V. 124. № 1. Article number 012076.
Head A.J., Novara M., Gallo M., Schrijer F., Colonna P. // Exp. Therm. Fluid Sci. 2019. V. 102. P. 589.
Alekseenko S.V., Anufriev I.S., Dekterev A.A., Shadrin E.Y., Kuznetsov V.A., Sharypov O.V., Boyko E.E., Naumov I.V., Kabardin I.K. // Int. J. Therm. Sci. 2021. V. 161. Article number 106715.
Anufriev I.S., Kuibin P.A., Shadrin E.Y., Sharaborin D.K., Sharypov O.V. // Thermophys. Aeromech. 2016. V. 23. № 4. P. 621.
Akhmetshin M.R., Nyashina G.S., Strizhak P.A. // Fuel. 2021. V. 313. Article number 122653.
Zeldvich Y.B. // Acta Physicochimica. 1946. V. 21. P. 577.
Zhang Z., Chen D., Li Z., Cai N., Imada J. // Energy & Fuels. 2017. V. 31. № 2. P. 1383.
Guo F., Zhong Z. // Journal of Cleaner Production. 2018. V. 185. P. 399.
Zhao J., Wang T., Deng J., Shu C.M., Zeng Q., Guo T., Zhang Y. // Energy. 2020. V. 209. Article number 118494.
Дополнительные материалы отсутствуют.
Инструменты
Химия твердого топлива